Overengineering in the automotive industry
20 September 2021Overengineering is a term used when product designers and engineers include more features than are strictly necessary for the end-use. It is also used to describe processes that are more complex than they ought to be, making them inefficient. This can result in products that are over-priced, unnecessarily complicated and harder to maintain.
Can overengineering be a good thing?
Some industry sectors value overengineering. NASA scientists overengineer certain craft in the hope that they can extend missions and collect more data. Overengineering in terms of computational power and memory also allows more data collection and the potential for software updates. NASA’s Opportunity rover is a good example of this. The original mission was planned to last 90-sol (sol is the term used for a Mars day which is slightly longer than an Earth day). Instead, thanks to overengineering, the rover continued to operate for 14 Earth years longer than expected. This allowed scientists to investigate rocks, meteors, and craters on the surface of Mars for a significant amount of time.
Other examples of overengineering are less positive. In the US, a start-up called Juicero developed a juicing press to squeeze out their pre-prepared juice pouches. The press cost over $400 and faced huge criticism when consumers discovered that the juice could be squeezed out just as effectively by hand. The press itself was deemed completely unnecessary and the company closed shortly after.
When it comes to the automotive industry, overengineering can have its advantages and disadvantages. Sports cars can be considered overengineered; they’re designed to be driven on the road yet have top speeds that can only be reached on a track (due to legal speed limits) – something most drivers never do. Porsche recently unveiled their latest performance roof box, which has been tested up to 124 mph, a speed which is illegal on most roads. Other features that could be considered overengineered include high-powered air conditioning systems, dashboard warning signals and complex in-car entertainment interfaces.
The problem with overengineering cars
Overengineering is characterised by wasting resources such as materials, time and money. Many global car manufacturers have implemented lean manufacturing processes, to reduce waste, improve quality and avoid overburdening production lines. They aim for speed and consistency on production lines and keep component inventory to a minimum. But we can also look to the design of the vehicles themselves to embrace lean design principles.
Overengineering can result in unnecessary features and components added to the vehicle. However, we sometimes find that what is once considered overengineering becomes commonplace in the market and is then considered necessary. For instance, when Mercedes introduced a passenger airbag and all-wheel ABS they were criticised as excessive in terms of safety provision. Now you’d be hard pushed to find a car without these features, and cars on our roads have more safety features than ever. The same could be said of LCD screens or LED interior lighting, which are now standard in a wide range of passenger vehicles.
One of the key difficulties with overengineered vehicles is the complexity involved. If one component fails, it can have a knock-on effect on others. For example, a wiring failure can look like a sensor failure, and it can be difficult to diagnose the problem. Electronic failures or even software issues can affect the running of the car.
From a consumer perspective, an overengineered car may incur higher maintenance and repair costs. Many vehicles have parts that are designed to be replaced after a period of time, such as tyres or brake pads/discs. Yet, in some car models, you need to use specific tools, software, and expertise, which come at a premium. Audi, for example, require the ABS system to be disabled before changing the brake pads to avoid damage to the ABS and sensors. This means you must take the car to a manufacturer-approved centre for repairs.
Finally, extra components mean extra weight. All cars have the same basic components; wheels, engine, steering wheel, braking system, pedals, doors, seats etc. So, all the extra parts that make the car more comfortable and easier to drive are contributing additional weight to the vehicle. More weight means lower fuel economy, higher emissions, and increased running costs.
Using aluminium components
The additional weight of on-board computer systems, passenger air bags and bumpers can be justified as they improve safety and comfort. Automotive engineers can look to use light-weight components elsewhere in the design to compensate for the extra weight of these features. One method is to use lightweight metals or other materials in place of steel or cast iron.
Aluminium is a lightweight metal that has the potential to be used for various components in the automotive industry. It’s strong, malleable, and ductile so can be bent or extruded into a variety of different components. However, it is also susceptible to wear and abrasion. To use aluminium in the automotive sector, it’s important to select the right alloy and the right surface treatment.
Keronite have been working with a leading component manufacturer for brake discs to develop an aluminium replacement for cast iron discs. The brake disc is fabricated using an aluminium alloy, then coated with a wear resistant PEO coating. Initial tests show promising results, with increased friction, brake performance and minimal wear. For details of the performance of PEO coated aluminium brake discs, read our research project report.
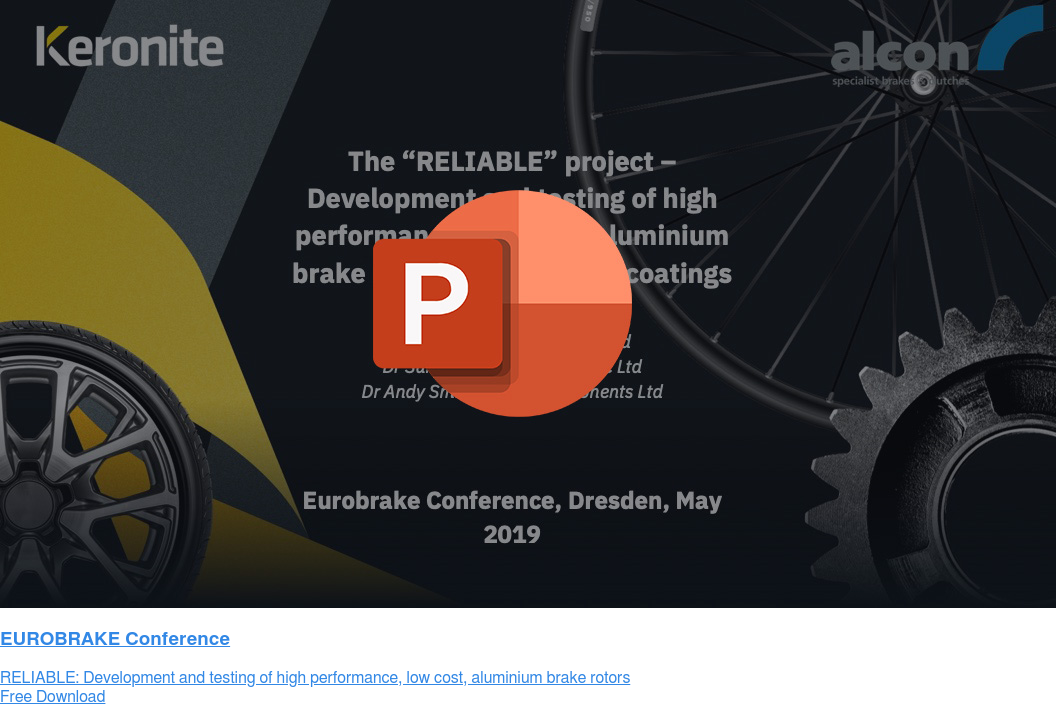
