Trends in automotive materials engineering
4 May 2021The global automotive sector is undergoing an extended period of significant change driven by a wide range of factors. Digitalisation, sustainability and climate change, rapid advances in engineering, science and manufacturing technology, consumer and business behaviours and expectations, transport patterns, health and pollution concerns and the COVID-19 pandemic – all these drivers are generating both opportunities and threats.
According to research by McKinsey, “the top 20 original equipment manufacturers (OEMs) in the global auto sector will see profits decline by approximately $100 billion in 2020”.
That requires massive rethinking on the part of auto-executives, who will be seeking strategies and opportunities to streamline costs and operations at the same time as differentiating their offerings from competitors. Materials choices will underpin the outcomes of these strategic decisions.
Engineering materials strategies available for automotive OEMs
Many OEMs will turn to their existing, and in most cases, well developed lightweighting strategies. Lighter vehicles mean lower emissions, less energy to run vehicles, greater ranges and so on, enabling OEMs to meet the challenges of the twenties. But some lightweight materials offering comparable properties to steel can be nearly four thousand times more expensive, so simply not commercially viable for volume vehicle production.
This means engineers and scientists must further explore how they can incorporate lightweight materials into products and operations, including production technology as well as vehicles, whilst maintaining the balance between safety, cost, value and utility.
Materials strategies chosen by engineers and materials scientists also have a role in meeting health and pollution challenges. Zero emissions does not mean zero pollution and health impacts. Researchers at Kings College London found that the particulates emitted from iron brake pads may be just as harmful as those found in diesel fumes. The UK Government’s Air Quality Expert Group reports that tyre and brake wear account for over 50% of particulates produced by road transport.
Is the automotive demand for lightweight materials growing?
The evidence that engineers and materials scientists are accelerating lightweighting strategies is shown in the growth of the automotive lightweight materials market. Market research firm Markets and Markets highlights that the: “global automotive lightweight material market is projected to grow from USD 69.7 billion in 2020 to USD 99.3 billion by 2025, at a CAGR of 7.3%.”
The lightweight materials covered by the report include metals, composites, plastics and elastomers (polymers). It highlights that these lightweight materials are incorporated into every part of modern vehicles across passenger cars, light commercial vehicles and heavy commercial vehicles. And lightweighting is adopted across combustion engine vehicles, hybrid electric vehicles (HEVs) and electric vehicles (EVs).
So, the impact of the lightweight materials choices made by engineers and materials scientists are far reaching, with the potential to influence how the global automotive sector evolves during the coming decades.
Automotive materials trends – lightweighting is the challenge
Steel of various types remains the most common material used in volume vehicle production, accounting for typically 60% of an average vehicle. Light metals and light metal alloys such as aluminium and magnesium can account for approximately 30%. On average, plastics and composites make up 8%, with around 10% other materials (these percentages do not total 100% as they are indicative). These other materials include rubber, glass, natural and synthetic textiles and leather.
The core lightweight materials types that are found in the automotive sector include:
- Light metals and light metal alloys, such as aluminium, magnesium and titanium
- Composite materials, including carbon fibre, glass fibre, SMC (sheet moulded compound) using a variety of materials, plus many other variations of composites that include metals, glass, resins and polymers
- Plastics and polymers
- Alternative and natural materials, such as bamboo, aerogels and textiles.
The dominance of steel in volume automotive production is forecast to wane from 2025, resulting from multiple factors. Lightweight materials have cost and performance challenges that are limiting their penetration. For example, composites are currently found mainly in high performance vehicles due to their expense. But manufacturing techniques such as pultrusion are reducing the cost of composite components.
Poor wear and corrosion resistance in light metals and light metal alloys historically limited their use in many automotive components and sub-assemblies. However, new alloys and innovative surface coatings, such as plasma electrolytic oxidation (PEO) enable engineers and designers to specify light metal components for a greater range of applications.
The pressure of health, regulatory, environmental, consumer and performance are also outweighing the lower cost and greater utility of steel. Consumers are more accepting of cost increases in exchange for health and environmental benefits, so lightweighting solutions are becoming commercially viable. For example, magnesium is typically 55-60% lighter than steel, yet 150%-250% more expensive. At some point, halving the weight becomes more commercially viable than adding half, or double, the cost.
The long-term future of automotive materials
There is a huge amount of speculation about where the automotive sector will be in 2050 and beyond. Wherever it will be, and whatever consumer will be driving, or perhaps piloting, will require safe, cost effective and good value materials with the appropriate performance characteristics. Those characteristics will include lightweight, as there are so many performance benefits associated with lighter vehicles.
To learn how surface coatings such as PEO enable automotive engineers to exploit the full range of magnesium’s properties in wider applications by preventing corrosion, click below to download the whitepaper.
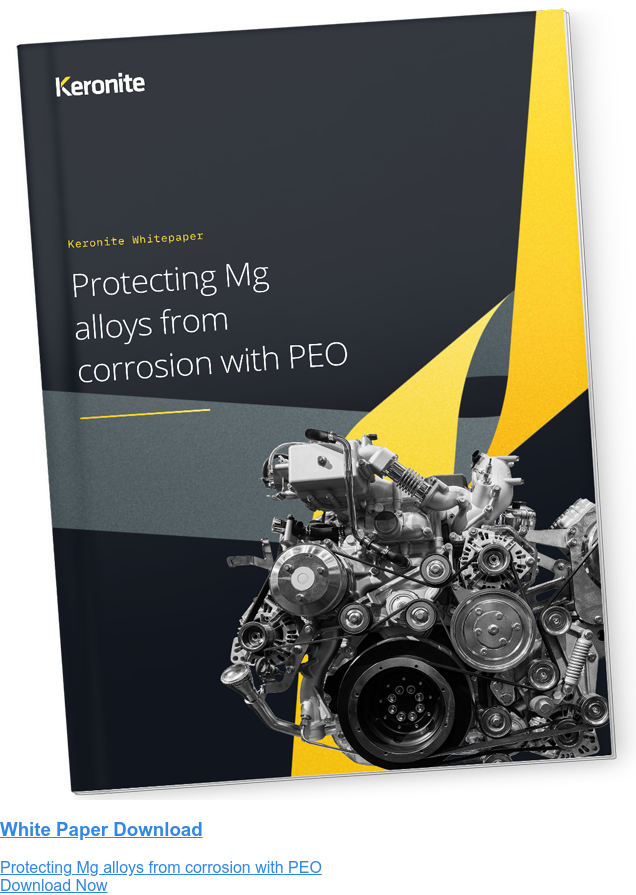
