How nanotechnology took over materials science
28 September 2022Once the realm of science fiction, nanotechnology underpins much of the technology we take for granted today. Without nanotechnology, the semiconductors in our electronics, lightweight aircraft, sports cars and even many modern drugs would not exist.
The roots of this branch of science and engineering lie with an iconic presentation by physicist Richard Feynman in 1959, There’s plenty of room at the bottom. In the presentation, he explained how matter could be manipulated at an atomic scale. Feynman’s work wasn’t recognised until 20 years later, but he is now credited as the ‘father’ of nanotechnology as we know it today.
According to the US National Nanotechnology Initiative, the definition of nanotechnology is “science, engineering and technology conducted at a nanoscale, which is about 1 to 100 nanometres (nm)”. To put that into context, a sheet of paper is 100,000nm thick.
To enable nanotechnology to be fully exploited, chemists needed specialised tools that simply didn’t exist at the time of Feynman’s presentation. The development of scanning probe microscopy technologies such as atomic force microscope (AFM, 1985), the scanning tunnelling microscope (STM, 1981) in the sixties enabled scientists to visualise nanoparticles. Fabrication technologies to make nanoparticles have since been developed, such as electron beam lithography, a technique used to make semiconductors.
So, nanoparticles are small. And nanotechnology offers so many opportunities and applications because when you get to that sort of size, atoms and molecules start behaving differently. But despite these changes occurring at nano-scale, they have the potential to bring about significant change.
Nanotechnology in materials science
The creation of innovative nanomaterials exploits these changes in behaviour when materials engineers start working at the nanoscale. Because the nanoparticles are small enough to confine their electrons, they experience quantum effects – the nanoparticle starts behaving with both wave and particle properties.
When the particles that make up a material are near or at atomic scale, the surface area to volume ratio is very high – they have a large surface area when compared to the volume.
Contrast this with a bulk material, such as a sheet or block of metal, which has a small surface area compared to its volume. A copper sheet or wire is soft and malleable. But copper nanoparticles at the 50mn scale perform very differently. The ductility and malleability characteristics are significantly different.
Why is this significant to materials scientists? The change in optical, physical and chemical performance characteristics at the nanoscale enables the material to be applied in new applications.
New materials applications emerging through nanotechnology
As one example, solar radiation is absorbed more effectively by a photovoltaic (PV) panel with silicon nanoparticles embedded. PV cells in a solar panel can lose light energy, and therefore efficiency, because light is reflected from the surface of the cells.
The nanostructures formed by the nanoparticles are by definition around 100mn or less. This structure can be tailored by scientists to reduce the reflectivity of the material. The result is the incoming solar radiation is guided into the cells that convert the photons into electricity with minimal reflection – thereby maximising efficiency.
Nanotechnology can also be applied to light alloys through surface coatings. Surface coatings can change the behaviour of a material by, for example, increasing its hardness or resistance to corrosion. There are nanocoatings, which apply coatings of a few hundred nm thick to a substrate. Depending on the coating, characteristics and properties such as corrosion resistance, self-cleaning, antibacterial and antiviral, anti-scratch, anti-fog, and even water repellency can be achieved.
Nanoparticles are also introduced into conventional coatings technologies. These are not nanocoatings as such but are surface coating technologies that incorporate nano-scale particles to alter the properties of the coating, thus creating new opportunities to add new characteristics to coatings.
How nanoparticles are used in surface coatings
Conversion coatings, like plasma electrolytic oxidation (PEO), are capable of using nanoparticles to generate performance benefits. The PEO technique involves an electrolyte bath and an applied voltage creates plasma discharges as the component oxidises. This produces a ceramic-like layer that effectively grows into the component. Like a nanocoating, PEO produces new characteristics that uniquely enhance the performance of the material.
There are two key features of PEO that make it particularly useful for materials engineers seeking to exploit the novel performance characteristics of nanoparticles. Firstly, the ceramic-like coating is multi-layered, and the top layer is porous, meaning that additives can be ‘salted’ into the coating.
Secondly, the composition of the electrolyte bath can be tailored so that materials engineers can finely control the qualities introduced by the coating. By ‘doping’ the electrolyte bath with certain nanoparticles, the final coating will incorporate these particles. Put these together, and PEO can be used to salt the resulting surface coating with nanoparticles that introduce new and exciting performance characteristics.
Salting the electrolyte with nanoparticles of titanium dioxide and other additives turns the coating into a photocatalyst. The photocatalytic effect is to create peroxides from moisture in the air which in turn kill microorganisms. The PEO with nanoparticles becomes an antimicrobial coating.
This is just one instance where salting a surface coating with a porous layer like PEO with nanoparticles produced a beneficial effect. PEO can be used to introduce many other nanoparticles into the porous layer that result in other useful performance characteristics.
To learn more about PEO, download our white paper ‘What is Plasma Electrolytic Oxidation?’ or get in touch with one of our materials scientists today.
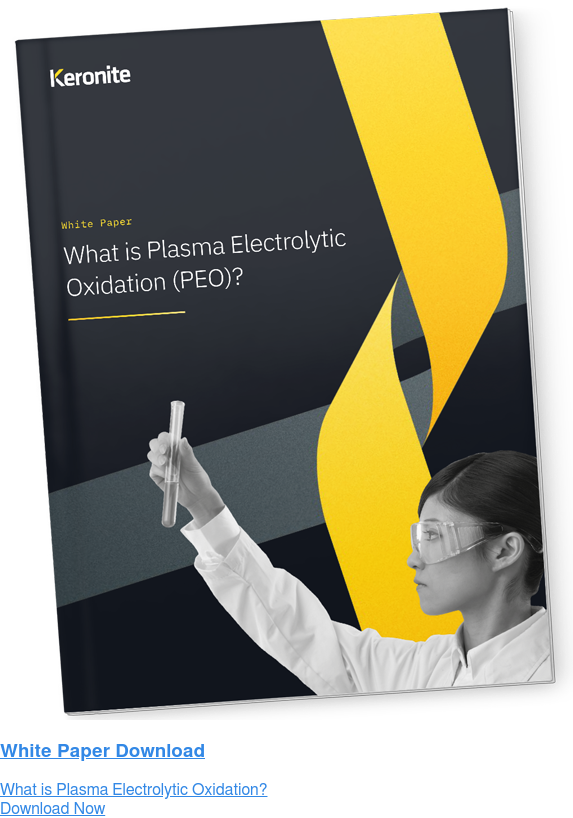
