Aluminium in internal automotive components: enhancing wear resistance
6 February 2020In the face of an environmental crisis, the automotive sector is on a reinvention mission. To avoid fines, manufacturers are seeking to make lighter, more efficient vehicles. Many of these vehicles are being powered by alternative means of propulsion.
Automotive manufacturers are doubling down on lightweight technologies. Materials scientists are finding more ways to make conventional components lighter. All while manufacturers introduce new systems that aim to reduce fuel consumption. Hybrid vehicles introduce secondary motors, as well as other components – adding weight in the process. Adding battery cells also adds a significant weight burden on vehicles.
Enter: aluminium. Recent advances in materials science are enabling the light alloy to be used as an outright replacement for steel and other heavy metals.
Replacing steel
In terms of strength, steel is almost unrivalled. This makes steel the obvious choice of material in automotive applications that involve wear. Globally, 12% of all steel is used in the automotive industry.
But this is changing. Despite its undeniable advantages, new materials technologies are capable of enhancing much lighter materials, such as aluminium. In many cases, these materials can offer a like-for-like replacement in terms of strength and wear. But light alloys high strength-to-weight ratio offers the opportunity to reduce weight all the while. In a study by MIT, it’s estimated that a 10% reduction in a vehicles’ overall weight improves the fuel economy of the motorcar by 6-8%.
Light alloys offer a promising solution, although their tribological performance poses a number of concerns for automotive manufacturers.
Advancing aluminium surface technologies
Materials scientists are working to improve the tribological performance of light alloys. Ceramic layers are producing interesting results in lab experiments. Technologies like plasma electrolytic oxidation (PEO) are capable of drastically improving the wear performance of aluminium, in a number of interesting ways.
PEO coatings are widely regarded as ultra-hard. However, the microstructure of the coatings also contribute to their wear performance. Unlike anodising, coatings created by PEO are non-columnar, which means that they offer a degree of compliance.
Recent research by materials scientists at Keronite and the University of Cambridge have highlighted several key factors for the efficacy of surface coatings on light alloys in an automotive context:
Coating thickness in improving wear performance
One of the key considerations is the thickness of the ceramic coating light alloys. While a thicker coating may be beneficial, Keronite’s proprietary research highlights the importance of ingrowth on conversion coatings.
Surface coatings that convert and consume the substrate are demonstrably denser. Ingrowth also strengthens the adhesion between the coating and the substrate, further improving wear performance.
Surface roughness for improving dry sliding wear
In applications involving dry sliding wear, surface roughness plays a role in determining the longevity of a component. Smooth coatings with visual uniformity also enable wear performance, smoother coatings have a higher coefficient of friction. In the example application reviewed by Keronite and the University of Cambridge – a suspension system – dry sliding wear was a common mode of failure.
Surface coating compositions
Advanced surface coatings like plasma electrolytic oxidation can incorporate elements of the electrolyte or even suspended particles within the resulting coating. This enables PEO coatings to gain atypical characteristics. Keronite’s scientists have invested significant time into experiments involving sealers and other duplex coating mixtures to find the best solution for wear.
Every automotive system brings with it a unique mixture of challenges for materials. In order to optimise components for performance, a coating that offers substantial protection from wear – in the forms that affect the component most.
The results?
Keronite’s materials scientists have published their research in a new paper entitled ‘Evaluation of Wear Performance of Plasma Electrolytic Oxidation Coatings on Aluminium’. This paper investigates the wear performance of alumina-rich plasma electrolytic oxidation (PEO) coated 6082 Aluminium cylindrical bore, which could potentially replace the use of chrome coated steel.
To download the full paper, click below. For more information about our research, get in touch with our technical team today.
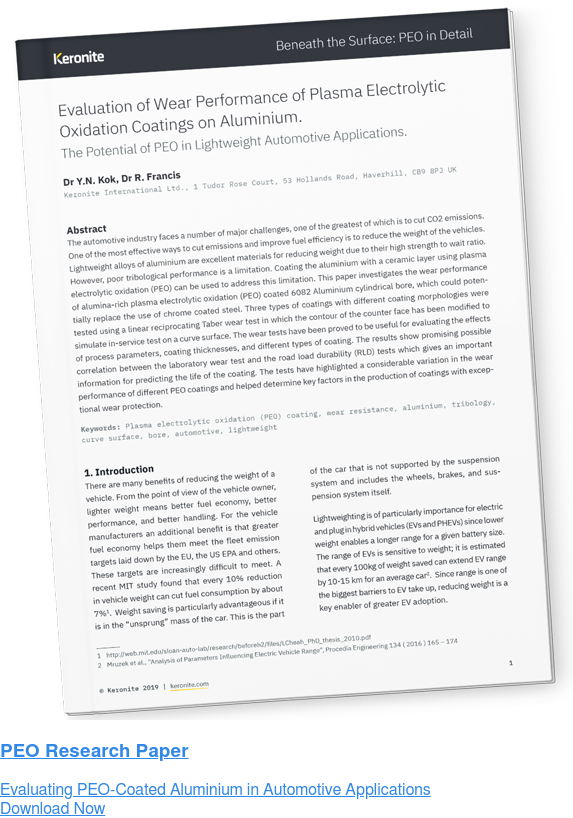
