Aluminum vs magnesium: which is best for industrial applications?
12 December 2023Aluminum and magnesium are two of the most popular light metals when it comes to lightweighting industrial designs. They each provide unique properties that benefit specific applications, but also have their own weaknesses in different environments.
In this article, we examine the properties of aluminum and magnesium relative to their industrial applications. Then we unpack their specific weaknesses and how these can be overcome through advanced coating solutions.
Aluminum for industrial applications
Aluminum is a well-established light metal that has seen widespread industrial use since the mid 20th century. Its popularity can be attributed to its lightweight features that reduce the cost and weight of designs without significant sacrifices to tensile strength.
Properties of aluminum
- Strength-to-weight ratio - Aluminum has a respectable tensile strength of approximately 70-111 MPa considering it has a density of 2.7 g/cc. This can be enhanced via alloying, with the highest series (7000) reaching an impressive 750 MPa.
- Natural corrosion resistance - Aluminum has a natural oxide film that protects the metal from natural corrosion. In conditions without high temperatures, humidity and/or corrosive elements, aluminum components are sufficiently protected.
- Thermal conductivity - Aluminum has a high thermal conductivity at 210 W/m-K whilst maintaining good mechanical stability at temperatures of around 100°C. This makes it perfect for heat dissipation.
Suitable applications for aluminum
Structural lightweighting
Aluminum is widely used for structural components due to its high tensile strength that is accompanied by low density. By reducing the structural weight of industrial applications, engineers can greatly reduce the cost and fuel efficiency of designs.
Automotive frames, aerospace fuselage and ship hull components commonly consist of aluminum, with many more integrations being made year on year to reduce weight.
Cooling
The high thermal conductivity of aluminum makes it extremely useful for cooling applications. Dissipating heat away from thermally vulnerable components can both extend their lifespan and reduce costs that would otherwise be spent on thermal insulation.
Electronic heat sinks, cooling fins in vehicles and cooling fans in aerospace applications all provide heat dissipation from vulnerable components. They help improve functionality, reduce costs and maximize component lifespan.
Key weaknesses of aluminum
Friction-induced wear
Aluminum has a low hardness compared to heavier metals like steel that are used for neighboring components in many automotive and aerospace applications. This can result in friction-induced wear that can greatly reduce the lifespan of components if not properly addressed.
Limited performance at high temperatures
Even though aluminum has an impressive thermal conductivity, temperatures exceeding the 100°C - 150°C limit can lead to plastic deformation in the metal. This is where the mechanical strength of the metal is permanently reduced, making it difficult to integrate into high temperature environments.
Magnesium for industrial applications
Magnesium is an exceptionally abundant, lightweight and interesting metal in the context of modern engineering. It showcases some unique features that can greatly enhance industrial designs, but has some integration limitations at the same time.
Properties of magnesium
- Lightest structural metal - Magnesium is the lightest structural metal on the planet at a density of 1.7 g/cc. It also showcases excellent castability, making it excellent for lightweighting purposes.
- Vibration dampening - Magnesium has natural vibration dampening features as a result of the high mobility dislocations within the metal. This can reduce vibration-induced wear for specific applications and provide unique capabilities for others.
- Electromagnetic shielding - Magnesium also has natural electromagnetic shielding capabilities that can be utilized in electronics and related industries to isolate and protect specific components from interference.
Suitable applications for magnesium
Electronics
Magnesium is regularly used in modern technology due to its lightweight and electromagnetic interference (EMI) resistant properties. This enables laptops, phones and other electronics to be lighter whilst shielding sensitive components from interference.
By integrating magnesium, electronics manufacturers can reduce the costs of designs that would otherwise be spent reducing weight and creating dedicated EMI shielding components.
Component lightweighting
Magnesium is used in specific components that can take advantage of its unique properties and reduce the overall weight of designs. The vibration dampening features and simple castability make this process simple, leading to reduced costs and significant weight reductions.
Magnesium is used in a wide variety of specific components across industries. Helicopter rotor blades, gearbox casings and biomedical devices all take advantage of the vibration damping and reduced weight of the metal.
Key weaknesses of magnesium
High susceptibility to corrosion
Magnesium is an extremely reactive metal with a relatively weak outer oxide layer. This makes it extremely susceptible to almost every form of corrosion in ambient conditions: such as uniform, calvanic, pitting and stress corrosion. This quickly leads to mechanical failure, resulting in unalloyed magnesium being impossible to integrate in even slightly corrosive environments.
Low fatigue and yield strength
Magnesium has a low fatigue and yield strength that severely limits component life. Even when alloying magnesium, common manufacturing defects such as shrink holes and oxide inclusions fail to provide sufficient fatigue and yield strength. This makes it difficult for magnesium to be properly integrated in high fatigue environments.
