How Keronite enables sustainable low/no carbon manufacturing
6 December 2022The environmental impact of carbon emissions is becoming an increasingly important issue, with many government and regulatory bodies placing net zero goals in the coming decades. Light metals and alloys play a significant role in reducing these emissions by improving fuel and energy efficiency as well as circularity. However, their integration is difficult due to their susceptibility to corrosion, wear and other elements.
As a solution, material science and advanced coatings must be considered alongside sustainability to provide resistant components that are environmentally friendly. Keronite and the advanced PEO process provides for all these factors as a green coating technology for the future.
What is low/no carbon manufacturing?
Low/no carbon refers to the global movement to reduce carbon emissions, with zero pertaining to a balance of the amount that is produced and removed from the atmosphere. This movement is a result of the Earth’s climate slowly warming as a consequence of emissions and greenhouse gases. Global warming then leads to extreme weather, food supply disruptions and increased wildfires amongst many more negative impacts to the environment.
In recent decades, government bodies have been recognising the importance of reducing carbon emissions, with the goal of eventually reaching net zero. The EU 1998 ACEA agreement was an initial step emission compliance which limited the amount of CO2 emissions that could be produced by passenger cars. The UK was the first government body to pass a net zero emissions law, dictating that all greenhouse gas emissions in the country will be net zero by 2050.
Why is material science important in achieving low/no carbon?
Material science is now a crucial part of achieving low carbon emissions. Innovations are surfacing high-potential opportunities to integrate repairable, circular and long-lasting materials such as aluminium into usable components; they are also lightweight, and thus greatly increase energy efficiency. Simply put, considering the performance of materials past their first-intended application is now a crucial part of moving towards a sustainable future.
Engineers are also considering how materials are extracted and smelted, as it accounts for a significant amount of global carbon emissions. Moreover, these engineers need to factor in how components and materials are reused and remanufactured in order to minimise the environmental impact of the process.
This requires a holistic, multi-faceted approach to materials selection – one that considers not only mechanical performance and fabrication, but repaired, serviced and prepared for end-of-life. Plasma Electrolytic Oxidation (PEO) takes all these factors into account and provides sufficient protection for components through a green process that enables circularity.
What are the benefits of PEO over other alternatives?
Clean
Many forms of surface coatings present complications when it comes to environmental impact and recyclability. The irreversible nature of certain spray coatings make recycling almost impossible, and anodising creates harmful byproducts that can damage plants and wildlife.
PEO is free of organic compounds, VOC or strong acids during the process. It uses 99% distilled water and creates no toxic waste products, making it perfectly safe to dispose of normally without any impact whatsoever. Also, PEO’s surface coating is imparted by changes to the substrate itself, allowing the metal to be fully recycled at the end of the component’s life cycle.
Reliable
Many metal coating technologies have individual drawbacks that make them unreliable in certain situations; Anodising has difficulty creating a consistent coating on complex geometries, and paint coatings lack the hardness to provide sufficient wear and abrasive resistance.
PEO provides consistent results and properties for components of all shapes, sizes and applications. It forms coatings with higher hardness, chemical passivity and structure that creates high strain tolerance and stronger adhesion.
Customisable
The outer ceramic layer formed by PEO is porous, enabling engineers to introduce various sealants during the process. These sealants each provide different characteristics depending on the component and application; one may provide extreme thermal protection whereas another boosts stiffness. This customizability allows designers to incorporate unique characteristics to their components that are required to adopt light metals and alloys into their application.
Achieving low/no carbon with Keronite
Regardless of your industry, achieving low carbon emissions is a shared goal and responsibility. By incorporating advanced material science that takes all factors into account, you can greatly improve efficiency, circularity and carbon emissions.
Keronite’s unique PEO process is a clean solution that allows engineers to choose high-strength, low-weight light alloys over heavier options like steel. Our materials scientists will work directly with you to create bespoke coatings that suit the specific needs of your application through a green and clean process.
If you are involved with a project that concerns reducing carbon emissions or extending the lifespan of your manufacturing components, get in touch with our technical team or download our white paper for more detail.
