How surface technologies are making Low-Earth Orbit satellites economical
1 June 2021Large tech companies are moving towards Low Earth Orbit (LEO) satellites to meet the demands of consumers in a global communications market. As satellite technology advances, engineers are looking to replace a limited number of high-orbiting geosynchronous satellites with thousands of smaller LEO satellites.
LEO satellites are small (100 – 500 kg) satellites that orbit the earth at a relatively low altitude. A typical LEO satellite will be placed between 200 km and 2000 km above the Earth’s surface. In comparison to existing geosynchronous satellites, they are much smaller and orbit much closer to Earth. This means they’re an excellent communications solution and can provide high-speed internet connection to remote areas, without the latency issues experienced from satellites in higher orbits.
Thousands of smaller satellites
LEO satellites for internet access use K-band communication frequency. This allows high bandwidth and smaller antennae, which is what enables the satellites themselves to be smaller. Another consequence of this is that they have a small field of view and can only communicate with a small geographical area on Earth. To increase coverage, LEO satellites are usually grouped in constellations, where all the individual units work together as a whole.
An example of this is SpaceX’s Starlink constellation, which is currently made up of around 1,600 individual units. Other tech giants such as Amazon and Samsung also have similar large-scale projects in the pipeline. Each satellite is expected to have a lifespan of approximately 5 - 10 years, after which it will lose power and deorbit before returning to Earth.
A short lifespan combined with the volume of LEO satellites proposed, will mean a dramatic shift in the design, manufacture, and deployment of satellites. Space technology companies are looking to produce satellites in the same way that the automotive industry manufactures cars. For example, OneWeb have already created a high-speed, high-volume satellite assembly line.
Minimising launch costs
The large volume of satellites required for LEO constellations means that significant value engineering exercises are underway across the space engineering sector. Scientists and process engineers are looking to reduce the cost of manufacturing the satellites, while maintaining the high performance required to withstand the hostile space environment.
Engineers are already tasked with minimising the weight of every spacecraft to reduce launch costs. With organisations planning to launch thousands of LEO satellites a year, reducing the energy required to get the craft into orbit promises significant savings.
Because LEO satellites operate at a lower orbit, the air is denser and they experience more aerodynamic drag. They require more power to correct their position and maintain their orbit. A reduction in aerodynamic drag would also incur financial savings and potentially extend the lifespan of the satellites.
Surviving in space, reducing lifetime costs
In addition to designing lightweight, aerodynamically efficient satellites from low-cost materials, engineers are also tasked with protecting the satellite from its surroundings.
LEO satellites are designed to orbit the Earth in a harsh environment; exposed to atomic oxygen, high levels of UV radiation and extreme thermal cycling. There is also a risk of damage from micrometeorites and space debris.
Many spacecraft components are made from either Kevlar, aluminium alloys, or titanium. Each of these is lightweight and strong but comes with their own limitations in terms of performance in a harsh space environment. They require additional coatings to protect the integrity of the satellite structure through the high-speed launch process and hostile environmental conditions.
Coatings are used to protect the metal alloys from the extreme conditions of space. Even within the Earth’s exosphere (up to 10,000 km altitude), satellites are exposed to significant amounts of radiation. Coatings can reflect UV and thermal radiation, and thermal barrier coatings can be used to reduce the effects of heat exposure during launch and thermal cycling in orbit. For example, aluminium is a relatively soft metal that requires a coating to improve hardness and wear resistance.
LEO satellites need a high-performance coating that fulfils all these criteria, as well as being cost-effective and easy to apply to a large volume of components. Many aerospace engineering projects look to plasma electrolytic oxidation (PEO) to provide the solution. Projects such as the MIR space station and the BepiColumbo mission to Mercury have successfully used PEO coatings to protect spacecraft in extreme space environments.
PEO coatings can be tailored to provide a combination of surface properties. They are applied to metals using an electrolyte bath with a high voltage current passed through. Changes can be made to surface properties by altering the composition of the electrolyte solution. The application process is simple, environmentally friendly and can be carried out on a large scale. Ceramic PEO coatings also provide a porous outer surface that has excellent adhesion properties if an additional polymer-based coating is required. When it comes to satellites surviving in space, PEO coatings provide the most effective, efficient and specialised method of protection.
To find out more about PEO coatings, how they are applied and the surface properties that they can provide, download our white paper “What is Plasma Electrolytic Oxidation?” using the link below.
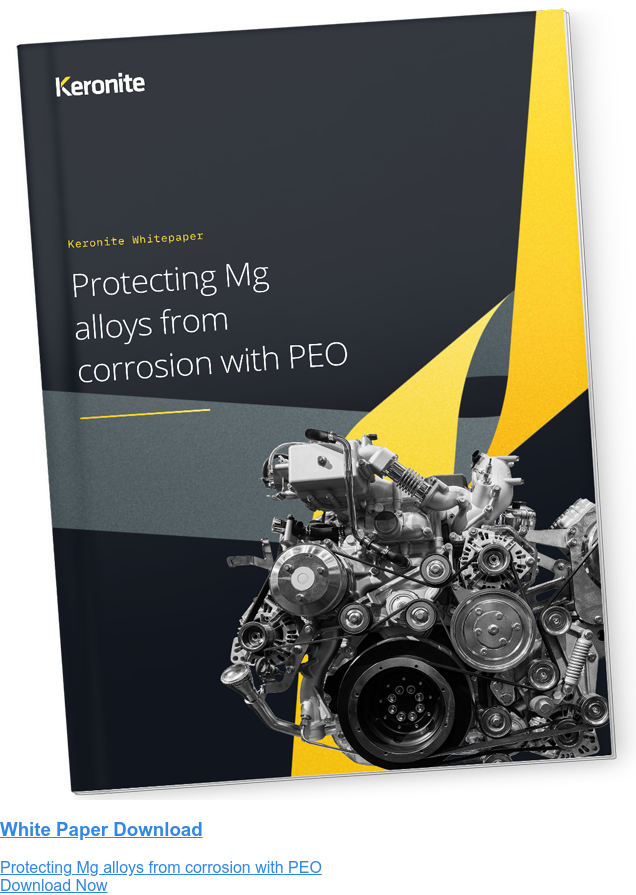
