Trends in sub-sea defence technology
6 July 2021Subsea defence technology is becoming more and more sophisticated. Over the last 50 years we have seen significant improvements in subsea communication and defence strategies. The widespread use of sonar tracking technology is now complemented by laser-tracking (LIDAR), infra-red detection, and satellite GPS. This has expanded tracking and monitoring capabilities in the subsea environment.
The key to keeping subsea vessels safe is to avoid detection by enemy forces. Improving stealth can be achieved through various methods, but since sonar is the main technology used for detection, many military development programmes focus on reducing the acoustic output of subsea vessels. Advances in coatings technologies also have great potential for layers to be developed with anechoic capabilities.
Improving Sonar Stealth
Sonar works by monitoring sound waves as they travel through water. Passive sonar is most commonly used to detect submarines and other subsea vessels as it emits no signals itself. Military experts around the world are essentially “listening” for submarines, using highly sophisticated equipment and advanced computational techniques to eliminate background noise.
Stealth techniques to avoid sonar detection have advantages across the defence sector. In addition to submarines, these methods have applications in surface warships and other submersibles. The military uses a variety of unmanned underwater vessels (UUVs) to detect mines and other submarines. These could also benefit from being undetected by the sonar capabilities of an opposing military presence.
Reducing the sound output from submarines can be achieved in two main ways; reducing the amount of radiated noise from the vessel’s onboard machinery, and reducing the external noise generated as the vessel moves through the water.
Radiated noise from a submarine’s engine and internal machinery can be reduced by using efficient machinery, such as diesel-electric engines. These are quieter than conventional nuclear submarines as they convert the energy generated from the diesel engine to electricity. It is then an electric motor that directly fuels propulsion through the water, which is much quieter. Noise dampening materials (often rubber) can be used to mount machinery and limit vibration.
A double hull design can be used to create a sound-proofing layer around the pressure cabin of a submarine. It also provides an opportunity to modify the shape of the hull to improve hydrodynamics and reduce external flow noise.
The hull can be soundproofed even further by adding anechoic tiles. These have been used in military submarines since the Second World War. The tiles are made up of several layers and contain different sized voids to target specific sonar frequency ranges. They are effective and are still used today. However, they do have limitations, particularly surrounding application, maintenance, and adhesion to the outer hull.
Looking to the future
Military applications are often the driving force for advances in technology. The marine environment poses a variety of engineering challenges; from improving energy efficiency of engines to developing corrosion resistant materials. Submersibles present an additional requirement of being able to withstand extreme pressures under water.
Materials scientists can look to lightweight metals such as aluminium, magnesium and titanium to improve a submarine’s efficiency. Other lightweight materials such as fibre-reinforced polymers (FRP) can be used for certain areas. Reducing the weight of the vessel will allow the submarine to remain submerged for longer and increase the distance that it can cover before surfacing to refuel. It also allows more weight to be allocated to weapon capacity.
With this in mind, the use of titanium alloys for subsea hulls has become increasingly popular, particularly with Soviet submarines. The high strength-to-weight ratio of titanium means that the submarines can operate at increased depth. Titanium has the added advantage of being able to avoid detection by magnetic anomaly detection (MAD).
Engineers can also use advances in coatings technologies to avoid submarine detection by enemy forces. There is potential to experiment with superhydrophobic coatings for the outer hull; both for anti-fouling and hydrodynamic properties. Similarly, an extremely smooth surface (surface roughness of the order of 10 microns) would have advantages in terms of drag and reducing external flow noise.
PEO coatings can be modified to tailor the surface properties of a component. The outer surface of the coating is porous, allowing specific compounds to be impregnated to alter the surface chemistry. Recent studies have shown the potential of multi-layered and shaped anechoic coatings. PEO also gives excellent adhesion properties for a duplex coating system, where a subsequent polymer coating is added. This has potential to be used for sonar stealth and other defence applications that require sound absorption or similarly specific coatings.
To find out more about PEO coatings, including how they are applied and how their properties could be modified for use in the subsea defence sector, download our “What is Plasma Electrolytic Oxidation?” white paper below.
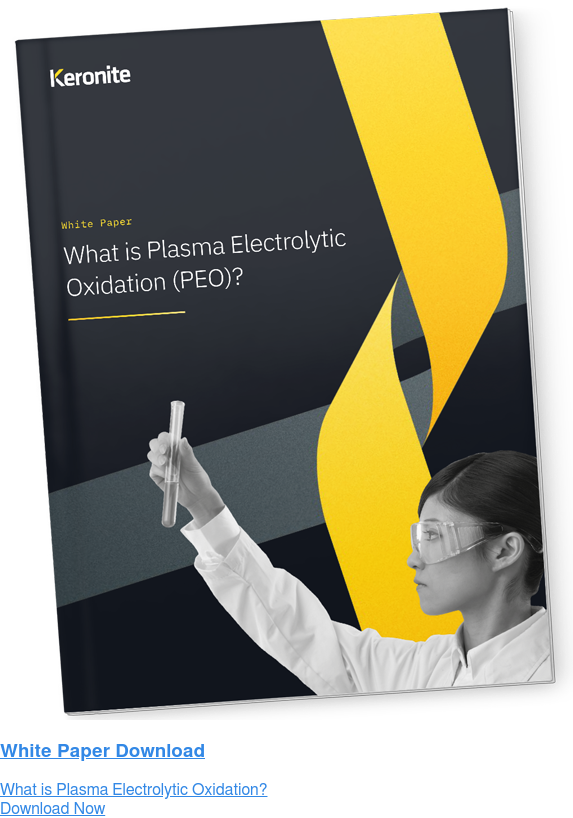
