Plasma electrolytic oxidation for high power industrial electrification projects
22 November 2021Electrification is taking place across a whole range of sectors, all over the world. In an effort to increase green credentials and adopt non-polluting sources of energy, fossil fuel-powered equipment is being replaced by high power electricity. Much of this electricity comes from renewable sources, enabling manufacturers to make a marked effort to improve their carbon footprint, with many aiming to produce net zero emissions.
Plasma electrolytic oxidation (PEO) is a surface technology that uniquely improves the performance of light alloys. The process allows manufacturers to reduce the weight of their components, enabling them to increase efficiency. Alongside this, the characteristics imparted through PEO radically boost the reliability and longevity of components.
The role of light alloys in industrial electrification
Many industrial activities are resource and energy intensive. From high-temperature manufacturing environments, to those that are highly acidic, machinery plays an important role in creating the products we use everyday.
Sustainability has become a priority on the agenda over the last decade. Coupled with calls to publish sustainability reports, manufacturers are expected to also present strategies for reducing greenhouse gas emissions and improving energy efficiency.
Electrification, naturally, seems the most important way to do this. It enables manufacturers to keep their processes, replacing energy consuming machinery and heavy transport with electric, clean alternatives that perform the same role.
High temperature manufacturing processes still rely heavily on coal and natural gas to heat components. Yet other areas of the manufacturing process, such as powering machinery, are moving towards electrification. Electric industrial motors are now being used across many manufacturing sectors and will likely account for a significant proportion of electricity demand in industry by 2040. This transition towards electric motors will be accompanied by other key process improvements, such as lightweighting equipment and energy recovery systems.
Electrifying heavy transport and manufacturing machinery
Reducing the weight of machinery and motorised process components can improve overall process efficiency. Engineers are looking to alternative materials, like light metals, to design and fabricate more energy efficient manufacturing facilities. Other sectors, such as transportation, have highlighted lightweighting strategies, making significant energy savings using aluminium or magnesium alloys for aerospace and automotive projects.
Aluminium and magnesium alloys developed for transport applications demonstrate excellent strength-to-weight ratios, good corrosion resistance, and have a relatively low cost compared with composite materials. These alloys are ductile and versatile and have the potential to be used in industries such as manufacturing. Their properties can be further enhanced using advanced surface coating technologies.
Surface coatings can improve the wear resistance, hardness, electrical insulating properties and strain tolerance of light metals, allowing them to be used in place of steel in manufacturing and transport equipment. High-speed machinery components are often exposed to harsh conditions, including abrasion, corrosion, and high temperatures. To extend the lifespan of these mechanical parts, reduce maintenance costs and avoid process downtime, the parts are coated to protect the underlying metal.
Plasma electrolytic oxidation for industry applications
Increasing the lifespan of components in intensive industrial applications
PEO is an innovative solution for coating light metals for use in industrial applications across manufacturing and transport. PEO coatings can be tailored to provide a variety of different surface properties. The coating’s application process involves submerging the metal component in an electrolyte bath and passing it through a current. At the surface of the metal, high temperature and high pressure conditions create a multilayer ceramic coating. The properties, including coating thickness, can be modified by altering the composition of the electrolyte bath and the voltage sequence during processing.
The plasma modification process allows elements of the electrolyte mixture to be incorporated into the ceramic coating composition. The resulting coating has a unique microstructure, with a uniform, tightly packed oxide layer at the metal’s surface and a porous outer layer. This outer layer can be impregnated with polymers such as polyetheretherketone (PEEK) to improve lubricity to reduce friction and wear. PEO coatings can also be used as a primer to ensure adhesion of secondary coatings, such as epoxies or fluoropolymers. These duplex systems can be used where enhanced corrosion protection is required, or to achieve specific surface properties and aesthetics.
The PEO application process itself is sustainable and environmentally friendly. The electrolyte solutions used are water-based, chemically benign and contain relatively low concentrations of chemicals. Submersion in an electrolyte bath also means that components with complex geometries can be coated uniformly, with minimal risk of through-thickness cracking.
Lightweighting and efficiency boosting
PEO coatings are currently used in a wide variety of industrial applications, from automotive brake discs to subsea defence machinery, demonstrating an increasingly impressive performance record. They enable light metal alloys to be used for lightweighting in applications where they cannot normally be used without enhancing their natural properties.
For more information about PEO coatings, and how they offer commercially attractive solutions that enable light alloys to be used in more sustainable manufacturing, get in touch. Our experienced team of materials scientists can develop custom coatings for aluminium and magnesium. This will provide corrosion and wear resistance and insulation in new electrical applications.
To find out more about PEO, download our whitepaper.
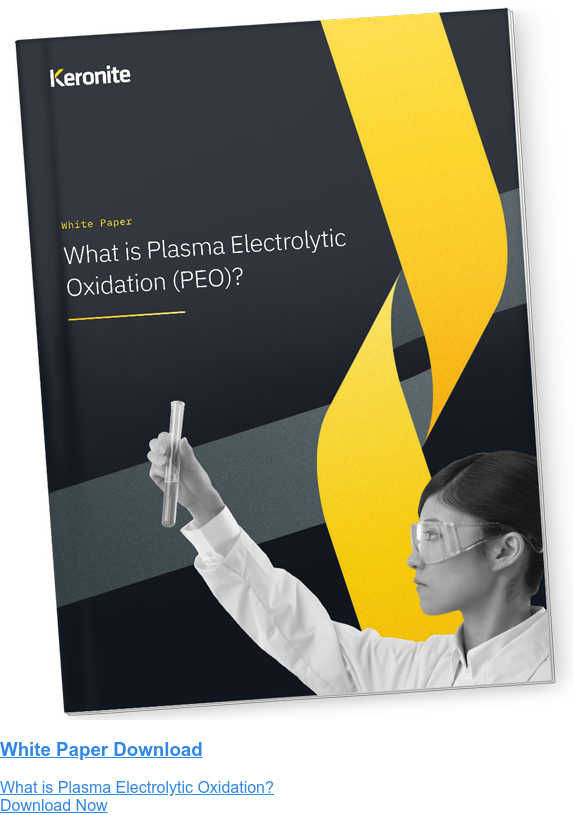