PEO - a holistic solution to integrating aluminum or magnesium
Aluminum and magnesium are interesting light metals that provide unique features for reducing the weight of different applications. That said, they each face a number of integration challenges in high thermal, corrosive and abrasive environments.
Plasma Electrolytic Oxidation is an advanced surface coating solution that provides light metals such as aluminum and magnesium with protective characteristics. It consists of an electrolyte bath solution where plasma discharges produce a resistant ceramic outer layer on the metal’s substrate. This provides a wide range of protective characteristics for magnesium and aluminum to reduce the weight of designs and extend the lifespan of components.
To find out more about PEO and how it can optimize your designs, contact a member of our team today.
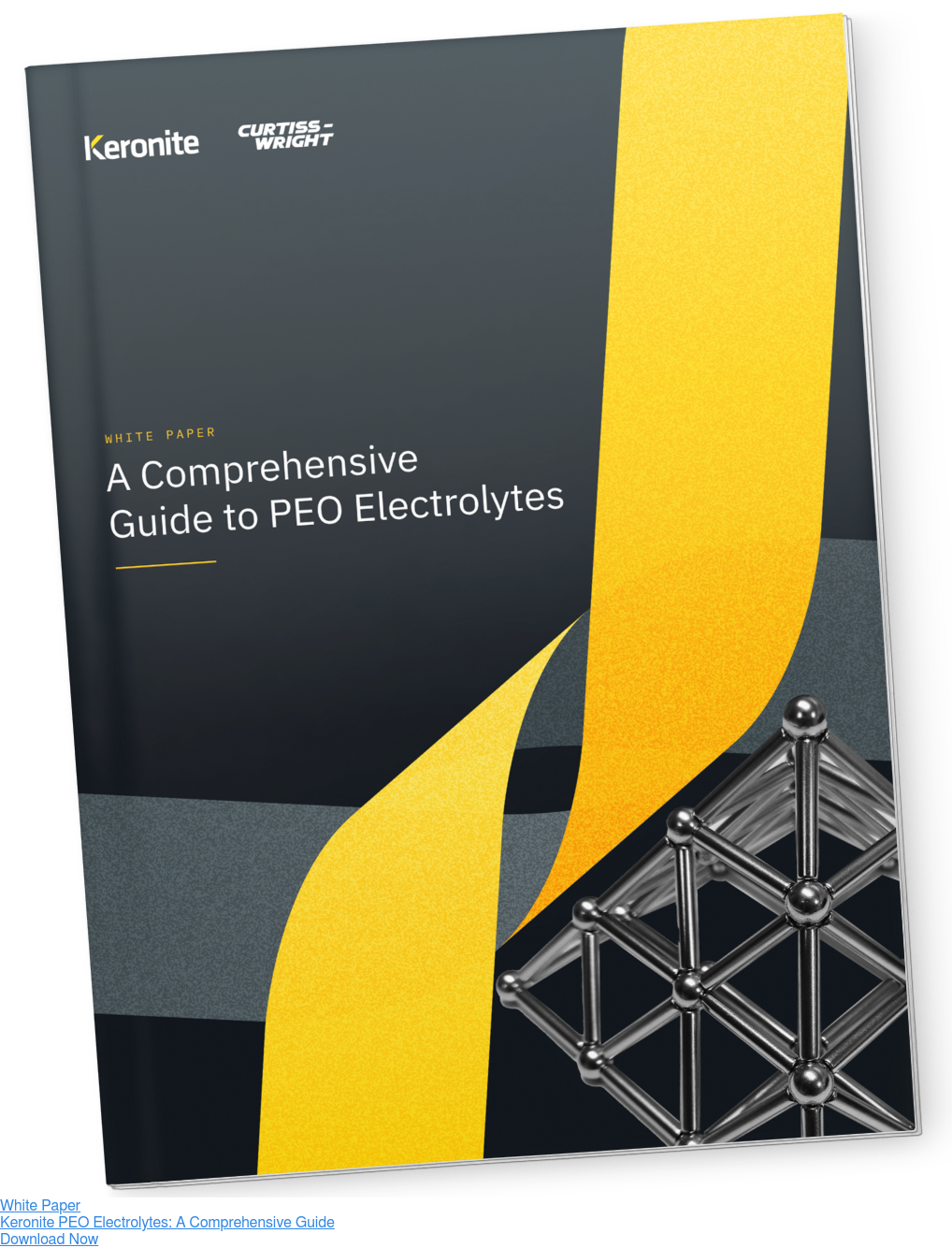
