Corrosion resistance for industrial tooling in food and beverage
15 December 2020Bulk, high volume food and beverage production is one of the harshest manufacturing environments for industrial tooling and machinery. Often, what ends up on our plate and in our glass has been on a lengthy processing journey to ensure it is appetising, looks good, is convenient and is safe to consume.
Hot corrosive liquids, syrups and chemically active ingredients, abrasive raw materials, high temperatures and exceptionally high speeds are common elements to food and drink production. And some production processes require surprisingly delicate handling and mixing. As many food and beverage processes operate on high volume low profit margin mass production models, production and process engineers look for efficiencies in every step.
This combination of high performance under demanding conditions and optimising efficiencies means engineers often specify light metals, such as aluminium and its alloys, as tooling and machinery components. Properties such as high strength to weight ratio, thermal conductivity and ductility make light metals, with the right surface coating, optimal choices for industrial tooling in food and beverage production.
What industrial tooling and machinery is used in food and beverage production?
Most food processing and production is batch or continuous process and includes multiple stages. The scope of tooling and specialist machinery is huge, used to prepare, handle, process, cook / refrigerate / freeze, store and package food and beverage products. The products also need transporting, which typically requires high speed conveyors.
The first stage can often be preparing the raw materials, for example washing with saline solutions, heat and steam treatments for peeling, or mechanically sorting raw materials such as fruit according to size, colour and odour. Sorting may require delicate machinery and conveyors that can operate at high speeds. Agricultural goods, such as cereals, are highly abrasive, and have naturally acidic or alkali properties, so can be extremely corrosive, especially when the process includes heating and boiling.
Liquids can be found in many food and beverage production processes. Common high-volume industrial processes are brewing and soft drink manufacture, but others involving liquid ingredients include industrial scale sugar product production, confectionery and baked goods. Some fruit juices can have a pH as low as 2.7, which can be highly corrosive over time. The sorting machinery and conveyors must operate efficiently, delicately, at high speeds and withstand corrosion and abrasion.
Alongside the sheer scope of specialist tooling and range of raw materials, ingredients and operating conditions, is the need to be food safe. There are various hygiene regulations and standards, which can require food grade machinery to have antimicrobial and hydrophobic properties for self-cleaning.
PEO surface coatings for corrosion resistance of light metal tooling
Aluminium and its alloys are used throughout the food and beverage sector. Being chemically active, aluminium and its alloys are naturally corrosion resistant because they form an aluminium oxide surface coating when exposed to air that has ceramic-like properties. However, this coating does not provide sufficient protection from harsh, corrosive food and beverage applications.
Plasma electrolytic oxidation (PEO) is a surface coating technology that offers multiple solutions for materials and process engineers specifying food and beverage tooling. It uses an electrolyte bath and plasma over three distinct stages to form a ceramic-like duplex coating on light alloys.
Each of the three stages creates opportunities to uniquely adjust processing parameters to create bespoke coatings for the precise needs of the tooling component application. The multi-layered coating’s top layer is also highly porous. In addition to the substrate, uniquely, PEO incorporates the contents of the electrolytic bath in the surface coating.
PEO’s fine microstructure and surface texture create an ideal physical ‘key’ for top coats – resulting in much stronger adhesion of the top-coat than with hard anodised solutions. Such “duplex” systems combine the improved corrosion protection of both components in a synergistic way, resulting in unparalleled corrosion protection, and further extending the life of components.
The duplex layer and ability to introduce other properties enables engineers to specify additional properties. Wear resistance enhanced with hydrophobic coatings are desirable because they provide self-cleaning, antifogging and antifreezing properties, and help with corrosion resistance. Thermal barrier coatings can be introduced by using silica-rich electrolytes. Introducing titanium dioxide and additives into the electrolyte makes the PEO coating photocatalytic and therefore anti-microbial.
Finally, PEO is simpler and more straightforward to apply than many surface coatings and is suitable for bulk processing. As a result, large volumes of components can be coated cost effectively for food and beverage processing equipment.
To find out how PEO coating your food and beverage tooling and components can deliver competitive advantage for your business, download the whitepaper below or contact our team today.
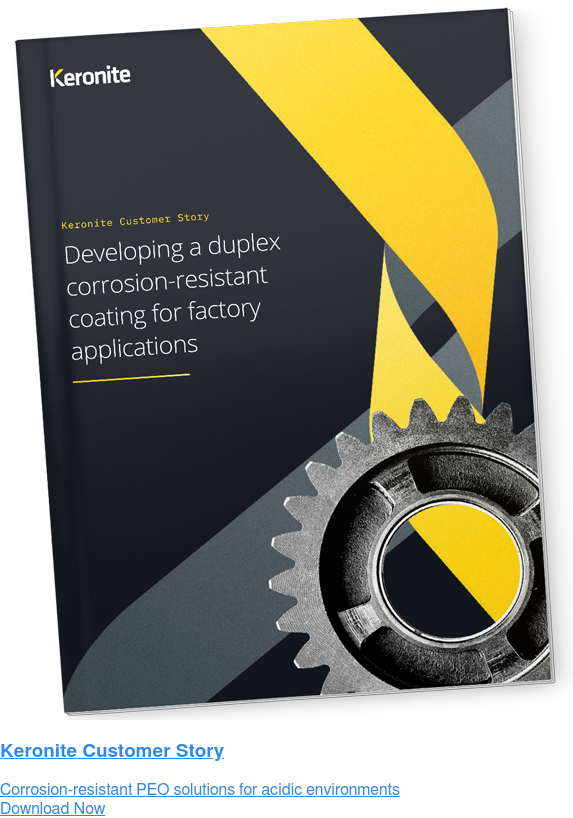
