How Keronite protects specialist aluminium equipment from subsea corrosion
25 June 2021In sub-sea environments, protecting light alloys against corrosion, while retaining their functionality, is absolutely critical. For this reason, steel is still the most widely used material that fabricates large vessels. Yet, for many reasons, specialised components and equipment are increasingly created using alloys of aluminium, titanium and magnesium.
Across the marine industry, steel is predominantly used for fabricating large vessels. However, specialised parts and equipment are often made from light metals such as aluminium, titanium and magnesium alloys. These metals are lightweight and often more suitable for specific applications, particularly where speed and efficiency are key. Keronite have designed a duplex coating system for light alloys which protects light metal components from corrosion for decades at a time.
Keronite have recently collaborated with a manufacturer of specialised equipment for marine vessels. In the harsh subsea environment, corrosion poses a significant threat to machinery and equipment. The project brief required a coating system for light metal alloys which could withstand being submerged in seawater for prolonged periods of time.
Although many ships and sea-faring vessels are made from steel, light metal alloys are often used to fabricate specialist components. In the case of the sonar and radar detection systems often used by marine vessels, these need to be housed in protective casing. This housing can be made from titanium, which is pliable and has a high strength-to-weight ratio. Aluminium and magnesium can also be used.
Light metals are prone to corrosion, and the salt and oxygen concentration in seawater can accelerate this process. The project needed a coating that could protect the metal housing for sonar equipment for up to 20 years in a subsea environment.
An additional challenge was the size and complexity of the components. The housing for side or hull-mounted sonar equipment can have a surface area up to 300 dm2. Relatively large light-metal components needed a high-performance coating to protect them from corrosion and increase their lifespan.
PEO coating for large and complex components
One of the key features of plasma electrolytic oxidation (PEO) is the flexibility of the application process. The metal component is placed into an electrolyte bath which is modified for anticorrosive properties. A current is passed through the metal (200V or higher) and a ceramic coating layer forms on the metal’s surface. This creates a uniform coating across the surface of the metal that is resistant to through-cracking, even on complex shapes and structures. Keronite’s industrial-scale equipment includes electrolyte tanks up to 3500 litres, which can be used to process large components.
An additional requirement for this project was to protect specific machined and threaded surfaces, which did not need anticorrosive treatment. Keronite’s in-house engineers designed the fixtures needed to mask these features during the PEO application process. These remained in place while a secondary sealer was applied.
Corrosion resistant duplex coatings
Due to the extreme conditions of the subsea environment, a PEO coating with an additional epoxy polymer sealer was recommended for this project.
To protect against corrosion, a PEO coating creates a passive ceramic layer between the metal alloy and the coating. An additional benefit to this coating is improved wear resistance (500-1100 HV), useful against mishandling and transport damage.
Corrosion-resistant coatings often fail due to through-cracking or at welds. Using PEO methods, the coating “grows” on the surface of the metal. This leads to excellent coating coverage and reduces the risk of through-thickness cracking, particularly at welds or bends. The precise nature of the PEO application process means that the coating thickness and surface roughness can be tightly controlled. For this application, a uniform thickness of 10 – 20 microns was required before a sealer was applied.
The PEO coating is formed in situ, so it experiences very good adhesion to the metal surface. The outer surface of the coating is porous and can be modified to promote adhesion to the secondary coating or sealer. For this particular project, Keronite’s materials scientists achieved a closed-cell architecture with approximately 1-3 micron diameter. When measured, the average surface roughness of the PEO coating was 1-1.5 microns Ra. This provided an excellent surface for bonding to various types of sealers or primer/paint combinations. The ceramic PEO coating combined with an organic topcoat provides excellent corrosion resistance to the underlying metal.
At Keronite’s development laboratories, a range of performance testing is carried out on all anti-corrosive coatings. Samples of metal alloys coated with the PEO/sealer duplex coating system were tested using salt spray tests (ASTM B117) and seawater immersion tests. These are accelerated tests that allow scientists to evaluate a coating’s anticorrosive performance. Using the salt spray testing, these coatings passed after 28 days (5% salt spray) in highly corrosive conditions. Seawater immersion tests also showed excellent results after 42 days. These results indicate that the coating system has an expected lifespan of 15-20 years.
Laboratory-based testing shows that the PEO coating combined with an additional sealer meets the customer requirements set in the project brief. The coating system will now be applied to sonar housing components at Keronite’s large-scale facility.
This product development project demonstrates how PEO coatings can be adapted to meet specific customer requirements. It has a range of promising applications for corrosion protection of light metals in the marine and defence sectors. To learn more about PEO, download our whitepaper “What is Plasma Electrolytic Oxidation?” or get in touch with our expert team of materials scientists today.
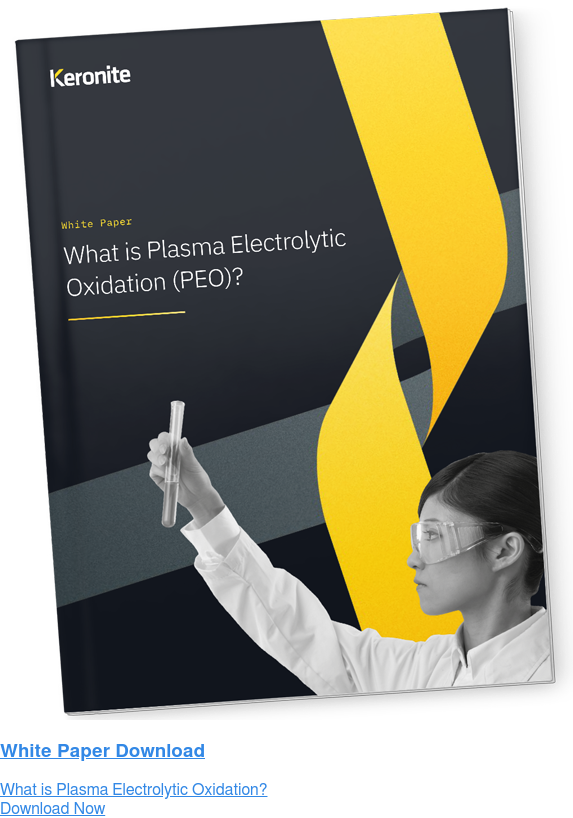
