How materials science is enabling a future with electric vehicles
21 March 2019The future of mobility is clear: electrification is the way to a greener, cleaner future. Manufacturers are now racing to replace gasoline-powered internal combustion engines (ICEs) with electric motors, powered by batteries or hybrid technologies.
Governments around the world have incentivised consumers to buy electric, through grants and similar tax incentives. While on the other side of things, governments have introduced hard deadlines on greenhouse gas emissions that manufacturers must comply with.
Despite these incentives, the market hasn’t gone head-over heels for electric vehicles just yet. Consumers aren’t yet convinced by their benefits and it’s not yet convenient enough to make the switch from gasoline to electric. A lack of charging infrastructure, poor range and lengthy charging times have all been attributed to the lack of market penetration of electric vehicles.
So has the industry bitten off more than it can chew? Fortunately, the materials science industry has been supporting manufacturers in their battle to get ultra-efficient, high-range electric and hybrid vehicle designs off the ground: by beginning electrification projects with close examination of their materials.
The state of lightweighting
Automotive companies have sought new ways to reduce the mass of their designs for decades. Most initiatives have been fruitful, with lightweight materials like aluminium, carbon fibre and reinforced plastics can now be found in a variety of passenger and commercial models.
Despite the huge investments in lightweight technologies, new features that are required in modern cars have come with a heavy price: more mass. Vehicles are now actually 50% heavier than they were in the 1980s. Heavy comfort and convenience features, bulky safety systems and sophisticated systems to reduce emissions all add to the total weight of a vehicle. In fact, the only area of the vehicle that has reduced in weight over this time has been the base structure.
Now, the introduction of electric and hybrid motors, hundreds of battery cells and bulky powertrains are added to vehicle mass at a time where manufacturers are desperately seeking ways to reduce it. For this reason, creating an ultra-light, electrified vehicle is something of an oxymoron under current technical possibilities. This is where new surface technologies could make a real difference.
Making the case to consumers
With fewer moving parts, purely electric vehicles have the potential to offer users exceptional levels of reliability and incredibly low maintenance costs. However, within hybrids, this simplicity has not been realised, in fact, they are heavier, laden with more components and their vastly more complex systems could actually increase the burden of maintenance.
In the short term, increasing the reliability of these components is an absolute essential to ensure they offer consumers value for money.
Rethinking the possibilities
To successfully electrify cars, vans and trucks, there are two key challenges that need to be overcome. Fortunately, both challenges can be overcome through collaboration between the automotive and materials science industries. These are:
- Lightweighting. Lightweight components allow the vehicle’s weight to be reduced, thus reducing the power requirements and increasing the range of a vehicles’ battery.
- Component life. Redesigning the motor vehicle has produced an endless number of opportunities to improve the performance of automotive systems. Reviewing the materials used within a variety of applications will allow them to last longer and perform better in tough operating conditions.
Is aluminium the material of the future?
Aluminium has come under the spotlight as more automotive manufacturers seek ways to lightweight their electric vehicle designs. The added benefits are also appreciated: it’s low production and machining costs make these vehicles more affordable, too.
Take battery enclosures, for example. In 2018, a few vehicle manufacturers began to install aluminium battery enclosures to sit atop of the powertrain, not too dissimilar to a skateboard. Aluminium is a perfect option as its thermal management properties allow for effective battery cooling. However, it’s natural tensile strength is comparatively low, making a suitable choice of surface coating essential to their use.
The case for light alloys
While light alloys are now used extensively in modern vehicle designs, their natural characteristics have prevented their use in more challenging applications. Take magnesium, the lightest structural metal. It has received a surge of interest from the automotive industry due to it’s impressive strength-to-weight ratio. However, Mg is still considered unsuitable for many applications due to its vulnerability to pressure under tension. But with advanced coatings, materials scientists are challenging long-held preconceived notions about the material.
Magnesium alloys, for instance, are often selected on their natural corrosion resistance. Even then, magnesium alloys need to be suitably protected from galvanic corrosion. To enable the use of magnesium, high performance, ultra-scalable surface coatings like plasma electrolytic oxidation (PEO) have become the natural choice for enhancing light alloys.
The lightweight ceramic coating produced by PEO greatly increases the tensile strength of magnesium. The degree of control provided by the Keronite technique means a variety of different coatings can be created, according to the porosity and chemical compatibility that works best for the particular industrial application and individual alloy.
A new research agenda
If parts are lighter, they require less energy to move; less mass, less gas. This makes them greener, more economical, more portable and, ultimately, more efficient.
New research into plasma electrolytic oxidation (PEO), led by Keronite, has made it possible to substitute traditional materials such as steel for lightweight alternatives which significantly reduce the weight of vehicle assemblies.
For automotive applications, there are clear benefits to reducing weight and increasing life within these applications:
- Electric motors and moving components.
- Battery castings and other heat-sensitive components.
- Brake systems and brake discs.
- Large-cast external body panels.
- Weight-bearing components.
- Components in moving applications facing dry sliding wear.
Keronite are working with a number of leading automotive manufacturers to develop coating solutions for a variety of challenging applications. To learn more about how we develop the world’s most advanced surface coatings, read our article on the plasma electrolytic oxidation process.
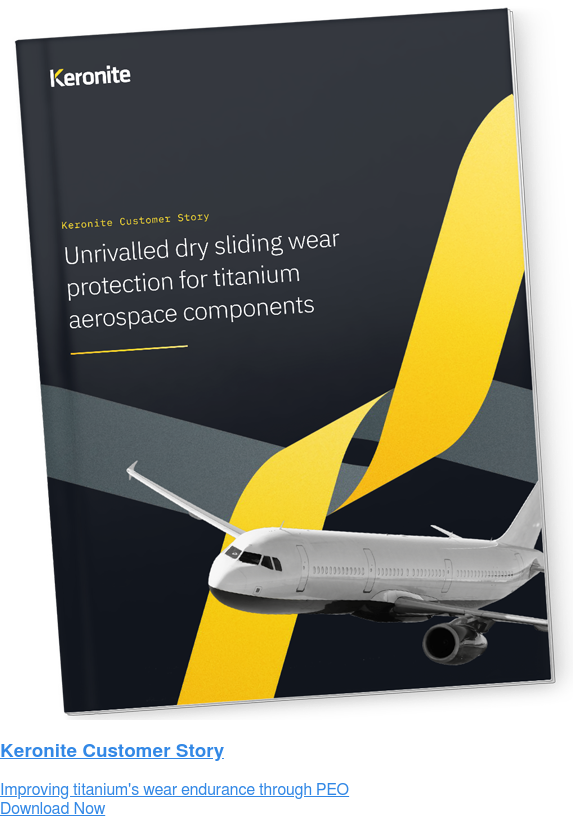
