Thermal barrier coatings (TBCs) for aluminium
8 August 2023Aluminium has been a commonly used metal in aerospace and automotive industries for decades thanks to its lightweight yet strong properties, amongst other useful features. It has almost single-handedly enabled the optimisation of aircraft and vehicle designs to be lighter, more fuel efficient and enhance performance.
For components that face extreme temperatures, such as automotive engine exhausts, the thermal properties of aluminium can limit the range of conditions they can be used in due to the potential for deteriorated mechanical performance. Fortunately, thermal barrier coatings provide thermal insulation for the lightweighting of these components, and Keronite have developed an exciting new surface coating process that utilises amorphous silica to further enhance these characteristics.
Aluminium - lightweight solution for aerospace and automotive
Aluminium (Al) is often described as a light metal that changed the world, being the most widely used non-ferrous metal around the world today. This is mostly due to its range of attractive features that fit component requirements across industries:
- Strength-to-weight ratio - Al is a third of the density of steel at 2.69 g/cc, yet exhibits impressive strength that can be further enhanced through the range of alloys that are commonly used.
- Innate corrosion resistance - Al has a passive outer oxide layer that provides effective corrosion protection, which can be further enhanced via anodising and other surface coating methods.
- High ductility and malleability - The ductility and malleability of Al means it can be machined with ease and allows for a level of component flexibility without damaging tensile strength; perfect for aircraft wings for example.
- Completely recyclable - The metal can be 100% reused via a recycling process that is constantly showcasing innovation to reduce emissions and maximise its sustainable potential.
These features have made Al commonplace in the automotive, aviation and aerospace industries through the 20th and 21st century. Aircraft wings, fuselages, automotive frames and many other structural components consist of Al to reduce the weight of designs. This directly enables engineers to improve fuel efficiency, optimise design elements and enhance the performance of vehicles, aircraft and rockets.
Thermal conductivity and aluminium - both a feature and a challenge
An additional feature of Al is that it has a high thermal conductivity at 210 W/m-K. Depending on the application, this can be seen as either a benefit or a challenge. In the case of the former, Al allows heat for dispersion to transfer heat from and protect vital components, such as heat sink designs for high voltage electronics. In the case of the latter, Al fails to retain structural and mechanical performance when exposed to high temperatures, making it unsuitable for internal combustion and jet engine components.
Al alloys such as the 2000 series reduce the metal’s thermal conductivity to ~80W/m-K. However, this is not enough for engineers to integrate Al into internal components that face extreme and constant exposure to high temperatures.
Thermal barrier coatings - a solution to thermal conductivity and resistance
Thermal barrier coatings (TBCs) are an advanced material coating solution that focuses on thermal insulation. They provide key components with resistant features to the various mechanics of extreme temperatures. TBCs each share the same key characteristics that include:
- A high melting point.
- No phase transformation between room temperature and operating temperature.
- Low thermal conductivity.
- Chemical inertness.
- Similar thermal expansion that matches with the metallic substrate.
- Good adherence to the substrate.
- Low sintering rate for a porous microstructure.
The mechanics of extreme temperatures showcases the requirement for properties that surpass that of simple heat resistance. The coating needs to be able to manage expansion in relation to the metal’s substrate, avoid sintering to maintain porosity and must be chemically inert to avoid unwanted reactions at extreme temperatures.
Plasma Electrolytic Oxidation and high-silica refractory coating
Plasma Electrolytic Oxidation (PEO) is an advanced coating technology that provides light metals with extreme thermal resistance, as well as a range of other bespoke surface features. It utilises an electrolyte bath that, when submerged, creates plasma discharges on a metal’s surface once a controlled voltage is introduced. This creates a highly consistent and resistant outer ceramic coating that is porous and can absorb reagents that are introduced into the electrolyte solution.
Keronite, the creators of the PEO process, have developed an electrolyte solution that contains amorphous mixed oxides of silica; a resilient element that not only provides thermal protection, but is also wear and corrosion resistant. By incorporating a higher concentration of silica in the electrolyte formulation, Al components exhibit enhanced thermal insulation properties, reduced thermal conductivity, and a bright white finish.
