Thermal properties of aluminium for electric vehicle batteries
8 November 2023The greatest challenge of electric vehicle (EV) design is maximising their driving range. The delivery and capacity of lithium-ion batteries determines this range, which is greatly affected by operating temperature.
Low temperatures slow chemical reactivity and reduces performance, whereas high temperatures also reduce performance and can lead to self-ignition at extreme levels. Because of this, thermal management is a necessary factor in EV battery design, which aluminium can provide through its thermal conductivity.
In this article, we cover the importance of EV battery thermal management and the features of aluminium that make it an effective cooling solution.
The importance of thermal management for electric vehicle batteries
Lithium-ion batteries have become the standard for electric vehicle batteries as a result of their impressive energy density (100-265 wh/kl or 670 wh/L) and delivery (3.6 volts). They also have an extremely low self-discharge rate and lifespan, making them suitable for high-power applications such as EVs. That said, these features are only maximised when lithium-ion batteries are within the optimal temperature range of 15 °C - 35 °C.
At temperatures below the optimal range, the chemical-reaction activity within lithium-ion batteries is slowed. This decreases ionic conductivity in the electrolyte and lithium-ion diffusivity within the electrodes, resulting in decreased performance of approximately 23% between -15 °C and 25 °C.
At high temperatures, there is a loss of lithium and reduction of active materials that results in a lowered energy capacity. Additionally, there is a risk of thermal runaway at very high temperatures that can lead to self-ignition and explosion if not controlled.
Lithium-ion batteries exhibit internal heat generation from high current states and fast charging/discharging rates. Because of this, high temperatures are a key challenge for EV manufacturers.
Aluminium as a material solution for battery cooling
Aluminium is a key metal in automotive and EV design. It exhibits an impressive strength-to-weight ratio, with the 7000 series of alloy exhibiting a tensile strength of upwards of 750 MPa. Because of this, it is used in a range of components to maximise fuel and energy efficiency.
Aluminium showcases the feature of high thermal conductivity (210 W/m-k). Because of this, it is used in a number of heat management applications such as heat sinks that redirect thermal concentrations to dedicated cooling areas. The features of aluminium make it a perfect fit for EV battery thermal management systems. A key example is Nissan ARIYA’s liquid cooling system that runs across aluminium extruded baseplates to ensure sufficient heat dissipation and regulation.
However, alongside the positive features of aluminium, it does have weaknesses that make its integration a challenge. Aluminium is susceptible to corrosion despite its natural oxide layer, which can potentially become an issue with water cooling systems where leaking is a risk. Moreover, aluminium is a soft metal, and can be susceptible to wear and material failure over long periods. This is a particular challenge with the high weights associated with EV battery packs that can cause long term wear.
Advanced coating technology for aluminium-based cooling components
Aluminium’s weaknesses to wear and corrosion are two of the main barriers in the way of its widespread integration in EV battery cooling components. Fortunately, there are advanced coating technologies available to provide resistance to these elements, with Plasma Electrolytic Oxidation (PEO) proving one of the most effective.
The PEO process consists of a customisable electrolyte solution bath where the component is submerged. A high and controlled current is passed through the electrolyte, causing plasma discharges on the component’s substrate. This oxides the outer layer of the component, creating a ceramic outer layer that is resistant to corrosion, wear and many other factors.
For aluminium, PEO is an advanced coating solution that provides corrosion and wear resistance for its effective integration. This makes it the perfect technology for EV battery cooling components, enabling designers to optimise the weight of their designs whilst ensuring effective thermal management and component lifespan.
Ensure the optimal performance of aluminium components with PEO
Aluminium is an innovative material solution to a range of the challenges faced in EV design. Alongside weight optimisation, the cooling features it provides directly aids engineers in maximising the efficiency and energy potential of lithium-ion batteries.
The unique PEO process provides component designers with bespoke surface qualities to incorporate light metals and extend component lifespan. Whether it’s wear, corrosion or other harsh environments, PEO enhances the surface properties for components to operate effectively without risk of failure.
