How to maximise light alloy performance in intensive applications
5 November 2019Choosing the right material and protective surface technology is often the difference-maker in sophisticated engineering projects. In order to produce a discernible improvement in performance among customers, surface technologies are key to maximising life and efficiency of new products.
In Project Sunrise, Qantas asked the aerospace industry to produce a design for an aircraft that could offer a 20-hour flight test. Both Airbus and Boeing pitched new designs to the airline that seek to minimise weight, while being able to carry commercial payloads. These sorts of projects require radical improvements in material performance.
By acknowledging the need for a specialist coatings early-on in the design, engineers are better able to optimise coating selection and development; thereby reducing costs, improving repeatability and enhancing product performance.
Why you should consider coatings early in the design cycle
By considering coatings early, engineers are better able to test any coating solution against their project requirements; as well as controlling and monitoring the coating processes for improved manufacturing efficiency. By doing this, engineers can reduce manufacturing costs, improve their product cycle time, and reduce the likelihood of costly product redesigns.
Process compatibility
Process compatibility refers to the material's ability to maintain structural integrity during the coating process. These processes might involve, for example, exposing materials to high temperatures or pre-treatments which can impact the structural integrity of components.
Undertaking development and testing before any design is finalised will likely mean coating processes are compatible with chosen materials; as well as helping to reduce any potential waste incurred through material warping or thermal expansion.
A holistic, early-stage approach to coating development will also give engineers a better understanding of which types of machinery and equipment will be necessary to manufacture the coating at scale, and how best to manage variables such as raw materials, labour and utility costs.
Mechanical compatibility
If a coating solution impacts the functional performance of a component, it has a low mechanical compatibility. Surface treatments can impact a components ductility, weight and surface roughness. This can cause mechanical issues that could compromise the feasibility of your design.
By integrating control processes throughout the development cycle; it is possible to undertake various coating solutions in a range of environments, and test on different materials; so that engineers can be sure their coatings are optimally matched to the material.
By precisely matching the solution to the substrate it is possible to maximise the longevity of the coating. This can be executed by testing and then selecting properties that generate the lowest stresses in the coating/substrate system. This is a difficult process, but if the coefficient of thermal expansions match relatively closely, the stresses generated during thermal cycling should be small - it is possible to perfect this process during the early stages of a design, while variables such as material type and coating solution can still be adapted.
Thickness and surface finish
If specialist coatings are considered as an afterthought it may be that the resultant thickness or finish undermines the product function; impacting, for example, the aerodynamic drag or heat transfer rate to the detriment of component performance.
In a wind turbine, for example, the extra mass on turbine blades also adds to the load on the turbine disk as well as on the turbine shaft and its bearings - seriously impacting on the engine life.
The impact of any coating solution on the surface of the material needs to be understood before the design is finalized. If a coating is drawn in too late, it could cause serious performance drops at the testing stage.
The right surface technology can make all the difference
The enhancements offered by coating solutions can be as fundamental to the success of a design as the materials themselves. Like materials selection, and component design; coating development needs to be considered from the outset. Involving coating experts at the early stages of a design cycle is the best way to optimise coating processes and performance. With coating development and design a central focus of a project, engineers can benefit from increased performance, improved repeatability, and reduced costs. If you’re considering a coating solution for an upcoming project, please get in touch with one of our experts here.
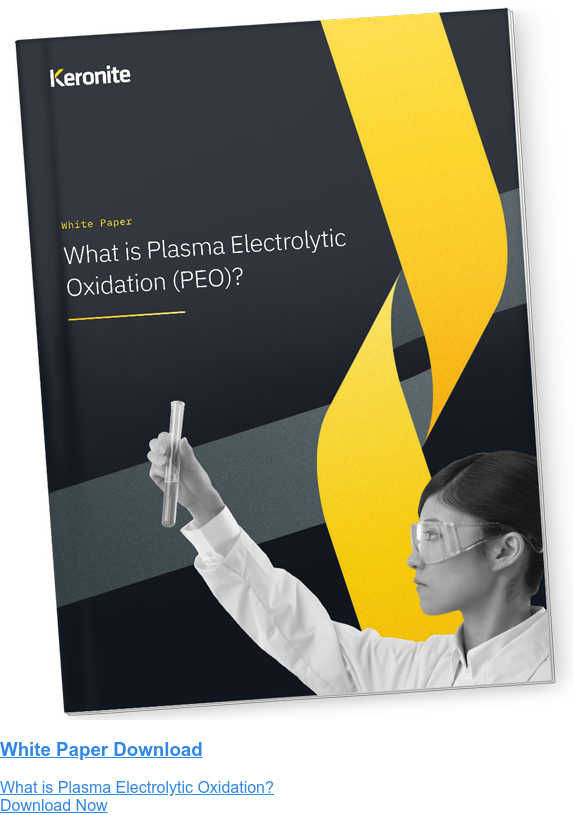
