How corrosion resistant surface coatings enable wider magnesium alloy applications
5 January 2021The drive for higher performance, lower energy consumption and longer operating lives means engineers and materials scientists are constantly seeking alternative materials with unique characteristics.
Magnesium is the obvious choice for many high-performance applications. Depending on the exact specification, magnesium alloy components can be as much as 50-70% lighter than stainless and high strength steels. It is even 15-30% lighter than aluminium.
However, even considering its benefits as a lightweight high strength to weight ratio, magnesium alloys have characteristics that are less desirable in many high-performance applications. These include lower ductility and creep resistance, less rigidity and it is chemically active and soft, so rapidly corrodes and wears rapidly in demanding environments.
For example, as the most reactive and anodic metal in its electrochemical series of the periodic table, when in situ with other metals, uncoated magnesium and magnesium alloys suffer from serious galvanic corrosion. Fortunately, there is a technology solution that, despite their weaknesses, enables magnesium alloys to be used in much wider applications where corrosion and wear are features of the operating environment.
Using the surface coating technology plasma electrolytic oxidation (PEO), magnesium alloys become corrosion and wear resistant in the most demanding operating environments. As a result, engineers and materials scientists can specify and benefit from magnesium alloys they would be unable to use without PEO.
What are typical magnesium alloy applications?
Magnesium alloys are used in a surprisingly wide range of applications, many of them high-performance and in demanding operating environments. The use of lightweight magnesium components can often underpin the application. For example, the lower weight offered by the magnesium component enables fighter jets and Formula 1 racing cars to achieve levels of performance that would not be possible if using aluminium or steel.
The threat of corrosion and wear
Aerospace, motor racing, automotive, oil and gas, industrial, sports – all these applications have different types of demanding operating environments.
In automotive and motorsports, there is the constant threat of corrosion from road salts and slurries, and salt spray and highly concentrated de-icers in aerospace. For example, these particular threats can cause galvanic corrosion resulting from an accumulation of corrosive salt liquids and debris around the fasteners fixing uncoated magnesium alloy components to the aircraft or vehicle.
Corrosive saline solutions in the form of seawater pose a constant corrosion threat to magnesium alloys. Most aircraft, many vehicles and industrial, oil and gas and energy applications face seawater corrosion. Magnesium alloys suffer from all main forms of corrosion, including uniform corrosion, galvanic corrosion, pitting and stress corrosion.
This could potentially severely limit magnesium alloy use in most applications, and in the automotive sector use has been traditionally restricted to components that will not suffer wear and corrosion, or are protected, such as engine blocks, seat parts and internal cosmetic features. And even many magnesium engine blocks have had internal aluminium liners to protect from hot corrosive lubricating oils.
Engineers can specify PEO coated magnesium alloys with confidence
There are dozens of magnesium alloys that have been formulated to have specific characteristics for use in specific applications. But a high strength or high temperature resistant alloy may lack corrosion resistance.
An advanced surface coating specially developed for lightweight magnesium components and that can be carefully tailored according to the application can be added. This enables the component with specific intrinsic properties, such as temperature resistance, to be used in corrosive environments, such as an aerospace, defence, oil and gas and automotive application.
PEO uses a unique combination of an electrolyte bath and plasma over three distinct stages to form a ceramic-like duplex coating on magnesium alloys. Keronite’s G3Mag PEO coating was applied to a test strip of ZE41A alloy. It underwent a six-hour salt spray test using 5% sodium chloride (NaCl) at 80 degrees centigrade. The result is shown in figure 1 – no corrosion.
Figure 1. Salt corrosion test of 5 micrometres G3Mag coating on ZE41A alloy.
One major significance of PEO’s duplex layers is that the outer layer is porous, a result of the plasma discharges during the coating process. This porous layer can be ‘seeded’ with other substances by including them in the electrolyte bath. The whole process can be carefully controlled to change the coating thickness and composition according to the target application requirements.
Keronite’s PEO surface coating G3Mag-C is an example. The coating prevents crevice corrosion by creating a stabilised layer at the interface between the ceramic and underlying alloy. This layer inhibits corrosion at sites adjacent to intermetallic particles in the underlying alloy by limiting localised pH swings, essentially forming a localised passivation effect for those sites. Pinhole corrosion, caused when solvents in surface sealers evaporate forming pinholes as the vapour escapes, is prevented because an oxidatively stable ceramic layer is formed at the base of the pinholes.
Figure 2 shows the impact of ZE41A alloys undergoing salt fog tests over 20, 92 and 164 hours. When a fluoropolymer sealer blend is seeded into the porous outer layer, even magnesium alloys containing highly reactive lithium, used in the fracking industry, can improve corrosion resistance.
Figure 2. Salt fog tests of G3Mag-C PEO coating versus G2Mag.
For more insight into the performance potential of magnesium with plasma electrolytic oxide coatings download the full white paper, written by Keronite’s chief technology officer, Robin Francis. Click below to download the full white paper now.
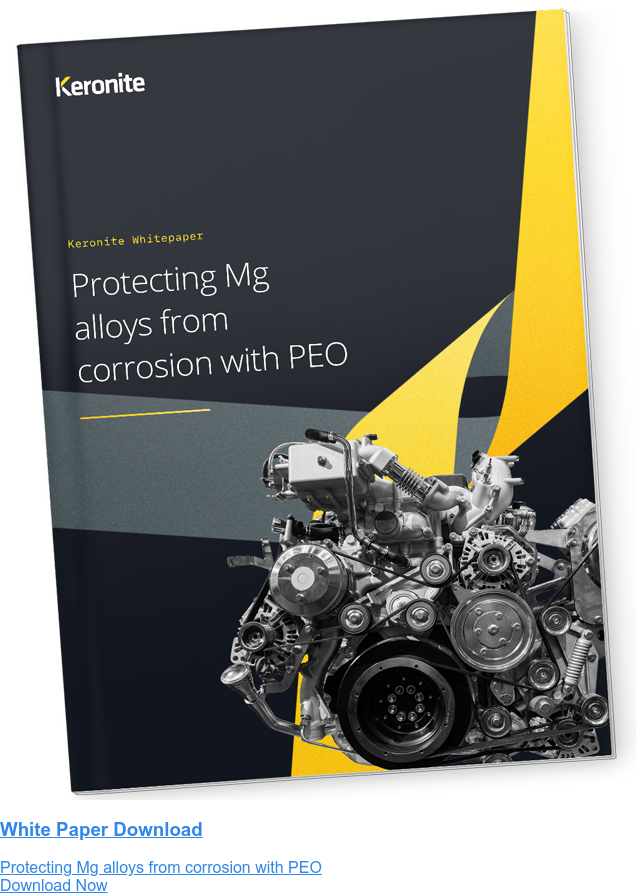
