The future of PEO and materials science research
22 June 2022It is over 140 years since plasma electrolytic discharge phenomena were first observed by Sluginov in 1880 (Sluginov, N.P. On luminous phenomen, observed in liquids during electrolysis. J. Russ. Phys. Chem. Soc. 1880, 12, 193–203.) In the intervening years scientists have developed and refined the technique of plasma electrolytic oxidation (PEO) - a bath-based method of producing ceramic layers on the surface of light alloys. Research and development have already greatly expanded the available range of treatable substrates, with more specific composition and morphology of ceramic layers now possible.
PEO surface coatings are characterised by their hardness (2-4 times that of hard anodising or steel), as well as their resistance to wear and corrosion, and thermal and chemical stability. These properties have made the process a viable option for weight reduction and life extension of metal components. Yet with advances in modern technology and greater customer expectations come new applications and more challenging specifications. Keronite’s material scientists continue to work on innovative and exciting research projects to further improve the scope and scale of future uses for PEO.
Notable advances in PEO technology
Even the most innovative processes can be further improved, and the research community continues to work on developing enhanced solutions to meet the engineering challenges of the future. Augmented PEO performance is already being delivered through ongoing research projects exploring:
Duplex coatings
With the use of duplex coatings, bespoke finishes can be produced by adding sealers such as epoxies, polyurethane coatings, fluorocarbon and silicon-based sealers and sol-gel. Through this advanced PEO process, optimum properties of both base coating and sealer are combined to give a superior overall performance standard. Research is highlighting where different sealers convey specific properties, such as lubricity and thermal conductivity, dependent on the application.
Anti-viral surface coatings
Keronite is currently working on research to develop surface coatings that will actively destroy airborne pathogens. SARS-CoV-2, the virus that causes Covid-19, can be destroyed by antiviral surface coatings exhibiting photocatalytic properties. The PEO process creates highly porous surfaces and their porous characteristics, when combined with TiO2, act as a potent photocatalyst. Research has shown that these coatings aid in the destruction of airborne pathogens, including SARS-CoV-2 - a potentially life-saving discovery.
Brush-on surface coatings
Currently, PEO coatings are applied in a specialist tank to ensure consistent coverage and full transference of resistive qualities. Keronite’s material scientists are working on developing brush-on PEO, to enable far more straightforward coating of small-area components. This would be especially useful for coating new or replacement parts in industries like aviation, saving energy and, crucially, reducing time on the ground.
Particle incorporation
Working with Cambridge University, Keronite’s R&D team are looking at ways to further improve both chemical and mechanical properties of PEO coatings. Incorporating fine particles into the electrolyte solution makes the resultant surface more resistant to corrosion and wear. The technique has the added advantage of making the process more energy efficient too, as less of the coating’s protection is produced by substrate oxidation.
Robotic adaption
Degradation due to excessive wear, as well as exposure to variable conditions such as high temperatures, acidic manufacturing environments and hydrostatic pressure, are key challenges for machine automation. Keronite is working on next-generation surface treatment technologies to give moving components improved resistance to wear, corrosion, heat and other extreme conditions such as high loads and repetitive stresses.
Parameter interdependence
As a multi-stage process, a range of parameters influence the properties produced by PEO: substrate and electrolyte composition, electrical power supply, operational pressures and temperatures. Modifying each of these parameters, and optimising the relationship between them, influences the physical properties of the resultant coating. Research is ongoing to understand how adaptations to process parameters can produce coatings with improved microstructure, pore size, roughness, colour, texture, hardness and adhesion. The implications for this research are potentially significant, as it may render PEO more suitable for use on ferrous materials in future.
A bright future for plasma electrolytic oxidation
Increasing reliance on green energy, artificial intelligence, machine learning and micro-technologies continue to bring new opportunities for producers and exert new challenges for engineers. Ongoing research will be vital in developing new solutions as well as tailoring existing ones to fit the specific needs of individual projects. The PEO process will thus continue to evolve, thanks to ongoing research to refine performance and open up potential for use in new applications and with different materials.
As we continue to refine the plasma electrolytic oxidation process to meet the future requirements of our customers, you can find out more about the fundamentals of PEO in our white paper.
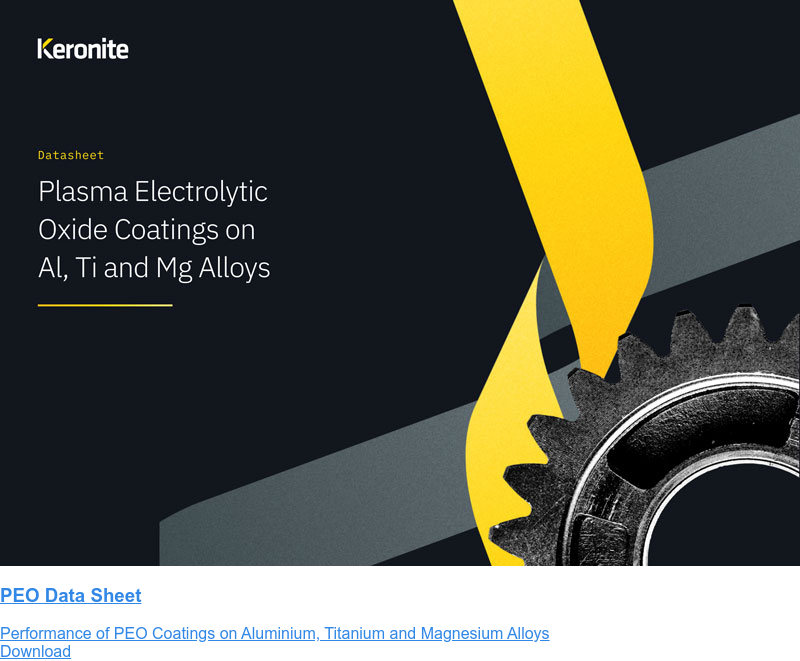
