Future technologies call for high dielectric strength coatings
7 September 2022The global economy is on the cusp of radical change. Influenced by efforts to reduce carbon emissions, our increasing electric power consumption is driving new tech trends: like manufacturing automation and robotics, in the hope of a safer and more efficient future. The question engineers now face is which challenges arise from such a huge leap in technology?
With higher voltages and temperatures, these technologies create new safety and performance concerns. More power electronics in small spaces equals more heat, which, if not transferred, could radically reduce the lifespan of new technology.
For years, materials scientists have had to focus their attention on protecting from dielectric breakdowns or thermal management exclusively. Thankfully, behind the scenes, Keronite’s scientists have been working hard on advancing surface technology to keep ahead of the curve.
Improving dielectric properties for the future
With the right surface technology, dielectric breakdown strength can ensure safe electrical insulation. If you consider the various emerging technology trends, increased power requirements will create new safety concerns.
Dielectric strength is important in preventing dielectric breakdowns from causing further harm. Dielectric breakdowns occur when an insulator becomes electrically conductive, potentially damaging on-board electronics and nearby components. This occurs when electrical currents flow through the insulator when the voltage applied across exceeds the breakdown voltage. If surfaces offer limited dielectric breakdown protection, they can create drastic safety and performance concerns.
Heat sinks will become an important factor
Another challenge to the electrification trend is in thermal management. In power electronics, the conversion of energy raises temperatures to a level that could damage components working in close proximity. While heat is an inevitable by-product of electrical energy conversion, the important thing here is to ensure the materials aid heat dissipation, rather than worsening the thermal properties.
Managing heat levels is an industry-wide concern. The innovation of thermal management technologies is forecasted to become a $16bn dollar industry by 2024. This is in part due to the increased development of sustainable and electrified technologies. New applications face difficulties in managing heat between interconnected parts placed closely beside each other. With such small gaps between each component, the damage from overheating is an issue that is being taken seriously in materials science.
Innovative surface technologies may hold the solution
With the right choice of surface technology, dielectric breakdown strength and thermal management properties can work together in unison. For materials that need to manage their thermal levels, Plasma Electrolytic Oxidation (or PEO) has shown to be successful. PEO already provides a form of electrical insulation on its surface, but also offers materials engineers high dielectric breakdown strengths of up to 26kV. This prevents the current from breaking through into the rest of the product.
This is a major advantage, particularly as most industries electrify. Not only the automotive sector, but also planes, and other machinery. What they also share in common is a move towards more compact designs. That a PEO coating can prevent the transmission of electric currents between close components, means greater insulation and a longer life-span all around.
PEO offers material scientists the chance to practically mould the coating to their temperature requirements. During the anodic bathing process, scientists have formed coatings for thermal transmission (0.8 – 10w m-1 k-1) and produced thermal barriers that can withstand temperatures of greater than 900 °C. The versatility of the technique means that there is scope to drastically improve the performance beyond these levels.
Conclusion
Engineers will face numerous challenges as technologies electrify, including managing higher levels of power and heat. We are using more power today than ever, and therefore producing more heat within a smaller form factor.
Keronite’s scientists have managed to work out a number of ways to keep you a step ahead. Using plasma electrolytic oxidation, we create bespoke surface technologies to form coatings that match the exact requirements for your application. Whether it is for drone technology, a hybrid vehicle, or a plane, each will require a unique coating to have it working effectively, ensuring that everything works optimally.
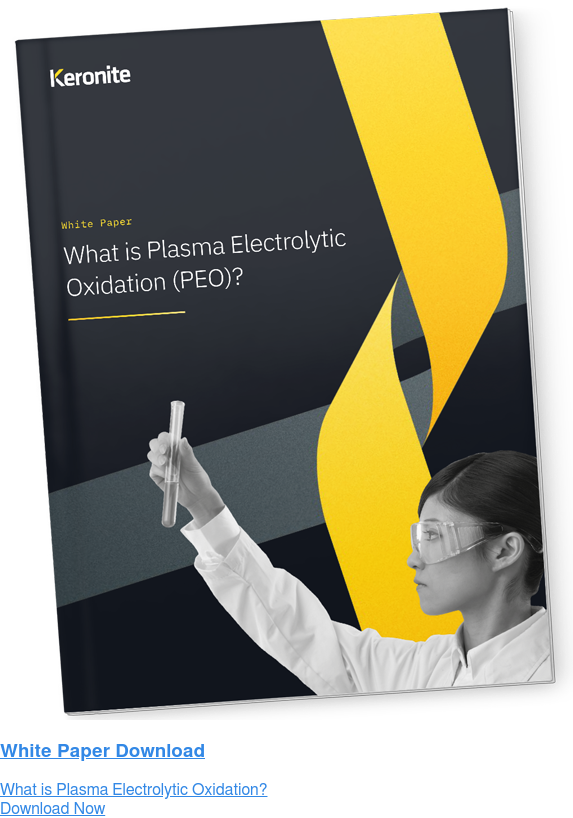