To find out more about PEO, how it can optimise your designs and its ability to extend the lifespan of your aluminium components, contact a member of our team today.
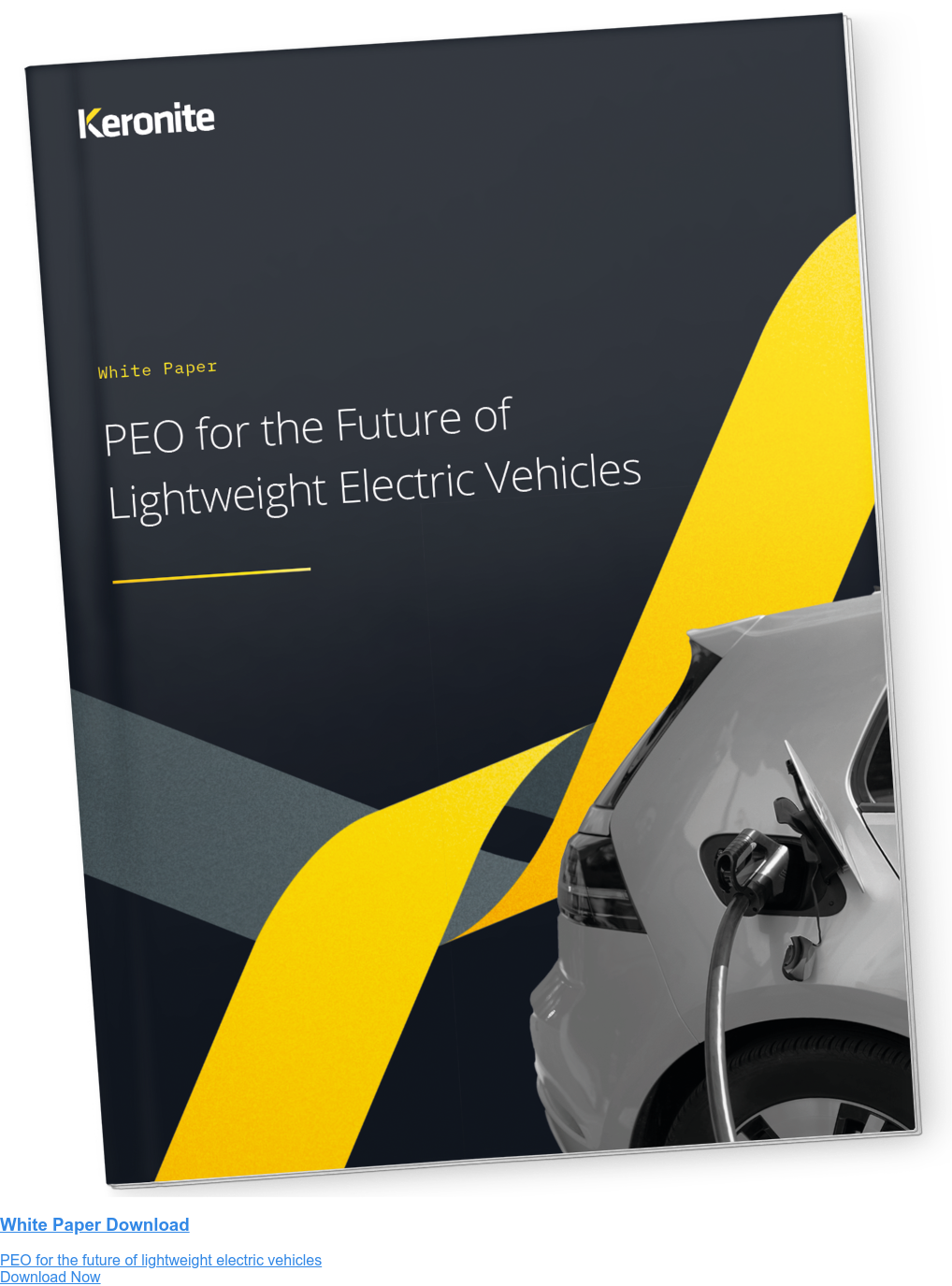
