What impact do light alloy coatings have on the environment?
9 June 2022Light metal alloys are inherently prone to wear and corrosion, yet surface technologies are able to improve their longevity – in even the most testing of applications. Just as pressingly, though, is the string of new environmental regulations impacting the selection of surface technologies.
New regulations in Europe, North America, and specifically within certain industries (including automotive and aerospace) have effectively outlawed some of the most prominent choices of coating technology for new designs. In this article, we will review some of these coatings and assess their environmental cleanliness and impact.
The role of light alloys in electrification, sustainability and component longevity
The overall environmental impact of a vehicle or piece of machinery extends long after its production, with consideration of potential negative effects also required during working life and at end of life.
The aerospace and automotive industries in particular are now taking responsibility for the re-use, recycling and disposal of their vehicles and components. Choosing light alloys that have been coated using processes with the lowest environmental impact thus makes total cost of ownership and end of life material management easier and more cost effective. The specific choice of light alloy coating can also offer a unique source of added value as industries seek to become more environmentally conscious, whilst maximising performance.
For some of the four light alloy coatings considered here, each has a unique set of environmental considerations – in processing, pre-treatment and post-processing. Some coatings can be formed using entirely clean processes, and some can also be coated a second time following use, further extending the life of the component.
Surface coating options assessed: performance vs. processing cleanliness
Chrome plating
DOW-17 was the original anodic process for improving the performance of magnesium components. However, as the process uses chromium (VI), a known carcinogen, DOW-17 coatings are now seen as carrying an unacceptable risk to life and wellbeing. Hexavalent chromium is a substance of very high concern,needing specific authorisation for use since 2017 and banned from use in the EU after September 2024. Furthermore, the plating bath produces toxic waste that requires treatment before disposal.
Plasma spray
Widely used to impart enhanced corrosion resistance and extended life to metal alloys, plasma spray applies a coating a few millimetres thick onto the substrate by injecting powder into a high temperature plasma jet. However, these spray technologies expose workers to respiratory issues as a result of breathing in harmful chemicals. In one study, workplace exposure and release of ultrafine particles during atmospheric plasma spraying in the ceramic industry, it was identified that both ultrafine and nano airborne particles travelled from the emission source inside the spray chamber, out into spaces outside of the chamber. Environmental release of ultrafine particles was also detected outside the exhaust tube, with the release of engineered nanoparticles (ENP) into workplace air.
Anodising
Through the process of anodising, aluminium components undergo a chemical reaction that forms a smooth and hard-wearing anodic surface layer. However, sulphuric acid fumes are released from the bath into the air that with extended exposure are harmful to workers.
Aluminium hydroxide, a by-product of the anodising process, is classified by the United States Environmental Protection Agency (EPA) as a hazardous wastewater and cannot be discharged into municipal wastewater systems.
Plasma Electrolytic Oxidation (PEO)
Developed by Keronite, Plasma Electrolytic Oxidation is a safe and environmentally low impact bath-based method of producing ceramic layers on the surface of light alloys, increasing their:
- Wear resistance
- Corrosion protection
- Thermal management
- Hardness
- Fatigue resistance
- Adhesion
- Lifespan
With PEO, no organic compounds, VOCs, strong acids or heavy metals are required. PEO uses 99% distilled water, and because the electrolytic bath is typically a low concentration, chemically benign, aqueous solution, waste liquids can be discharged directly to municipal drains after a slight pH adjustment.
Giving further environmental credibility to PEO-treated light alloy components, at the end of their life they are also fully recyclable - corrosion protection is imparted by changes to the substrate itself, rather than by adding sprayed-on coatings that may be difficult to recycle.
All things considered, PEO is perhaps the most environmentally friendly method of producing lightweight and long-lived metal alloy components. You can learn more about the environmental credentials of plasma electrolytic oxide (PEO) coatings in our white paper.
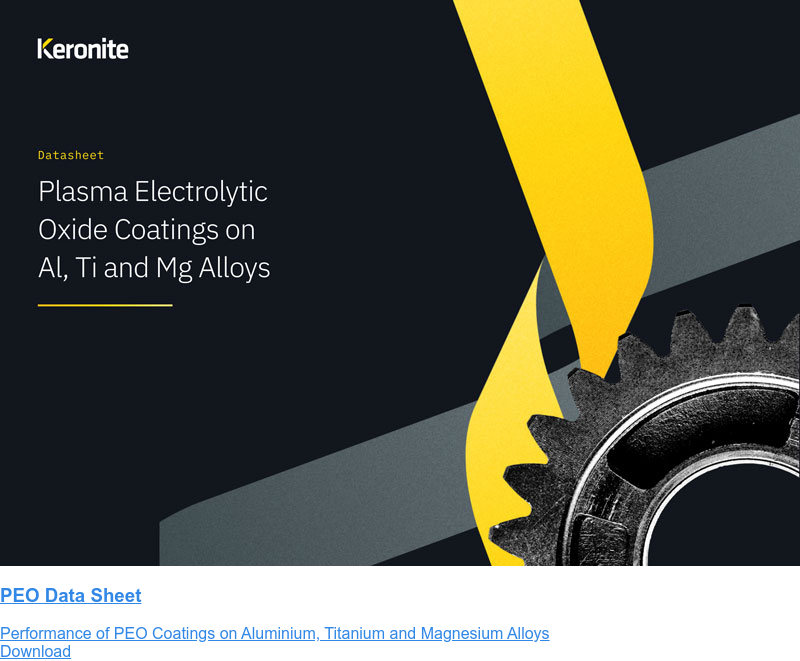