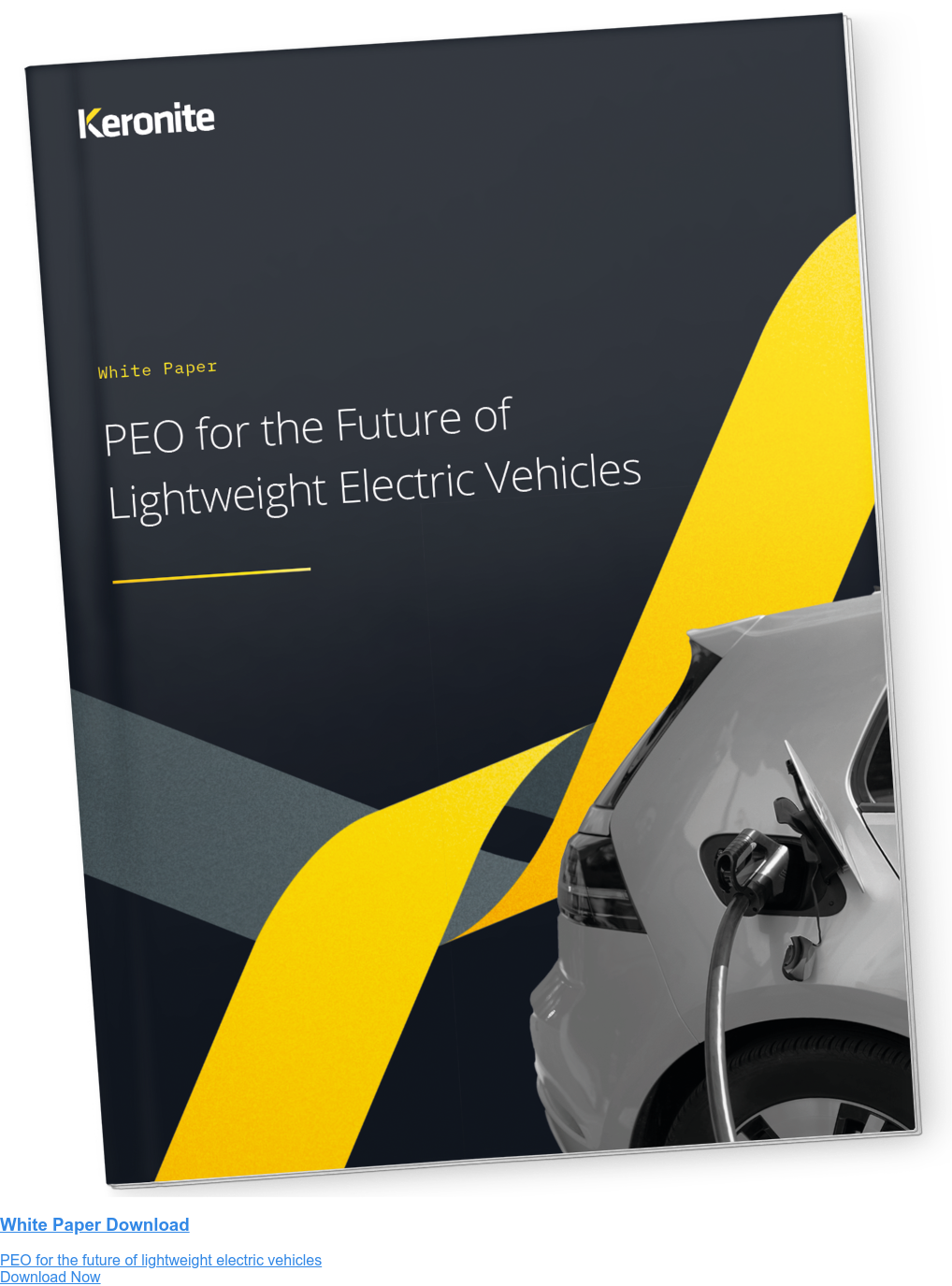