The coating's thermally insulative nature, along with the presence of a crystalline alumina phase, makes it ideal for applications requiring exceptional thermal management, such as jet engines, power generation systems, and automotive exhaust components. By providing an effective thermal barrier, this advanced coating facilitates the operation of components in extreme temperature environments, contributing to increased operational efficiency, reliability, and prolonged service life. They are also used to improve engine efficiency and to prevent any thermal issues affecting structural components that need to be lightweight.
To find out more about the details surrounding high-silica TBC and our other electrolyte solutions, download our datasheet. Or, to find out more about how PEO can provide the surface characteristics you need for your application, contact us today.
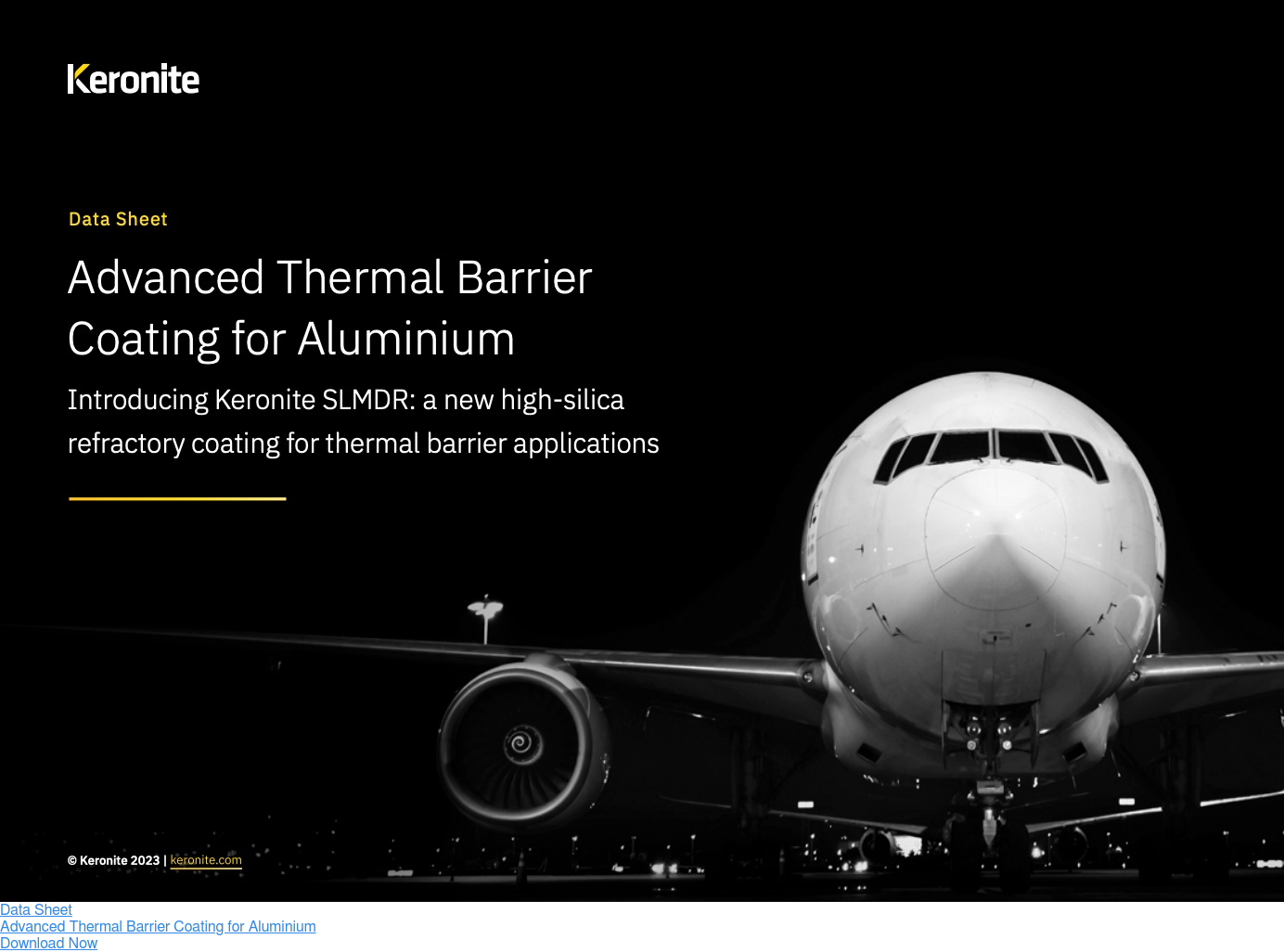
