Manufacturing into 2021: the journey beyond recovery
21 October 2020There’s more than one reason to be upbeat about the prospects of the manufacturing industry over the coming years. Numerous reports state that the worst of the impact felt by the manufacturing industry has passed. That is not to say that everything is suddenly rosey, the global manufacturing sector still has progress to make to get to pre-pandemic levels. But unlike the credit crunch, the path beyond recovery is not one of austerity: but one of investment, focus and partnership.
Strategically speaking, manufacturers have taken a range of different approaches to guide them through the adversity of this year. Some sought to refocus, cut loose the ‘fat’ from their organisations and double down on their strongest organisational competencies. Others took less radical change, instead began exploring more integrated relationships with their partners to build value.
This global buoyancy story is supported by multiple industry reports, including:
- The US National Association of Managers Outlook Survey: Third Quarter 2020 is almost entirely green across key metrics. Small numbers, but positive across growth, investment and employment. Only inventories look to shrink in the next 12 months.
- Europe’s manufacturing activity resurgence has been led by Germany, with the IHS Markit Eurozone Manufacturing PMI stating: “Eurozone manufacturing growth strongest for over two years.”
- In the UK, the picture is similar “as new work intakes improved from both domestic and overseas markets”, according to the IHS Markit / CIPS UK Manufacturing PMI.
- The outlook in Asia is mixed. Whilst Japan’s au Jibun Bank Japan Manufacturing PMI is upbeat about prospects, the ASEAN manufacturing sector declined at the end of Q3 2020, shown by the IHS Markit ASEAN Manufacturing PMI. But China’s impressive GDP growth between July and September underpins the growth story.
The outlook appears positive, and this appears to be presenting new opportunities for manufacturers to capitalise on resurgent global demand. But how exactly are organisations gearing up for this resurgence?
Writing in April 2020, Deloitte’s Punit Renjen highlighted the importance of looking outside of an organisation to foster stakeholder trust. An earlier Deloitte report, its 2020 manufacturing industry outlook, was even more prescient. It highlighted how many US industrial companies were focusing on their core competencies to improve results.
Focus: finding core activities to build value
The first business response to a crisis is, often, to examine and reduce costs. Layoffs and redundancies were reduced through initiatives such as furlough schemes, which subsided employee wages while hours were reduced. This has allowed manufacturing organisations to save on costs while retaining their organisational structure and headcount. So instead, organisations seemed to take a rather more long-termist approach.
10 years prior to this pandemic, in response to a different crisis, a Harvard Business Review article, When you’ve got to cut costs – now, by Kevin Coyne et al, examined how to do just that. This article is packed with useful strategies, including looking at areas that usually would not feature on the typical cost-cutting checklist.
One of the recommendations is to Shift the burden to the most efficient location. This is the recommendation to develop synergistic partnerships. Where you have a good relationship with manufacturing partners, examine exactly where you can extract more value from them. At Keronite, we know that materials science expertise can be hard to find. To meet performance specifications, the parts may require a dozen different types of surface coatings. Is having a department that handles hard anodising, paints and powder coating, chrome plating, plasma electrolytic oxidation and plasma spray coatings likely to be as efficient as five companies that devote their existence to these solutions?
How to create worthwhile manufacturing partnerships
Having identified the non-core activities within a manufacturing operation, companies require a supplier-relationship strategy. Deloitte goes on to say:
“Many manufacturers are actively mobilizing partnerships within their ecosystem that can drive targeted business goals, ranging from bolstering a traditional area (e.g., improving customer experience) to adding new capabilities (e.g., creating new business models). Recent Deloitte research showed that a group of digital front-runner manufacturers were executing in these areas at a much higher rate than their peers.”
All the current evidence, based on both the sentiment and hard data published by the reports above, suggests the outlook for these front-runners is positive. But only if they seize the market opportunities through introducing strategies such as creating partnerships with a trusted ecosystem of supply chain partners.
Manufacturing has a unique combination of generating typically higher-value and higher paid employment, an export bias and creating supply chain ecosystems that evolve to support it. These factors, plus others, writes Heap & Partners’ managing director David Millar in The Engineer, provide disproportionately greater support for economic recovery.
Keronite’s scientists are world leaders in an advanced surface technology called plasma electrolytic oxidation (PEO). The conversion coating process uniquely improves the performance of light alloys by enhancing them with an ultra-hard ceramic-based coating. PEO delivers a wide range of performance benefits for many applications.
Keronite is already working in partnership with leading manufacturers to find superior solutions for their materials. Our in-house scientists are examining methods to improve the performance of light metals, valve metals and their alloys.
To learn more about the work Keronite does, or to get in touch with our team to discuss how you can improve the performance of your light alloys, get in touch.
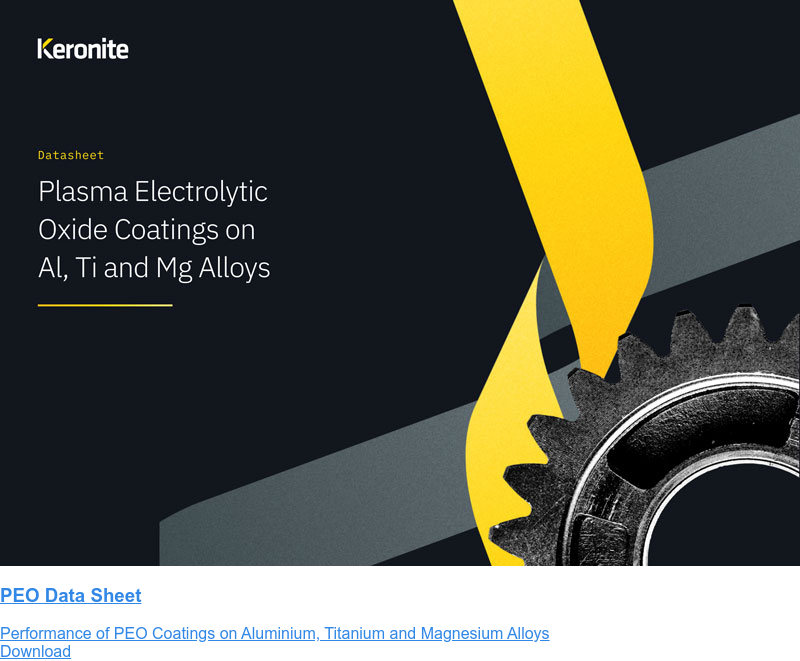
