The next industrial revolution: how will the digital and physical worlds collide?
13 December 2019Data has already had a tremendous impact on the global economy. To detract even more value from this data, manufacturers are transforming this data using sophisticated algorithms, and enacting change through robotics and artificial intelligence in the real world.
Data determines how much your insurance premiums cost. It helps aerospace manufacturers identify potential weaknesses in a design. And it's even feeding the algorithms that are training cars to drive themselves. There's even healthcare benefits, with machine learning algorithms leading efforts to find effective cancer treatments.
Manufacturers are already finding value in this data. It's helping find better ways to improve quality, efficiently manage resources, and even predictively anticipate when parts could fail. Yet over the next 100 years, we'll be seeing that data proliferate into physical form. Robots, self-driving cars and drones, automated machinery and electronics will all become more valuable thanks to machine intelligence.
Merging the digital and physical worlds
The digital worlds that we access through our phone and laptop screens and the physical worlds are no longer distinct.
Sensors are ubiquitous in factories and warehouses. They are becoming cheaper and capable of monitoring more types of activity. Self-driving cars are being powered by object-detecting cameras, goods moving can be tracked by RFID tags and sensors, while chemical sensors are helping keep industrial environments safe. Many of these sensors are being embedded within existing equipment, meaning they integrate seamlessly within existing equipment.
With new technologies, deriving value from these insights will become even easier. Instead of relying on vast amounts of labour, Ericsson describes a world where sensors collect ‘lakes’ of data. Algorithms could be crafted that enable robots to act upon this data, too.
Integrating digital innovation in the physical world
The 1980s marked the beginning of the third industrial revolution: the digital revolution. Little did we know that the data captured on computers and other digital devices would prove valuable in this very day. Data is now the lifeblood of modern robotics and data science. Companies that have the largest historical records, ‘datasets’, stand to benefit the most from new ways of manipulating data.
However, to fully exploit this opportunity, companies are seeking ways to develop robots and equipment that utilises this data:
The automotive opportunity
One of the most widely cited examples of machine learning and artificial intelligence is the self-driving car.
Cars kitted out with sensors are racking up millions of road miles, all in order to collect data on the road and the behaviour of fellow drivers. This information is ‘training’ the software that’ll control self-driving cars in the future, so it’s always improving.
The entire business model of vehicle ownership may disappear. Volkswagen has launched a new service called WeShare in Berlin. The initiative allows drivers to rent Volkswagen’s electric cars by the minute. VW has a fleet of 1,500 e-Golf’s available to rent now, with plans to increase the size of the fleet size by 75% by the end of 2020. At the moment, VW employs a service team to ensure vehicles are charged – the company hopes soon to incentivise drivers to plug in the vehicles themselves, but that hasn’t changed the business model now.
There are likely to be wide-reaching consequences for the supply chain, too. Efficiency and manufacturing speeds are likely to increase, too. Additive manufacturing (AM) may be employed by designers prototyping new vehicles, helping speed up the time to market. Also, advances in materials science will help these parts last longer and perform better – creating more opportunities to add value and improve profitability of new market opportunities.
Industry 4.0 takes to flight
Data and analytics is already helping to create aerospace designs that deliver greater value for customers. Intelligent design decisions are informed by information and analytics in regards to additive manufacturing, smart factories, industrial sensors and an increasing amount of robotics and automation in manufacturing.
The aerospace industry is likely to see major advances in the following areas:
- Vertical integrations
- Smart factories
- Industrial IoT
- Analytics for servicing
- Predictive fault detection and repair
SMART manufacturing
Robotics could revolutionise manufacturing. Integrating more sensors is helping manufacturing equipment become more connected and reactive. This could be supported by:
- Additive manufacturing
- The connected factory
- ‘Advanced’ manufacturing
Keronite is working to enhance the longevity of smart manufacturing equipment, including machinery, installation products and additive manufacturing equipment.
Advanced medicine in the the era of artificial intelligence
- Personalised healthcare. Wearables and medical equipment that capture medical data can help doctors recommend personalised treatments.
- Implantable technologies. Advancements in implantable technologies are making implants adhere more strongly to cells.
- Using advanced robotics to improve the quality of treatments and care.
Surfaces for the future
Keronite make uniquely performing surface technologies for light alloys. Light materials are integral to bringing the digital world into the physical. They help make lightweight, efficient and long-lasting products that create value within these new applications. With Keronite’s plasma electrolytic oxidation technology, these light alloys are able to replace heavier metals; making machinery more efficient. The coatings help these materials perform in intense operating conditions, too.
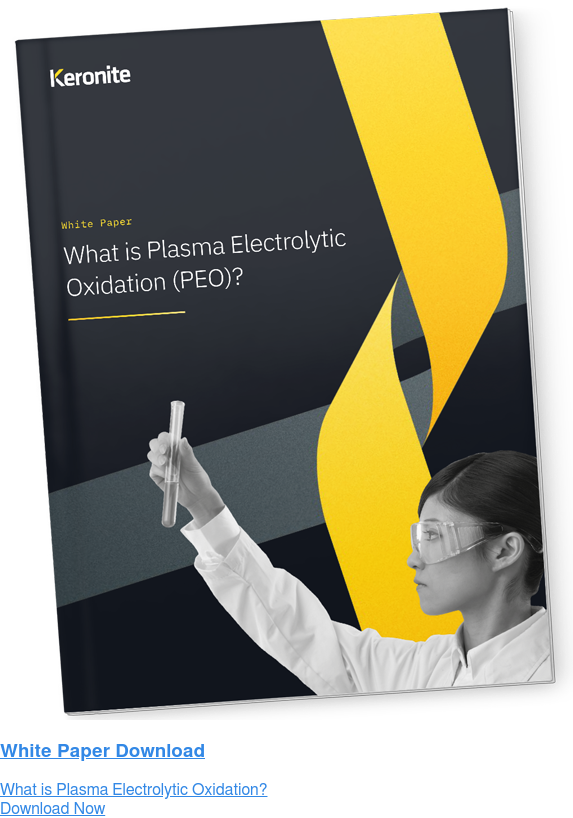
