Surface technologies to prevent aluminium brake fading
27 September 2021Successful braking is key to vehicle safety. High-performance sports cars through to heavy freight trucks all rely on a system of brake pads and rotors to control their speed. Brake fade is a reduction (or complete failure) of stopping power in a vehicle’s braking system. It usually occurs when brake pads become overheated. Automotive designers, materials scientists and engineers are working together to improve brake performance and reduce the risks associated with brake fade.
What causes brake fade?
Brake fade is not a mechanical fault. It’s a temporary loss of function in the braking system. This is characterised by a firm brake pedal but ineffective braking. The driver meets resistance when pushing the brake pedal, but little to no deceleration happens.
A typical disc braking system is made up of a spinning cast-iron disc which rotates with the wheel. When the driver pushes the brake pedal, pressurised fluid runs through a series of lines to the brake callipers, which push a brake pad against the rotating disc. This creates high levels of friction which slows the car down. It also creates a significant amount of heat.
Brake pads are generally made from a combination of phenolic resins and filler materials that are designed to dissipate heat through the pad. The formulation of these brake pads is key to their performance, and they’re designed with a specific end use in mind. A typical passenger vehicle will use organic-ceramic brake pads which can withstand temperatures of up to 250 °C. Whereas a high-performance race car would use semi-metallic sintered brake pads which work best between 450 – 700 °C.
Brake fade occurs when the temperature of the brake pads exceeds the tolerance levels that they’re designed for. Under heavy or sustained braking conditions the brake pad becomes overheated, and the organic resin degrades to produce a variety of gases. This thin layer of gas acts as a lubricant between the brake pad and disc. The pad and disc are no longer in full contact with each other so there’s reduced friction, and limited deceleration. Overheating can also cause a permanent change in the chemical composition of the brake pad, reducing braking performance and requiring a replacement pad.
Drum brakes work using similar principles to disc brakes, but all the components are housed inside a drum. This type of braking system is still used in older vehicles, or for rear wheels in newer models. Braking is less effective compared to disc brakes but sufficient for rear wheel braking. The components are cheaper to manufacture compared to disc brakes, but the heat is trapped inside the drum, making them more susceptible to brake fade.
An additional cause of brake fade comes from the brake fluid. Hydraulic brake fluid is designed to have a consistent viscosity and a high boiling point so that it cannot be compressed in the brake lines. However, if the fluid does boil due to prolonged or heavy braking, this will cause fluid fade and reduce braking power.
How can we improve brake performance?
Improved braking power comes from an increased friction coefficient between the brake pads and the disc. However, more friction generates more heat in the brake system.
Automotive engineers employ several techniques to minimise heat build-up in the braking system and maximise braking power. Using vented brakes to allow airflow through the centre of the brake shows significantly improved cooling compared to a solid cast-iron brake disc. We can also look to the overall design of the vehicle to direct airflow to the brakes to reduce the temperature and avoid brake fade.
Using brake pads that are specifically designed for a given application is critical to avoiding brake fade. The material used in the brake pads must be correctly designed for the end use of the vehicle. For example, a city-run-around designed for low temperature braking will have brake pads with a very different composition to a high-performance race car. There are also manufacturing costs to consider; with organic-ceramic brake pads being much cheaper to produce on a large scale than semi-metallic or ceramic pads.
As an innovative approach, we can look to surface coatings to improve braking performance. PEO coatings for vented aluminium brake discs could provide a solution to each of these three areas: maximising friction coefficients, reducing heat build-up and no significant increase in cost of raw materials.
Using PEO coatings, materials scientists can tailor the chemical composition of the metal’s surface to achieve the desired properties. Early studies show that PEO-coated aluminium has the potential to replace cast-iron brake discs. Laboratory-based testing has shown that a high friction coefficient can be achieved with a 50 – 60 μm PEO coating. These coatings also demonstrated excellent wear resistance under high thermo-mechanical load.
Aluminium alloys have high thermal conductivity, so can dissipate heat away from the brake pads quickly. The peak temperatures seen using aluminium brake discs were lower than the equivalent cast-iron samples tested, reducing the risk of brake fade. Aluminium has the added advantage of being lightweight, leading to reduced emissions, lower running costs and the potential for improved acceleration
Keronite have been working with leading brake disc manufacturer Alcon to develop PEO coatings for aluminium brake discs which have the potential to improve braking performance, reduce heat build-up and minimise non-exhaust particulate emissions. Find out more about the research project in our white paper here.
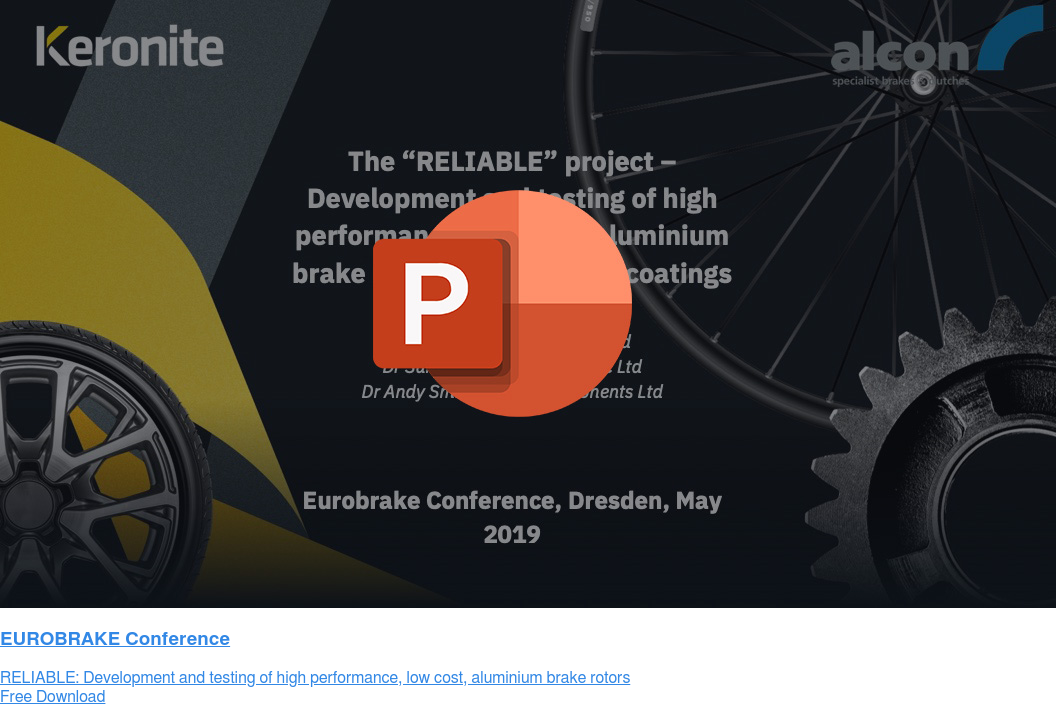
