Extending the life of light alloys: why bespoke coatings are key
11 August 2022With the help of bespoke coatings, designers can implement light alloys that facilitate lighter, stronger and longer lasting components. Where light alloys are naturally susceptible to corrosion, temperature and wear in certain environments and applications, the right coating can make the implementation of these alloys long-lasting and better performing.
Plasma Electrolytic Oxidation (PEO) is a world leading bespoke coating technology that provides engineers with full control over the resulting coating characteristics, ranging from better thermal protection to stronger wear resistance. PEO fully enables designers to implement light alloys into their designs, but what are the specific challenges faced when using light alloys and how does PEO overcome them?
What are the challenges that come with light alloys?
Magnesium
Magnesium has an extremely low density whilst also being fairly strong and stiff due to its hexagonal and close-packed crystalline structure. These features alone can make it attractive in certain applications where saving weight is crucial, and is used in gearboxes and steering wheels within the automotive industry.
The challenges magnesium alloys face are that they’re highly susceptible to corrosion, even in ambient conditions. The electron structure of its outer layer makes it highly reactive to oxygen, resulting in the corrosion of the outer layer of the alloy and exposing the metal underneath to attack. Magnesium alloys require bespoke coatings that provide corrosion specific resistance in order to be sustainability implemented into designs.
Aluminium
Aluminium alloys present a range of benefits for manufacturing designers and is already one of the most popular light alloys for designers. Its great strength-to-weight ratio, ductility and stiffness make it widely used in automotive and aerospace applications, whilst also being highly sustainable and widely recycled. Aluminium is much better for structural applications when compared to magnesium alloys, and is more suitable to replace steel.
That said, aluminium alloys are weak to factors such as corrosion and temperature, but particularly to wear. Dry sliding wear dramatically shortens the lifespan of components made of aluminium alloys. These components require a bespoke coating that provides sufficient substrate adhesion to prolong their lifespan.
Titanium
Titanium is one of the strongest light alloys available to engineers. It has features of high strength, moderate weight, decent corrosion resistance, and the ability to retain their mechanical properties at high temperatures. These features alone make titanium an attractive choice for intensive applications.
Unfortunately, titanium alloys are notorious for cracking and fatigue related issues. Whilst titanium has the strength and toughness to support up to 31900 psi, long-term fatigue causes cracks in the surface of the alloy, which in turn reduces the lifespan of components by creating stress raisers. Titanium alloys need bespoke coatings that provide sufficient fatigue performance through consistent and precise coverage around the substrate.
Bespoke coatings and PEO
Bespoke coatings are invaluable for engineers that wish to take advantage of a specific light alloy and successfully implement it into their application. As mentioned above, each light alloy has varying beneficial properties and degrees of resistance; Where an aluminium alloy may provide benefits for an automotive component, its weak wear resistance may make it difficult to realistically implement into a design. Bespoke coatings take the application requirements from the designer and implement the right form of coating to prolong the lifespan of components in that specific field.
Plasma Electrolytic Oxidation (PEO) is a bespoke metal coating technology for light alloys. It uses an electrolyte bath and high voltage to create plasma discharges on a substrate’s surface, producing multiple ceramic outer layers. These layers are porous, allowing reagents to be introduced that provide specific performance characteristics such as greater hardness, temperature protection or corrosion resistance. The customisability and degree of protection that PEO offers makes it the leading form of bespoke coating to extend the lifespan of light alloy based components.
Alternative forms of coatings, such as with thermal spray coatings, fail to offer the same level of optimisation and reliability that PEO offers. Thermal spray coatings involve superheating specific particles to then spray onto the substrate. The components used in the spray can include a mixture of alloys, ceramics and plastics to customise the coating, allowing for bespoke coatings. However, thermal spray coatings produce inconsistent results across components with complex geometries, whereas PEO produces a consistent coating across all designs.
Extending the life of light alloys with Keronite
PEO presents the ability for engineers to sustainably implement light alloys into their designs, enjoying the various beneficial properties they can bring. PEO also offers a level of customisability with the coating, allowing a range of engineers to use the technology to their advantage to prolong component lifespan.
Keronite is the world leader in PEO technology, uniquely improving the performance of magnesium, aluminium and titanium alloys. Our approach is highly collaborative; we work directly with your team to create bespoke PEO solutions that provide specific enhancements in ways no off-the-shelf coating technologies can. Our experience in PEO coupled with the expertise of our materials scientists and engineers allow us to adapt our coating solution to your specific problems.
To find out more about the PEO process and its impact on the lifespan of light alloy based components, read our full whitepaper below.
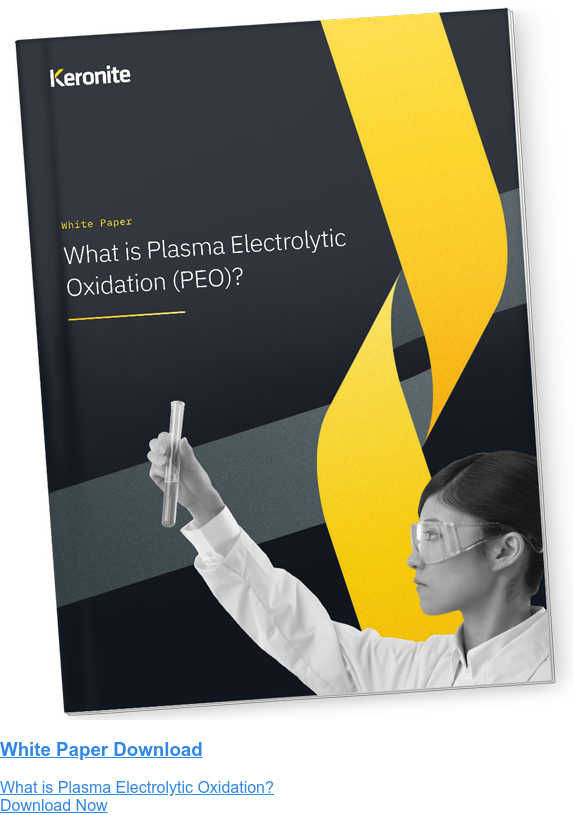
