How surface coatings manage the thermal conductivity of light alloys
1 June 2022In the mission to reduce the weight of critical components for the sake of efficiency, light alloys are an obvious choice. Across industrial machinery, aerospace and electronic equipment, light alloys are prevalent and great options for lightweight applications.
Yet as industries leverage more clean, low-emission technologies, the need for these materials to be lightweight, high performance, yet also long-lasting represents a challenge. Especially where, in high-power and high-temperature applications, thermal dissipation and heat sinking become crucial. This includes applications as diverse as:
- Electric motors in EV's
- Internal combustion engines
- Industrial robots and automation
- High-throughput factory machinery
- Friction-bearing surfaces, such as in rotors and gearboxes
In all these examples, machines and vehicles are required to be lightweight, high performing and safe – something of a challenge when factoring in the requirement for light components to have excellent thermal management properties too.
Surface coatings help manage the thermal properties of light alloys
Advances in surface technologies mean that light alloys like aluminium can be treated in order to protect components, improve their thermal performance and even provide protection from dielectric breakdown.
There are many considerations when specifying dielectric coatings for light alloys, as they carry out a range of functions:
- Increasing dielectric breakdown strength
- Reducing thermal conductivity (problematic if the component also has a cooling function)
- Altering optical properties – making components more or less reflective or emissive
Engineers must balance the insulating properties delivered by chosen materials against other considerations such as weight, lifespan and corrosion resistance – high or low thermal conductivity is not the only requirement of a specified component. Insulators used in applications like electric cabling, such as polypropylene, have dielectric strengths of 22 kV/mm, whereas surface-coated aluminium alloys have a dielectric strength ranging from 14.6-16.7 kV/mm. While relatively high, this clearly is not sufficient for many applications so special measures such as thermal sprays, hard anodising or plasma electrolytic oxidation are needed to form coatings with higher dielectric strengths.
Improving thermal barrier properties of light alloys with PEO coatings
Researchers at the University of Cambridge have tested the thermal barrier properties of plasma electrolytic oxidation (PEO) coatings, and found them to be in the order of 1 W/mK.
In contrast to thermal sprays, which are applied onto a substrate, PEO changes the composition of the alloy, so there are no cracks, edges or uneven surface finishes. The technique uses an electrolyte bath and a plasma mediated process to form a dielectric coating on a component. The light alloy part sits in a room temperature electrolyte bath and a high voltage is applied. This stimulated plasma discharges at the surface of the part which drives the conversion of the surface into a ceramic oxide layer.
This oxide layer’s thickness can be finely controlled, enabling resulting characteristics to be adapted for the precise application. Thickening the oxide layer increases the dielectric strength. Aluminium oxide, the main component of the PEO surface layer on an aluminium alloy, has dielectric strengths ranging from 14.6-16.7 kV/mm. Recent research has shown that aluminium components with PEO surface coatings that include silica additives have dielectric strengths of 59-79 kV/mm, far in excess of polypropylene.
Thanks to the versatility of the PEO process, where our material scientists design bespoke solutions for every project, specific coatings can be produced to meet required select thermal management qualities, whatever they may be. We have created coatings both for thermal transmission (0.8 – 10 W m-1 k-1) and thermal barrier (up to 900℃) applications.
Whatever the project, PEO offers a cost-effective, scalable solution for engineers looking to optimise the thermal conductivity of components, greatly improving the viability of light alloys across a wide range of applications.
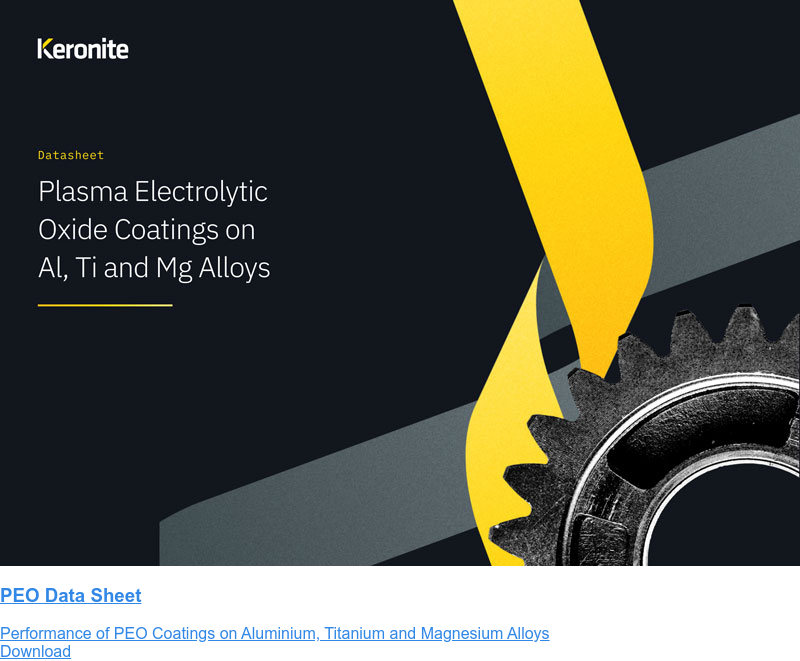
