What is Plasma Erosion?
11 May 2020Plasma erosion refers to the degradation of materials which are in frequent contact with plasma. Light alloys and other materials can suffer from chemical corrosion, surface cracking, blistering and embrittlement, which can drastically reduce the service life of components used in plasma processing equipment.
Plasma has hundreds of potential applications. From water purification, sterilisation, surface passivation, to semi-conductor processing. But as plasma use increases, the need to make these processes cost efficient and long-lasting becomes more important, and the demands on materials used become more extreme.
Plasma erosion is a mode of wear created specifically by plasma. This occurs where surfaces corrode, crack, blister or even become more brittle due to continued contact with plasma. Keronite has investigated this phenomenon widely, with real progress being made to protect light alloys from plasma erosion. In this article, we’re going to review why plasma erosion occurs, how to stop it, and examine how the right surface coating can extend the life of materials with plasma contact.
What causes plasma erosion?
Plasma is an ionised gas, whereby orbital electrons have been removed when subject to a high energy input, for example a strong electric field. Plasma is highly conductive, usually hot and sensitive to magnetic fields. To utilise plasma in industrial applications highly specialist equipment is needed. Unfortunately, the very nature of plasma means that this equipment tends to erode, sometimes at a remarkable rate.
There are several underlying causes of plasma erosion. These include sputtering, unipolar arcs and heat pulses. These processes cause surface evaporation, chemical corrosion, changes to the surface structure and morphology, and implantation of atoms from the plasma.
- Sputtering is the loss of microscopic amounts of a material from a substance as a result of bombardment by high energy particles. The ionised particles in a plasma collide with the material and the energy released by the collision can result in the material ejecting atoms.
- Unipolar arcs can be formed as a result of electric field differentials between the plasma and the material. The arcs release significant energy that causes localised material loss at the point of arc-solid interaction. Craters are often formed in the material’s surface structure.
- Heat pulses are generated by instabilities in the plasma. These intense bursts of energy cause localised melting and evaporation of the material. The heat pulse can also cause internal stresses within the material. The material loss due to evaporation, alongside the melting and structural stresses, impact on the material’s performance characteristics.
- Gas implantation occurs when ions and neutral atoms from the plasma can lodge within the atomic lattice of the material. This process can form interstitial defects and alter the surface structure, composition, and properties of the material. If a sufficient concentration of the interstitial defects occurs they coalesce into small bubbles, or humps, on the material’s surface. This blistering can cause the solid material to flake.
- Chemical corrosion/erosion is principally caused by highly reactive chemical species that are formed in the plasma. These react with the surface forming volatile species, further contributing to materials loss. At higher temperatures, chemical erosion through the loss of volatile compounds occurs at a higher rate than sputtering.
What’s the impact of plasma erosion?
Plasma handling requires highly specialised equipment. Due to the effects of plasma erosion, plasma equipment typically has a short life. For the life sciences industry, for example, this makes the cost of replacing equipment and repairing equipment expensive – forcing some to consider alternative options.
Putting the above into context, if a material is in contact with a plasma during the many industrial processes that use plasmas, it can be fundamentally damaged. If used in a critical application, that material could perform in unexpected ways and fail.
Many high performance applications in sectors such as aerospace, space, industrial and consumer goods use plasma processes. An understanding of plasma erosion and its impact is essential for engineers who use materials that have undergone plasma treatments.
Protecting light alloys from plasma erosion
One way of protecting components is to treat their surfaces with a suitable coating. Such a coating should:
- Be extremely chemically stable to resist corrosion/erosion by reactive species in the plasma.
- Be thermally stable to withstand the effects of localised heating and heat pulses.
- Have a high dielectric strength to protect against arcing.
- Resist particle shedding even under the impact of high energy particles.
- Be highly pure to avoid the possibility of any contaminants being transported onto downstream equipment.
- Be well adhered to the substrate to resist blistering and detachment.
Keronite’s PEO coatings meet these requirements. For example, our plasma protection coatings on aluminium are almost pure alumina (aluminium oxide), an extremely chemically and thermally stable material with a very high dielectric strength. Further, since they are grown via direct conversion of the substrate they are extremely well adhered. Keronite has collaborated with leading plasma science companies over many years, and made several discoveries in the field of plasma erosion. With an advanced surface coating, plasma handling surfaces such as discharge channel walls can last longer and perform better.
Summary: Protecting equipment from plasma erosion
Plasma erosion causes:
- Material loss through sputtering, unipolar arcs, heat pulses, flaking and chemical erosion
- Surface cracking through chemical reactions on the material surface caused by ion bombardment and resulting interstitial defects changing the composition of the material
- Embrittlement resulting from chemical reactions caused by interstitial defects that change the composition of the material
- Blistering on the material surface as a result of the interstitial defects concentrating into subsurface bubbles that can develop into flaking.
The above effects can cause premature failure of equipment used in plasma processing. This can be prevented by the use of suitable coatings. Keronite’s PEO coatings have ideal properties for protecting against plasma erosion.To learn more, get in touch with our materials science team at keronite.com/contact or info@keronite.com. Or, to read more about our advanced surface technology, Plasma Electrolytic Oxidation (PEO), download ‘What is PEO?’
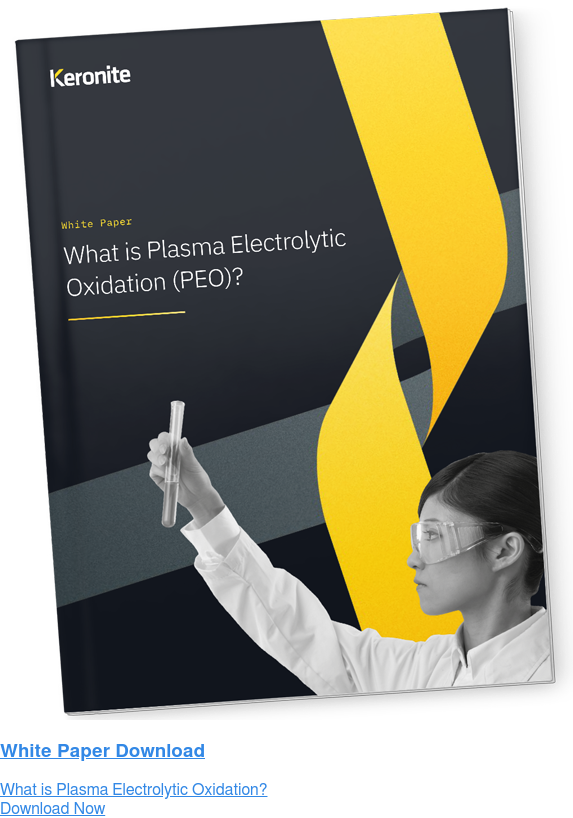
