Keronite’s PEO thermal barrier coatings improve internal combustion engine efficiency
6 September 2021When it comes to selecting light alloys, most engineers do not venture far from Al, Mg and Ti alloys. However, this article explores the uses and benefits of some of those lesser used light alloys, such as Zirconium, Tantalum and Hafnium.
UK and European governments are curtailing the sale of petrol and diesel passenger vehicles by 2040. However, internal combustion (IC) engines are projected to remain in use for heavy duty applications such as freight, rail, and marine transport. As a result, the need for more energy-efficient and eco-friendly modifications for IC engines remains.
Keronite has been working alongside materials scientists at the University of Nottingham to develop and test Thermo-Swing PEO coatings for engine pistons, with the aim of reducing heat loss and improving combustion engine efficiency. The research, co-written by materials scientists at Keronite, has recently been published in Applied Thermal Engineering.
The role of thermal swing coatings
Improving engine efficiency means optimising the conversion of fuel chemical energy into useful work. A typical diesel engine can lose up to 60% of fuel energy as waste heat, which is absorbed by the coolant or dispersed into the exhaust gas. To overcome this heat loss, the concept of using thermal barrier coatings was introduced in the 1980s. This is typically a thin ceramic coating, historically Yttria Stabilized Zirconia (YSZ), which exhibits low thermal conductivity. These coatings can be applied to the entire combustion chamber, or to specific components such as the piston crown, cylinder head, liner, or valves.
In recent times, advances in materials technology, coupled with the movement towards zero-carbon vehicles has renewed the industry’s focus on these coatings., Toyota, for one, developed a coating that encompasses Thermo-Swing Wall Insulation Technology (TSWIN). This material has the capacity to rapidly change temperature in a more dynamic way, to follow the temperature of the internal gases. These types of coatings are characterised by low thermal conductivity and low heat capacity. The surface temperature of the aluminium piston coated with a TSWIN coating increases during the combustion period and decreases during the exhaust and intake strokes of the engine. This reduces heat loss (compared with an uncoated piston) and prevents intake air increasing in temperature, an issue seen with traditional thermal barrier coatings.
Toyota’s TSWIN solution is a Silica Reinforced Porous Anodised Aluminium (SiRPA) coating. The main drawbacks of anodised coatings are surface roughness, porosity and non-uniform coating thickness. Each of these factors has the potential to reduce insulation performance, although surface roughness is sometimes overcome by an additional layer of silicone-based sealer.
Materials scientists at Keronite have been working with the University of Nottingham to create a coating which behaves similarly to a TSWIN coating, with ultra-low thermal conductivity and heat capacity, but with more consistent coating thickness, high porosity and a smooth surface finish.
Developing a new coating technology
As the world leaders in the coating technology, Keronite’s Plasma Electrolytic Oxidation (PEO) technology that uniquely improves the performance of light alloys such as aluminium, magnesium, and titanium. The technique involves immersing the aluminium pistons in an electrolyte solution. An electric current is passed through the metal substrate and a unique oxide coating forms on the substrate surface. The coating exhibits ingrowth, ensuring high levels of adhesion. Depending on the desired properties of the coating, different electrical sequences can be used. It also ensures a consistent through-coating thickness, even on bends and surfaces with complex geometries.
The composition and concentration of the electrolyte solution determines the composition and resulting properties of the coating. In this case, a sodium silicate and potassium hydroxide solution was used as the electrolyte, to form a coating composed of alumina and mullite in approximately equal proportions. The experimental PEO coating was found to be highly porous, further reducing thermal conductivity thanks to the air trapped within the porous microstructure. It had a considerably reduced surface roughness, which can be improved by adding a silicone-based sealer.
Following the development of the PEO coating, it was tested under road-realistic conditions – under part-load. The results showed excellent performance under thermal cycling conditions and good substrate adhesion. Laboratory-based emissions testing demonstrated that the PEO coatings developed between Keronite and the University of Nottingham showed promising signs to reduce NOx emissions, soot and total hydrocarbon (THC) emissions.
At the forefront of automotive coating technologies
The full paper, Plasma electrolytic oxidation thermal barrier coating for reduced heat losses in IC engines, is available to read in Applied Thermal Engineering and has been co-authored by Keronite scientists Robin Francis, Suman Shrestha and Ankit Khurana, together with the University of Nottingham’s Department of Mechanical, Materials and Manufacturing Engineering. Read the full paper here.
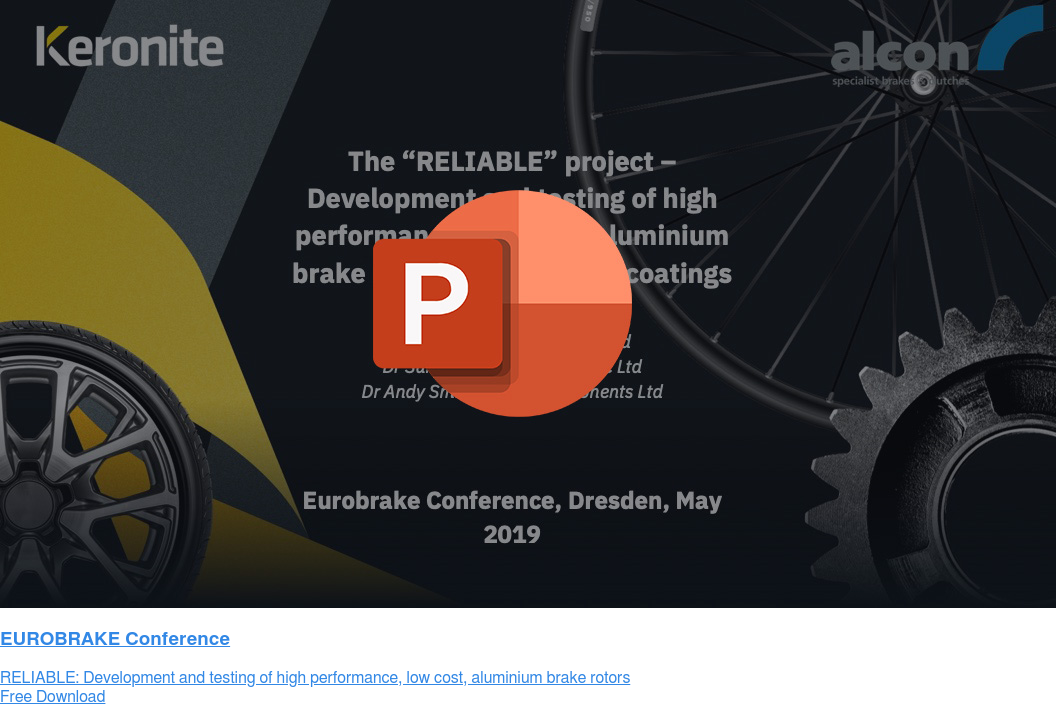
