Magoxid and Keronite: PEO coatings for Mg alloys
13 October 2020Lightweight metals have become essential materials for the components used in aerospace, automotive, defence, industry, medicine and many other sectors. As these applications become more demanding, the unique combination of low weight and high strength often make lightweight metals the only viable choice for engineers.
Light alloys are not, however, complete solutions on their own. Magnesium, for all its advantages, is highly chemically active, as well as featuring low hardness, poor creep resistance and a concerning degree of flammability. For applications that need to be corrosion and wear resistant, magnesium is therefore not always thought of favourably. That is until you consider the range of advanced coating solutions that enable magnesium’s use in extremely testing conditions.
Surface coatings for improving magnesium's performance
Advanced surface coatings are capable of improving the performance and life of light alloys. These can ensure the surface is protected from wear or corrosion by process chemicals and substances in the operating environment.
Coatings come in various forms, such as a paint or plated material on top of the substrate, or through a conversion coating process, such as anodising or plasma electrolytic oxidation (PEO).
As well as providing performance enhancements, coatings can modify the characteristics of the surface in other ways. This could be improving the friction coefficient, introducing antibacterial properties or even improving the dielectric breakdown strength. Each coating is capable of improving these materials in unique ways.
Conversion coatings for magnesium
Conversion coatings are among the most powerful coatings available for light alloys. Due to the method of coating, they adhere extremely well to light alloys, even growing into the substrate itself. This sort of coating, and the coverage provided, makes it extremely difficult to find alternatives that offer the same degree of protection.
Plasma electrolytic oxidation (PEO) is a bath-based conversion coating process that uniquely improves the performance of light alloys. It is frequently used in industries where light alloys can replace heavier metals to improve fuel efficiency and where the life of materials are extremely important, such as defence and industry. Yet research increasingly provides new opportunities to bring additional characteristics to these materials.
Plasma electrolytic oxidation (PEO)
Magnesium alloys with advanced surface coatings, due to their high strength-to-weight ratio, are a great choice for components requiring protection from a variety of modes of failure.
To coat magnesium components, they are placed into an electrolyte bath. Components do not require any sophisticated cleaning processes, such as would be required through an electroplating regime. Once immersed, an electric current is then passed through the bath and a double layered oxide coating develops on the light alloy substrate, shown in figure 1. The top layer is porous and the bottom is impervious. The electrolyte also becomes part of the coating, which is further modified by a plasma discharge during the coating process.
Figure 1.
Scientists have long experimented with each of the variables controlled during the plasma electrolytic oxidation process, yielding interesting results. With this understanding, materials scientists can effectively tailor the electrical regime and electrolyte contents to promote characteristics for every individual application. So, the PEO-coated magnesium components gain wear, corrosion and heat resistance qualities required for the application. Furthermore, the uniquely porous nature of the upper coating layer enables the addition of substances that increase the surface lubricity of the component, increasing its anti-friction properties.
PEO options
Even within the branch of plasma electrolytic oxide coatings, there are a number of performance differences. Keronite’s technologies for magnesium differ from those such as Magoxid. Fundamentally, the technologies and deployment of these coatings are different, which can make a lot of difference when finding a coating that protects a component in a highly sophisticated use case.
Materials engineers benefit from some fundamental advantages with PEO over other coating technologies. These include the fine control of the deposition process, the unique dual layer with top-later porosity and the ability to customise the electrolyte.
Optimising each of these approaches to the application requires high degrees of both science/technical knowledge and know-how alongside extensive experience of applying the technology at industrial scale. This is particularly true when challenged with a particular application that requires a unique set of surface coating characteristics. And this is where the difference lies between the two technologies.
Comparing technologies: Keronite and Magoxid
Keronite’s technology has been delivered by the company of the same name since 2000 – in fact, PEO was the initial driver behind the company’s launch and it built the world’s first purpose-built PEO coating facility in 2007. This has since expanded to multiple locations and licenced partners worldwide, including a UK-based automated line.
The MAGOXID PEO technology is relatively recent in comparison, and lacks many of the features that the Keronite technology include. This significantly widens the scope of potential applications of the Keronite technology.
Alongside its global production and partner infrastructure, another strength of the Keronite technology approach is the science behind the solutions.
The Keronite technology is supported by a large in-house materials science team that benefitted from over £1m of investment during 2019/20, and a dedicated PEO technology centre was opened in 2018. It also has strong links with academic research, notably the University of Cambridge’s Gordon Laboratory in the Department of Materials Science and Metallurgy.
Keronite has been actively delivering surface solutions across multiple sectors where high performance materials can be found. As a result, its scientists and engineers and global partner network have acquired unrivalled application-specific solution design knowledge and production know-how.
What about for industrial scale manufacturing?
This has led to many innovations on the PEO process and resulting surface coating solutions. The duplex coating system developed unique to the Keronite technology enables specific performance capabilities to be designed in. This enables the Keronite technology to be used in a wide range of specialised applications where MAGOXID cannot.
Research into the mechanism of how the particles from the electrolyte become part of the surface coating by Cambridge University and Keronite has shown that pores can be ‘filled’ with other materials that are included in the electrolyte. For example, because of the high porosity of the outer layer and limited phase composition range, basic PEO coatings on magnesium alloys do not provide long-term protection from wear. This would restrict PEO’s use in some tribological applications.
However, Keronite’s technology uses techniques to include aluminium oxide particles in the electrolyte that became incorporated into the surface layer of magnesium oxide during deposition. This significantly increased the hardness and the resulting wear resistance.
The combination of science and application knowledge, alongside production know-how and both specialist and high capacity production capabilities with global availability means Keronite’s technology delivers both a superior engineering and commercial solution.
To find out more about how PEO coatings perform on light metals, click below to download the whitepaper. For an unbiased assessment of the best surface coating for your project or application, speak to our technical team.
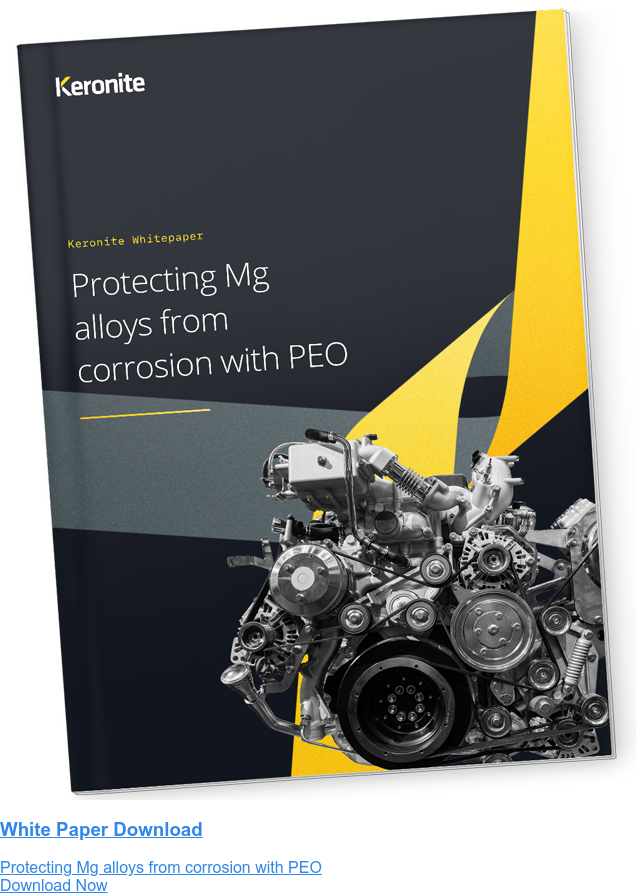
