Semiconductor fabrication technology that could resolve the supply chain crisis
25 April 2023In the past 3 years, the semiconductor industry has faced an unprecedented multitude of pressures. A supply shortage, coupled with an unexpected demand surge for electronics, in consumer technology, automotive, robotics and countless other industries, put foundries on the backfoot to reduce their lead times.
In response, a spate of new technologies and research projects, pioneered by scientists, are coming to market to resolve the issues once and for all. One of these breakthroughs is in materials technologies, which could revolutionise how semiconductor machinery performs. Specifically, new technologies are enabling light alloys to perform in harsher, faster, high-throughput semiconductor manufacturing environments – allowing foundries to quickly increase efficient, high-quality, high-volume manufacturing with minimal friction.
The supply chain complications of semiconductor production
Semiconductor fabrication is a complex engineering process that depends upon a volatile supply chain. It demands a range of rare earth resources, as well as cutting-edge technology in foundries that costs multiple billions to create. The capital, resources and expertise needed to produce semiconductors has resulted in R&D specialisation in different geographic locations. The side effect of this, however, is a global ripple effect when one part of the chain fails.
There are multiple factors that have led to semiconductor shortages. The global pandemic has had a long-lasting impact on the market; major outbreaks at rare mineral mines produced shortages, whilst global lockdowns increased the demand for electronics at home.
Major semiconductor manufacturers have also faced internal as well as external complications that affected the entire supply chain. Renesas, a Japan based premier supplier of semiconductors globally, experienced a fire at one of their fabrication plants early in 2021. Renesas is a major supplier of the automotive industry, one that has dramatically reduced production from the supply chain crisis and experienced billions of losses as a result. Additionally, the situation in Ukraine has resulted in a global shortage of vital resources used for semiconductor manufacturing; Ukraine supplies 25-35% of global purified neon gas, and Russia supplies 25-30% of global palladium.
The need for efficiency in semiconductor manufacturing
In light of the supply chain issues faced by the semiconductor industry, the optimisation and efficiency of existing production has become a major concern for manufacturers. Increasing yield quantity and minimising production downtime are vital in achieving these goals. The resilience and lifespan of manufacturing equipment is a pivotal part of production efficiency, which face extreme conditions throughout the process.
The process of creating semiconductors includes a range of extreme and strenuous elements. The initial creation of high-purity silicon wafers involves a range of gaseous and corrosive chemicals that are highly reactive to machinery. This is followed by the use of high temperature gases to modify the electrical properties of the wafers. The final stage of annealing consists of extreme pressures to create crystalline oxide, also requiring temperatures in excess of 1,000°C.
The corrosive, thermal, and pressure extremities of the semiconductor process is strenuous on a range of manufacturing equipment. Gas erosion, thermal distortion and pressure-induced damage are all real risks involved that can inhibit production. Because of this, specialist metals such as aluminium alloys are used to extend the operable lifespan of components and maintain efficiency. That said, maintenance, repairs and replacement parts are still required after extended periods that put a halt to production.
Advanced surface technology: a solution to semiconductor machinery efficiency
Advanced coating solutions allow manufacturers to protect their industrial equipment from the extreme conditions of semiconductor production. A result of this additional protection, manufacturers are able to minimise the downtime of production, limit the cost tied to maintenance and extend the lifespan of components. This gives businesses optimisation opportunities that are welcome in a seemingly bleak semiconductor market.
Plasma Electrolytic Oxidation (PEO) is a bespoke advanced coating solution that provides semiconductor manufacturers with versatility, reliability, and a longer lifespan for components. PEO coatings demonstrate excellent thermal and chemical stability, as well as high wear resistance and hardness for semiconductor manufacture.
The unique PEO coating process allows for the fine tuning of specific resistances with a crystalline structure that is resistant to through-cracking whilst allowing for flexion. Additional chemical resistances can also be achieved through the addition of a fluorocarbon-based duplex layer or sealer. To find out more about how PEO can help extend the lifespan of components in the semiconductor and other industries, send an enquiry today.
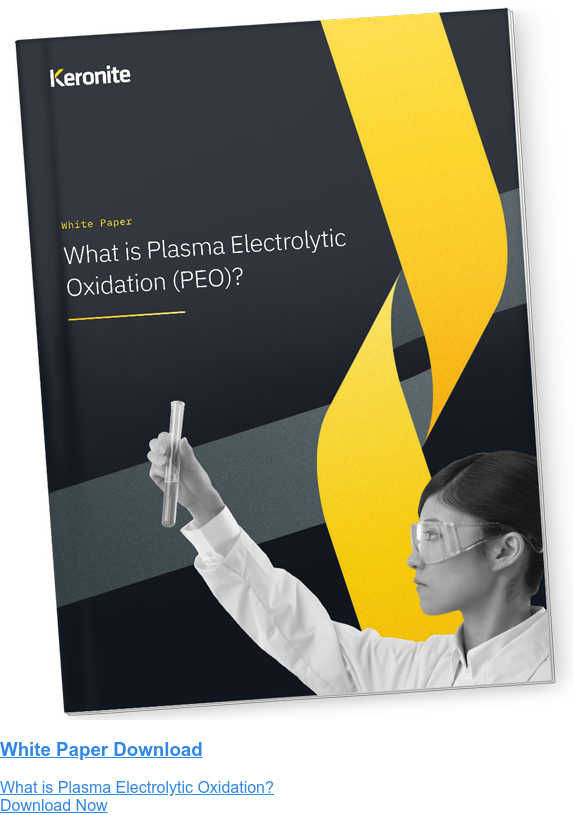
