How plasma electrolytic oxidation improves the corrosion performance of magnesium alloys
22 March 2022With its very low density, magnesium is increasingly specified by engineers looking to reduce weight. Unfortunately, this distinct benefit is negated by its propensity to corrode faster than heavier alternatives, in even the most ambient of conditions, and so until now, using magnesium has required some compromise. Keronite’s Plasma Electrolytic Oxidation (PEO) process uniquely improves the performance of magnesium, improving their corrosion performance, wear performance and enabling them to lighten the components they create.
Why does magnesium corrode?
Magnesium’s susceptibility to corrosion occurs despite the presence of an oxide layer. This outer film fails to adequately protect magnesium components in acidic and neutral environments, causing the surface to rapidly corrode and exposing the metal underneath to further attack.
When it reacts with oxygen from the air, magnesium loses two electrons to oxygen to form magnesium oxide: 2Mg + O2 → 2MgO
Corrosion is caused by this redox reaction. Magnesium is a group II element, so has two electrons in its valence shell. The number of valence electrons determines how reactive an element is, which in turn determines how easily the element will bond chemically with different atoms. Magnesium’s low ionisation energy means that the energy required for it to lose its two outer electrons can typically be found in ambient conditions. It easily forms oxides, hydroxides or sulphides and thus the corrosion process will begin relatively quickly.
By protecting magnesium components with surface coatings such as Keronite’s Plasma Electrolytic Oxidation (PEO), their corrosion resistance is greatly increased, opening up engineering applications for magnesium that would previously have been dismissed as too challenging.
What is PEO?
PEO is a method of producing strong and flexible surface coatings through the application of an electrochemical surface treatment to aluminium, magnesium or titanium. Components are exposed to liquid electrolyte and an electrical potential is applied to form an oxide-based ceramic.
How does PEO prevent corrosion?
Coatings formed on magnesium by plasma electrolytic oxidation broadly consist of three layers:
- A thin but dense interface layer between the coating and the underlying alloy
- A compact and hard middle layer
- A porous outer layer
These separate layers provide a magnesium PEO coating with its characteristic high adhesion, high wear and corrosion resistance, and ensure excellent binding to topcoats.
PEO coatings are highly conformal, resulting in extremely dimensionally precise coatings. The PEO process is further augmented with impregnation sealing, closing surface pores by bonding glass ceramic, polymer resin, ceramic polymer matrix and silicones as appropriate.
We have also developed Keronite coatings for use on reactive alloys where extreme corrosion resistance is required. In such environments, the innate problem of crevice corrosion is solved by creating a stabilised layer at the interface between alloy and ceramic coating.
Stringent tests have shown that PEO’s inert ceramic structure provides excellent natural chemical stability and corrosion protection:
- Single layer coatings can survive up to 648 hrs (alloy dependent) whereas Duplex layer coatings have exceeded 1800 hrs in Neutral Salt fog testing (ASTM B117)
- A coating of only 5μm is sufficient to protect ZE41A alloy unscathed for 6 hours in 5% NaCl at 80oC.
Corrosion resistance, coupled with other protective qualities
Using PEO gives magnesium alloys increased mechanical load tolerance whilst also keeping them flexible. Crucially this means that Keronite's coatings don't suffer from the cracking and flaking that many other treatments are prone to. In addition, PEO gives engineers solutions to a number of common material specification challenges, delivering:
- Corrosion protection
- Wear resistance
- Extreme hardness
- Strain tolerance
- Increased lifespan
- Electrical insulation
- Thermal and chemical stability
- Environmentally clean production (after pH adjustments, the electrolyte solution is safely flushed down the drain)
You can learn more about the specific benefits of plasma electrolytic oxidation for magnesium alloys in the technical data sheet.
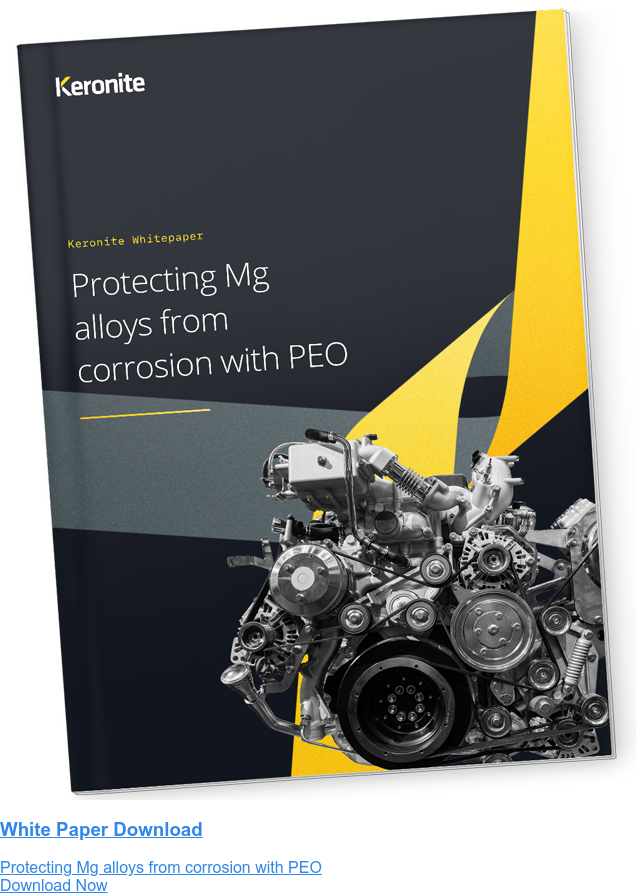
