What role do light alloys play in the electric vehicle infrastructure revolution?
6 December 2021Auto manufacturers have proven there’s a market for electric vehicles. More than 3 million were on European roads at the end of 2020. The next challenge is clear: how do we ensure that the charging infrastructure scales alongside EV sales? There are two requirements, both as necessary as one another:
- Improve the performance of charging stations – ensuring that they deliver faster charging times that enable drivers to get to their destinations with less frequent, faster charging, stops.
- Scale the infrastructure. By making supporting technology easier to manufacture and produce, whilst remaining reliable and robust, we need to ensure that chargers are available to support adoption.
Rapid construction of this high-quality EV infrastructure can only be achieved with the right combination of materials and components with fit-for-purpose properties, including light metal alloys of aluminium and magnesium.
High power requirements: a materials challenge
Electric vehicle charging infrastructure is one of the key factors slowing the adoption of ultra-low emission EVs. For many drivers who don’t have access to a private driveway or parking space at home, the lack of public charging points means electric vehicles are not an option. In the UK, the Committee on Climate Change (CCC) projects that approximately 280,000 EV charging points will be required by 2030.
As well as the high volume of charging points required for EVs, the power supplied by these chargers must increase. Many existing charging points are classed as slow, 3-7kW AC, used for home charging or fast, 11-22kW AC, installed in commercial areas such as car parks. The installation of rapid 50kW DC and ultra-rapid 100kW DC points is expected to increase significantly over the next decade.
To facilitate these improved charging speeds for EVs, specialist charging equipment and dedicated high-powered connections are required. Due to their relatively low cost, good electroconductivity and excellent strength-to-weight ratios, light alloys are good candidates for metal components within EV infrastructure. Aluminium and magnesium alloys are versatile materials that can be insulated with dielectric coatings to enhance the safety and efficiency of electrical components.
Dielectric coatings for high voltage cabling
Most overhead power lines supplying high voltage electricity are now produced from aluminium. Aluminium has replaced copper as the main conductive element in power cables, often reinforced by a steel or composite core. Aluminium alloys are significantly cheaper than their copper equivalents and have a higher conductance. This means that more electricity can be transmitted using the same level of infrastructure - exactly what is required to support future EV charging infrastructure.
To improve efficiency, ensure safety, and reduce the risk of equipment failure, dielectric coatings are used to insulate the conductive materials within power cables. Dielectric coatings are electrical insulators. These coatings are often thin film ceramic coatings or polymers and require finely tuned application techniques to ensure a uniform protective film across the metal’s surface, which must be completely free of pinholes, cracks or voids. They must also withstand high temperatures, especially where high-voltage power throughput is required.
Types of dielectric coatings
Dielectric coatings are characterised by their dielectric strength. This indicates the maximum electric field that the material can withstand without suffering electrical breakdown. Aluminium oxide, which forms naturally on the surface of aluminium alloys, has a dielectric strength of approximately 15 kV/mm. This can be increased to up to 79 kV/mm using an advanced dielectric surface coating. There are several technology options for commercially available dielectric coatings:
1. Ceramic sol–gel composite coatings
Electrically insulating coatings can be produced by applying fine ceramic powders based on alumina and silica dispersed in a sol-gel solution. Sol-gel coatings can be applied by spin or dip-coating and typically require a series of drying or heat-treating processes to cure the surface coating.
2. Thermal spray coatings
This method involves superheating the coating particles to generate droplets that are spray applied to the metal substrate. This allows ceramic-based coatings to be applied to a wide range of metal substrates, including aluminium oxide and magnesium aluminate. But as with conventional spray application techniques, achieving uniform coverage across complex geometries can be difficult.
3. Polymer nanocomposites
Polymer nanocomposites for dielectric coatings are typically polymer matrices with nano-scale filler particles. These coatings are currently in the development stage and work best for small-scale applications.
4. Plasma electrolytic oxidation (PEO)
PEO coatings are an innovative method of applying dielectric coatings to light alloys. The application process is straightforward and involves immersing the component in an electrolyte bath and passing a current through the alloy. The voltage sequence and composition of the electrolyte bath can be altered to create the desired coating properties. PEO creates a uniform ceramic coating at the metal’s surface that can be tailored to achieve specific microstructures, surface properties, or coating thicknesses. This versatile coating method works well for complex geometries as the component is fully immersed in the electrolyte solution.
Dielectric strengths between 59 – 79 KV/mm can be achieved using this type of advanced surface coating. PEO coatings can also provide additional wear resistance, corrosion resistance, and thermal stability, allowing light metal alloys such as aluminium and magnesium to be used in a wide range of industrial applications.
For more information on PEO coatings for light metal alloys and how they can be used to develop low-cost, lightweight components for EV infrastructure, get in touch with our team.
Keronite’s coating development team and expert materials scientists can work alongside your project team to create PEO coatings which meet bespoke design criteria for your EV infrastructure project.
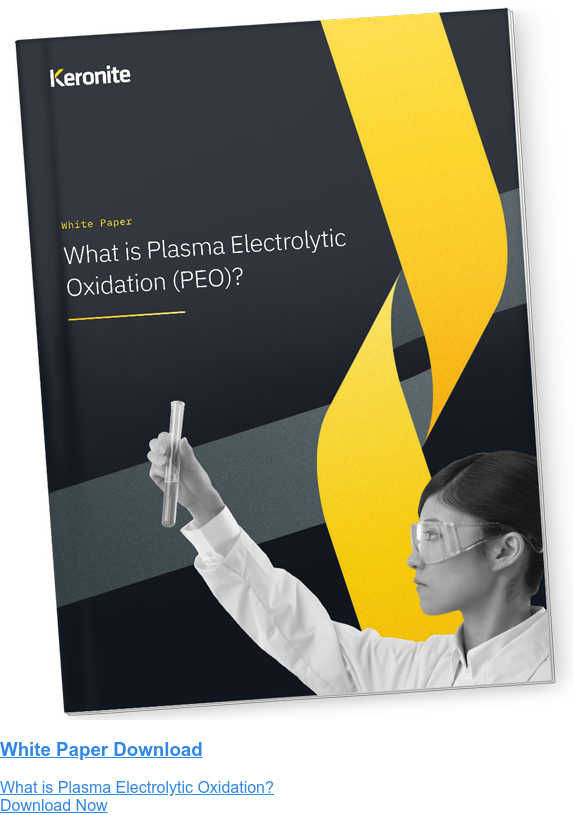
