How innovations in materials science are reducing PM10, NOx and CO2 emissions
19 June 2019Carbon emissions and air quality are the two biggest environmental challenges facing us today. The transport industry produces around a quarter of greenhouse gas emissions in Europe. Consequently, regulators have imposed strict deadlines that implore automobile manufacturers to take action right now.
From 2021, passenger vehicle manufacturers must meet a new 96 g/km carbon emission limit. This is the first time that this limit will apply to all new vehicles. Manufacturers that fail to meet the new limit will face fines (called the excess emissions premium) for every unit in excess. A recent report has suggested that as many as 8 of the big 13 manufacturers will be some way off meeting the targets.
In a quest to reduce emissions and improve efficiency, automotive manufacturers are looking to reduce the fuel consumption and emissions created by their vehicles. Fortunately, the materials science industry has created some intriguing opportunities to reduce both direct (tailpipe) and indirect emissions.
Brake technologies
By design, braking involves huge energy losses. All the kinetic energy is converted into heat in conventional braking systems. Conventional braking is also one of the leading causes of particulate matter from vehicles. For both reasons, the prospect of finding a better alternative is an exciting one.
Brake discs
Recent research in brake disc materials has highlighted several critical features that could both lightweight the ‘unsprung’ mass of a vehicle and reduce particulate emissions. The unsprung mass of the vehicle – the weight which is not borne by the suspension – is said to have a larger impact on fuel economy than the sprung mass. Therefore, reducing this mass will make a greater improvement to fuel economy and emissions.
Cast iron brake discs have been the norm up to now. However, a current Innovate UK project by Keronite, in combination with Alcon, has highlighted that aluminium brake discs, protected by plasma electrolytic oxide coatings, could prove the answer. They are 50% lighter, demonstrate very low wear and nominal particulate emissions – all while delivering the equivalent performance to a cast iron brake disc.
Lighter regenerative braking systems
Many of today’s hybrid-electric and battery-powered cars feature regenerative braking technology technology, but there are still intriguing improvements to make nonetheless. Regenerative brakes create fuel savings of up to 3%, simply by capturing that lost energy through an alternating current circuit, gearbox, motor and a battery. While these systems enable the capture of this energy, they also add a considerable number of components, each with a number of unique modes of failure. To ensure that the impact of this added weight can be mitigated, using a lightweight brake disc protected by an advanced surface coatings is a possible solution.
Pistons
Thermal management within the internal combustion engine offers benefits to fuel economy as well as emissions. Recent development projects carried out using plasma electrolytic oxidation (PEO) has demonstrated that a ceramic layer on the piston can deliver thermal solutions that manage temperatures with demonstrable benefits in both fuel economy and cold start emissions.
Engine Stop-Start (ESS) Systems
While the regulatory environment changes, so does the environment for drivers. With more congestion than ever before on roads, drivers are spending more time in traffic, while the engine idles and burns through fuel.
Engine Stop-Start (ESS) Systems were introduced to reduce fuel consumption while stationary. Depending on the traffic conditions, they can save up to as much as 12% on fuel. However, by initiating the engine ignition cycle far more times than in cars without, starter gear can get worn out far more quickly – offsetting any financial advantage over the long term.
Yet surface coatings that offer improved metal-on-metal wear protection could demonstrate an effective way forward. Aluminium engine ring gears and pinions may be made more wear-resistant, reducing their total life cost and further improving reliability.
Lightweighting for the future
As vehicle designs now sport bulky electric motors, electric batteries and other hybrid technologies, finding new ways to reduce weight has become critical. With far more components than ever before, reducing a vehicles’ weight by 10% will equate to a ~7% improvement in fuel economy. Making the most of lightweight materials and technologies that enhance them is absolutely critical to meeting the demands of the future.
Aluminium and magnesium, in particular, are being used far more to save weight. There are some automakers that have begun to explore the opportunities provided by the lightweight metal. Magnesium, for instance, could be enhanced to work in the following applications:
- Exterior (body) panels
- Engine blocks
- Chassis
- Gearboxes
Advanced surface coatings like plasma electrolytic oxidation are capable of producing ultra-hard ceramic coatings that protect components like these from wear, high temperatures and corrosion. Keronite’s materials scientists are world leaders in PEO technology and have developed best-in-class solutions for automotive manufacturers for all kinds of components and systems. To consult our technical team, please get in touch with a few details on the project and they will be pleased to introduce you to our technology.
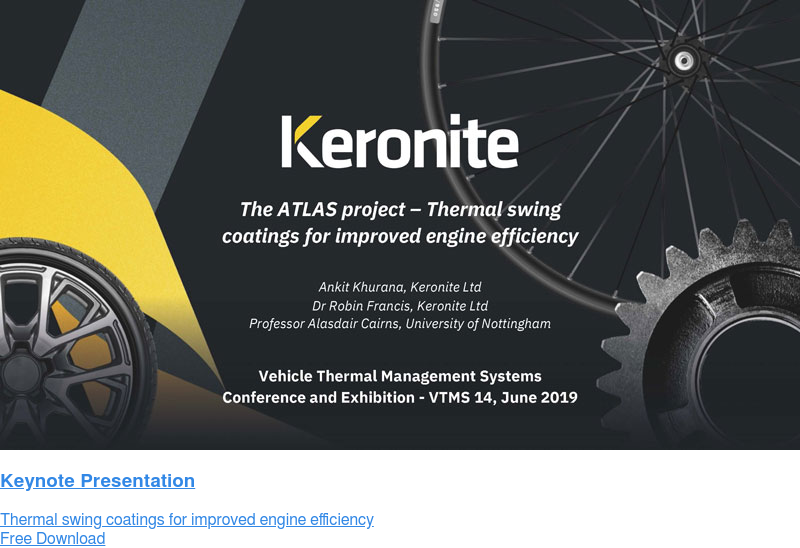
