Minimising particulate emissions from passenger vehicle brakes: strategies and technologies
13 September 2021The automotive industry places a lot of focus on replacing heavier iron components with lightweight alternatives such as aluminium or carbon composite. This is especially true in high-performance vehicles for motorsport, where every kilogram counts. Recent research shows that iron brakes not only add unnecessary weight to a vehicle, but they’re also contributing to particulate emissions and air pollution.
Iron brake discs are commonly used across the automotive industry. They have been used for decades and are an established, cost-effective technology. A robust supply chain system exists for iron brake discs in the automotive industry as the concept and design has hardly changed in over 50 years.
There are two main drawbacks to using iron brake discs in passenger vehicles. Firstly, they’re heavy. The main challenge for automotive engineers over the last few years has been to increase engine efficiency and reduce CO2 emissions. Reducing the weight of the vehicle will improve fuel economy and reduce running costs. As using electric and hybrid vehicles becomes more widespread, reducing vehicle weight will allow for a longer range, allowing for an increased travel distance on a single charge.
The second issue with iron brake discs is particulate emissions. The cast iron brake discs of road vehicles are the main source of iron particulates affecting air quality. Usually, a car’s braking system is made of an iron brake disc and a high-friction polymer-based brake pad. Over time, we see significant wear to both the brake discs and pads, which leads to them being replaced to ensure passenger safety. Wear on brake discs and pads generates particulate matter which contributes to air pollution, something which continues for the entirety of a car’s useful life.
Particulate matter from traffic
Exhaust emissions have long been recognised as a contributor to air pollution. There is legislation in place which requires car manufacturers to ensure vehicles remain below specified levels of carbon monoxide, nitrogen oxides, hydrocarbon, and particulate matter emissions.
Although many studies on air pollution focus on exhaust emissions from traffic, there has been more recent research that shows that small solid particles constitute a significant proportion of non-exhaust particulate matter. Studies show that, since exhaust filters have improved, particulate matter originating from brake wear, tyre wear and road surface wear now makes up a significant proportion of particle pollution in the air.
A report from the UK Government’s Air Quality Expert Group highlighted the problem of non-exhaust particulate matter to Environment Minister Therese Coffey in 2019. She commented that, “It is not just fumes from car exhaust pipes that have a detrimental impact on human health, but also the tiny particles released from their brakes and tyres.”
However, there is currently no legislation in place to restrict non-exhaust emissions from passenger vehicles. Particulate matter levels are difficult to measure, and it is also difficult to identify the source. Independent testing company Emissions Analytics carried out real-world testing to measure tyre wear. They found that a typical family hatchback emitted approximately 5.8 g/km of particulate matter. Compare this to 4.5 mg/km of permitted exhaust emissions and we can see that particulate emissions from tyre, brake and road wear pose a considerable threat to air quality.
Particulate matter from car exhausts is predominantly made up of carbon products from incomplete combustion. Tyre wear and road wear also contribute some organic particulate matter but cast iron brakes generate ferrous particles. However, it is not the chemical make-up of these particles that cause a problem, it is their size.
Particulate matter is categorised into PM10 (larger particles in the 2.5–10 μm range) and smaller PM2.5 particles. Both can have significant detrimental effects on human health. A study by the WHO looked at the levels of particulate matter across Europe and warned of the impact on respiratory and cardiovascular health.
Laboratory-based studies on cast iron brake discs show that the particulates generated from brake disc wear vary considerably in size; from tens of microns to just a few nanometres diameter. Particles of this size can be inhaled and penetrate deep into the lung tissue, causing a variety of pulmonary health conditions.
Alternatives to cast iron
A range of alternatives to cast iron brake discs are used in high-performance applications such as motorsport.
Carbon fibre reinforced ceramic (CFRC) brakes are now used in Formula 1 cars. They’re lightweight and can withstand the high temperatures generated from friction during braking. However, this material is expensive and only suitable for use in high-performance vehicles. Aluminium metal matrix composite have also been trialled in the past but they’re less effective than CFRC and still expensive to produce.
The use of aluminium or magnesium alloys for brake discs could be an affordable, viable solution for the automotive industry. But it’s well known that these light-weight metals are susceptible to wear. Keronite has been working alongside a leading automotive component manufacturer to find a solution to this.
Aluminium alloys coated with a ceramic PEO coating could have the wear-resistance required to minimise damage and particulate emissions. They offer a more reasonably priced alternative which is lighter than iron and enables the brake designer to specify the properties of the coating. Find out more about Keronite’s ongoing research project into aluminium brake disc coatings here.
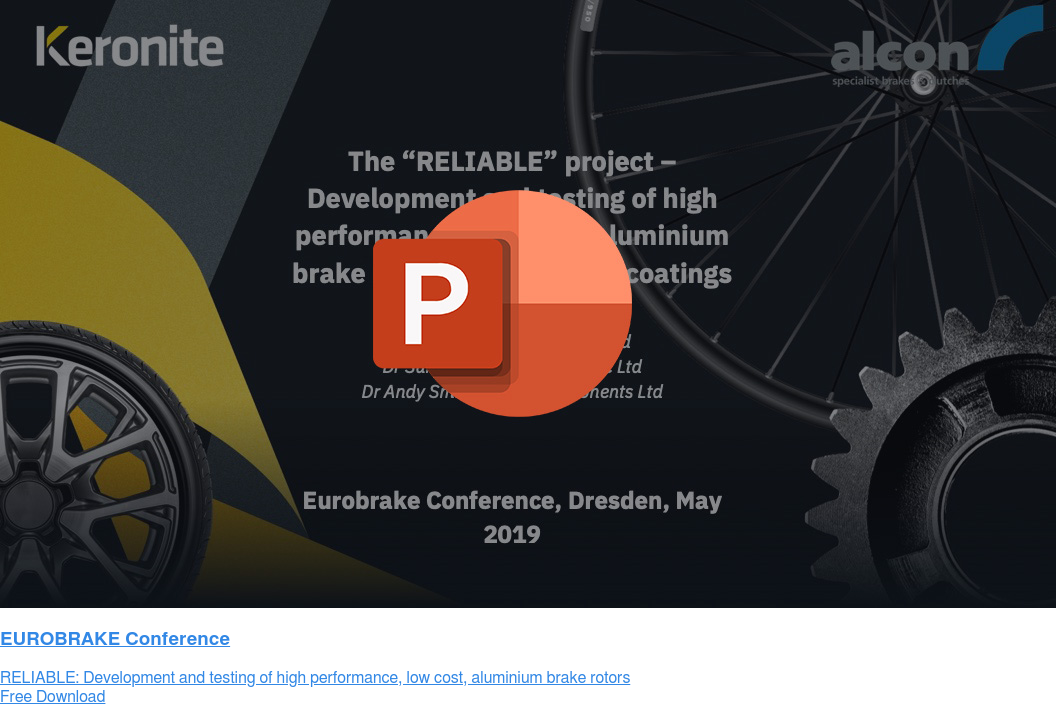
