Smallsats: The future of satellite design?
14 January 2020Innovation in the space manufacturing industry has taken a different trajectory lately. Rather than focusing on high-risk innovation for one-off projects, a new, frugal approach has become more favoured.
Manufacturers are seeking to reduce the cost of satellite launches and general space exploration. SpaceX are pioneering reusable rockets, as are Blue Origin and others. But it’s satellites where major strides are being made.
By 2025, there will be 1,100 satellite launches per year, predict MIT. Launching new satellite constellations will enable new communications possibilities, more detailed Earth imaging applications and contribute to our understanding of the universe.
The case for smaller satellites
Satellites are critical in communications and navigational systems. They’re big, bulky, and surprisingly expensive to launch. For every kilogram they weigh, it costs as much as £50,000 to launch them. Thanks to a number of innovations, smaller satellites are still capable of delivering the same benefits to customers.
By definition, a microsatellite weighs less and is much smaller than a typical satellite. Based on where you are in the world, the criteria for a microsatellite may vary. Generally, speaking they can weigh as little as 10 kg.
Smaller satellites are allowing for a wider diversity of applications. As technology becomes miniature and materials like light alloys are enabling the design of super-lightweight satellites.
Microsatellites come with a wide range of commercial benefits, as well as advantages enjoyed due to their form. Space manufacturers seeking economies of scale are looking towards microsatellites. By mass producing smaller satellites, they are able to reduce the price of space missions; thereby encouraging more space agencies to take the leap.
Microsatellites and surrounding technologies are enabling more nations to undertake space missions. For example, Switzerland, Estonia and Slovakia have all launched their first satellites since 2009 – each of them were microsatellites, weighing mere kilograms.
Microsatellite applications
- Earth imaging.
- Software-defined radio. (ref)
- Low-Earth Orbit telecoms and data communications. (ref)
- Radiation monitoring. (ref)
Offering satellites new life
Microsatellites pack in a host of components into a tiny form factor. As electronics become more miniature, compact, and lightweight, microsatellites can house far more equipment than ever before – without adding an excessive payload.
Increasing life in aggressive environments
Satellites will typically include sophisticated communications and control systems, on-board computation components and propulsion systems. Every added feature adds more weight, which can be costly. Cameras, instruments, sensors and high-end compasses are all likely to feature.
But the introduction of sophisticated equipment begs the question: how can microsatellites become as light as possible, all while lasting longer in orbit?
Effortlessly lightweight
Space offers an incredibly aggressive environment for light alloys. Light alloys have risen to prominence in microsatellites. Given their lightness and high strength-to-weight ratio, they are replacing heavier metals and even plastic composites. Replacing the former allows satellites to become cheaper to launch and carry increased payloads. Whereas in plastic composites, they cannot guarantee performance in particularly aggressive environments.Satellites need to be built to for:
- Thermal performance.
- Optical reflectivity.
- Debris formation.
- Vibrations.
- Atmospheric humidity.
But light alloys alone won’t provide all of the qualities necessary to perform in these aggressive environments. Choosing materials and advanced surface technologies is crucial in modern space design. The aggressive, diverse environment necessitates surface coatings to uniquely improve the characteristics for parts, all of which are likely to come under unique materials challenges.
Aluminium alloys are commonly used in microsatellites, helping to reduce weight and increase life. But their performance is almost wholly dependent on the alloy selected and the right surface coating.
Surface coatings for light alloys on microsatellites
Microsatellites present a unique set of challenges for light alloys in space. With multiple conflicting properties, there are few surface coatings that offer comprehensive performance in space.
Materials scientists at Keronite are leading the line when it comes to coatings for space. Keronite has refined the technique for producing hard ceramic coatings by plasma electrolytic oxidation. Their materials scientists are deploying the world’s most advanced coatings for microsatellites, in the form of Keronite Ultra-Black and Keronite Ultra-White.
Plasma electrolytic oxidation has caught the eye of space manufacturers due to the versatility of the coating. The coating methodology can be adjusted to deliver coatings with select characteristics. By modifying the composition of the electrolyte, electrical regime, application time and a host of other factors, Keronite’s materials scientists have been able to create coatings that uniquely improve the performance of light alloys in space.
What’s next for PEO?
Keronite’s ties to research organisations and innovation partners have enabled them to lead the way on research and development on coatings in space.
Research conducted with the European Space Agency (ESA) led to the creation of Keronite Ultra-white, a coating that was later used in the Bepicolombo mission to Mercury. The goal of the project was to create an ultra-white coating that would provide all of the necessary qualities to enable the microsatellite to remain in orbit for the entirety of the 15 year length of the project.
Keronite’s scientists are inviting enquiries from microsatellite manufacturers right now. If your project involves a particular materials challenge that other coating solutions cannot provide sufficient performance, get in touch with Keronite today.
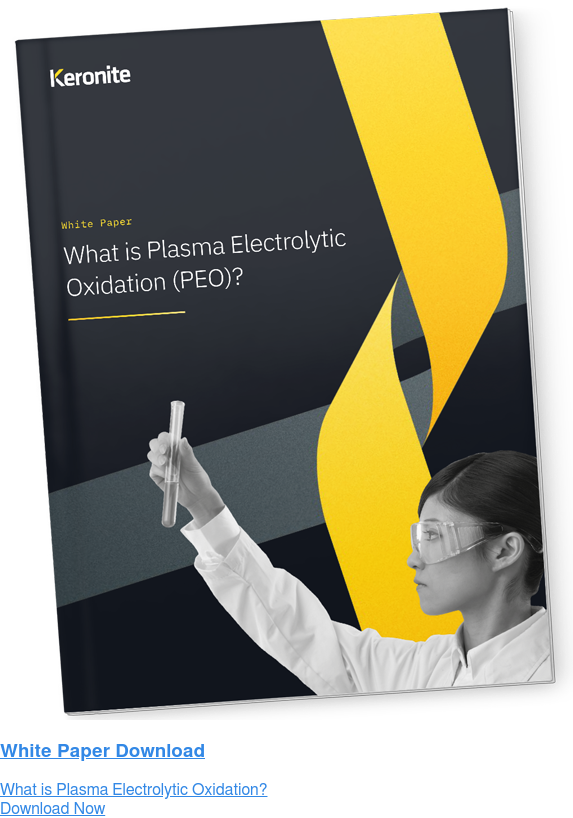
