Surface coatings for localised corrosion resistance
27 January 2021Weight reduction, driven by performance, cost and sustainability pressures, is of increasing importance to design engineers and materials scientists. With weight savings of up to 50% over steel and 30% over aluminium, magnesium and its alloys are becoming an increasingly popular choice in a range of applications.
However, alongside its attractive strength-to-weight ratio and other properties such as low stiffness and high heat conductivity, magnesium has some intrinsic weaknesses naturally. Without an appropriate coating, it can easily corrode and its low hardness results in poor wear resistance.
Specific metallurgical factors and corrosion mechanisms means magnesium alloys are particularly susceptible to a form of corrosion called pitting. Conventional surface treatments used for corrosion protections exacerbate this weakness because of highly localised weaknesses in their coverage. This weakness can limit the applications where magnesium and its alloys can be used.
However, surface treatment technologies such as plasma electrolytic oxidation (PEO) protect magnesium from corrosion without pinholes, wear and can even add other features such as lubricants and antibacterial coatings.
What is pitting corrosion?
Pitting corrosion is distinguished from general uniform corrosion because the damage to the material is in the form of cavities, or ‘pits’, and is localised. Because it is localised and the cavities start at the microscopic scale, it is harder to detect and therefore can be higher risk than other forms of corrosion.
The formation of the cavities by pitting corrosion can lead to failure as a result of mechanisms such as stress corrosion cracking. In this failure mechanism, undetected cracks propagate from the cavity along grain boundaries that lead to catastrophic failure. This is a frequent occurrence for substrates coated with surface coatings that are prone to cracking.
Magnesium suffers from all the main forms of corrosion: uniform corrosion, galvanic corrosion, pitting corrosion and filiform corrosion. The latter two mechanisms are the most common in magnesium and magnesium alloys and typically occur simultaneously.
Understanding corrosion mechanisms
Light metals such as aluminium and magnesium are sufficiently chemically active that they form oxide films on their surface in the presence of air that provide limited protection against wear and corrosion. In the case of magnesium alloys, this film is not complete and uniform – there are gaps. Microstructural inconsistencies, fine and coarse grains, are formed during the alloying process, which in turn results in inconsistent oxidation of the outer layer.
Magnesium alloys, such as the commonly used AM60B cast alloy, are also disproportionately affected by low and neutral pH levels. In the case of AM60B, this is believed to be the result of local micro galvanic corrosion arising because of the voltage differential between the alpha magnesium (α-Mg) crystalline structure surrounding the aluminium-manganese (AlMn) phase.
In an acidic or neutral solution, such as aqueous sodium chloride (NaCl), the magnesium reacts with water, so the resulting corrosion pit is filled with magnesium and hydroxide ions. These precipitate at the surface of the pit as magnesium hydroxide, emitting hydrogen gas. This anodic-cathodic reaction deepens the corrosion pit that, if unchecked, can lead to accelerating pitting corrosion and eventual failure.
Using ceramic-like conversion coatings to protect magnesium from pitting corrosion
Surface coatings are widely used to protect magnesium from corrosion and wear. But defects in common surface coatings, such as paints, powder coating, thermal and plasma-spray coatings, electroless nickel plating, hard anodizing and nitriding, can generate pinholes.
These defects can be caused by surface imperfections because the alloy has not been pre-treated correctly when powder-coating or electroless nickel-plating, through inconsistent coverage by spray-type coatings, or from coating defects, such as cracks found in hard anodising. The microscopic to visible holes, cracks (see figure 1) or inconsistent coverage, in the surface coating leads to pitting corrosion.
In contrast, the highly conformal and duplex PEO coatings, shown in figure 1, provides consistent coverage with no scope for pinhole formation and pitting corrosion.
Figure 1 Left: Cracks in hard anodised coatings that lead to pitting corrosion. Right: Consistent conformal PEO coating.
PEO’s approach uses an electrolyte bath and plasma over three distinct stages to form a ceramic-like duplex coating on magnesium alloys. Each stage can be finely adjusted to create bespoke coatings according to the end-application. As shown in figure1, the oxide base layer is part of the substrate, it is not a coating or plating, so pinholes cannot form. The multi-layered coating’s top layer is also highly porous. This enables the coating’s top layer to incorporate additional substances added to the electrolytic bath that provide additional properties. For example, using a silicate-rich electrolyte results in a mullite-rich outer layer that is highly wear resistant.
PEO’s fine microstructure and surface texture create an ideal physical ‘key’ for top coats – resulting in much stronger adhesion of the top coat than other surface coating technologies, such as hard anodising. This duplex system combines the improved corrosion protection of both elements synergistically to provide unparalleled corrosion protection. As a result, materials scientists and engineers can specify magnesium alloys for use in corrosive and harsh environments.
To learn how surface coatings such as PEO enable engineers and materials scientists to exploit the full range of magnesium’s properties in wider applications by preventing pitting corrosion, click below to download the whitepaper.
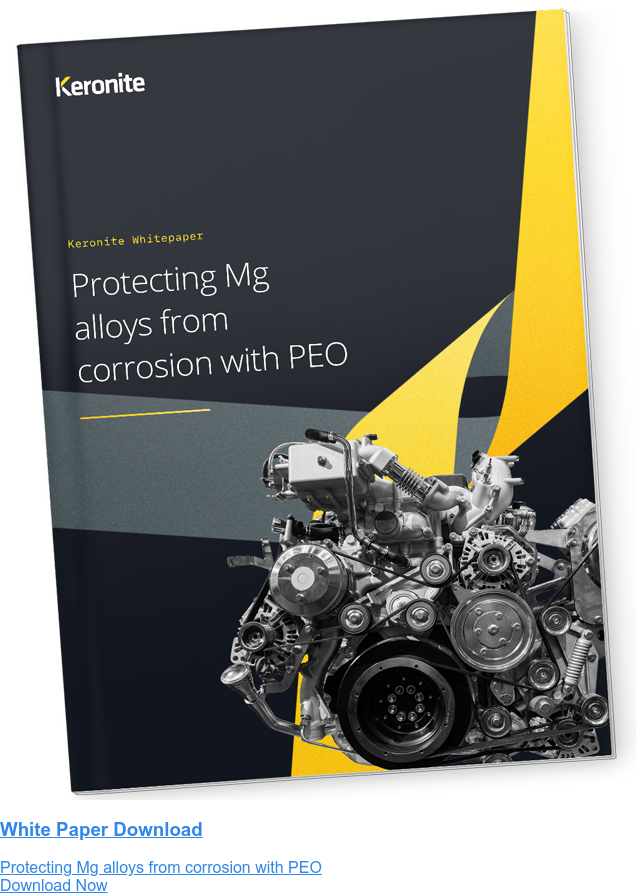
