Surface coatings for magnesium in defence: enhancing performance
6 July 2020Magnesium is still playing a critical role in the global defence industry, as it has done since the 1940s. New research and technologies are highlighting new ways to enhance the performance of this material – even as composite materials become more prevalent.
Defence agencies ask a lot of their materials. Materials need to withstand wear, corrosion, friction and a number of other materials challenges, all while being lightweight and inexpensive. Magnesium fits the bill remarkably well.
New science continues to shine a light on the potential of magnesium – bringing new benefits and properties to the alloys. In this article, we take a look at why this is the case, and what these new opportunities look like.
The benefits of magnesium alloys in defence
As one of the world’s lightest structural metals, magnesium alloys bring a number of benefits, including its density. Magnesium is less dense than other structural metals, like aluminium or steel. This enables magnesium to be used as a direct replacement for aluminium or steel, while offering significant weight savings.
The second enticing proposition is cost. Magnesium is the 8th most abundant element in the Earth’s crust. Due to the availability of supply (and the economies of scale emerging from its demand), magnesium is less expensive than alternative materials. While there has been a long period of decline in defence spending globally, a recent surge in demand makes now a prescient time to examine new opportunities with materials.
Thirdly, new findings in materials science and technology are more able than ever to boost the performance of magnesium alloys. Alloys such as AZ31b or AZ80 are readily replacing aluminium alloys and steels, which are heavier and suffer from a shorter lifespan than a Z-series alloy with an advanced coating.
Magnesium is not yet the panacea to all materials challenges in the sector. There is still a long way to go in terms of developing alloys and coatings that offer even better performance. What we do know, however, is that magnesium is being used in surprising ways – where wear, corrosion, high temperatures and ballistic resistance would have historically prevented its use.
Enhancing the performance of magnesium alloys
Performance in these applications are critical; there is no room for compromise, Mg alloys need to be:
- Corrosion-resistant. Magnesium is highly reactive, for three reasons: the synergic effect of its negative standard potential, the presence of impurities and the passive protective film it creates. Magnesium only naturally resists corrosion in alkaline environments.
- Lightweight. AZ80 has a dentistry of just 1.80 g/cm3, while AZ31B has a density of 1.77 g/cm3
- Wear-resistant. Magnesium alloys, even when protected by some surface coating techniques, cannot meet the requirements of the defence industry with regards to wear.
- Friction and dry-sliding wear resistance.
- Shockproof. Magnesium alloys can absorb the shock of ballistics, to a degree determined by the outer surface coating.
AZ31B Performance (source)
Magnesium alloys in defence: applications and considerations
Aerospace and aeronautics
Magnesium alloys are often found in structural applications, such as large-cast aeroplanes components and spacecraft parts. The weight savings offered by magnesium can reduce the mass of parts by as much as 50%, boosting fuel efficiency and performance.
Lightweight military systems
Despite huge advances in electronics and wireless communications technology, infantry in the US military now carry heavier equipment around with them than ever before. Official documents state that U.S. soldiers may carry up to 100 lbs (45.5 kilograms) worth as standard, if not more. The variety and bulk of necessary equipment (from batteries to power equipment, to armour and helmets, to other kinds of hardware) has increased dramatically. Lightweight materials could offer remarkable weight savings.
Lightweight powertrains
The bulk of the weight in any land vehicle is in the engine. In the defence industry, machines are built with enormous cargo loads, to make them fit and proper for their designed application. There are a whole host of potential benefits to using magnesium in powertrains – including the increase in fuel efficiency, range, durability and maintenance cost reduction.
Choosing a surface coating for magnesium components in defence
There is no shortage of options available for protecting magnesium alloys. Researchers and materials scientists at Keronite are fully accustomed with the range of surface coating options available to enhance the performance of magnesium alloys – from sol-gel techniques to the company’s proprietary plasma electrolytic oxidation (PEO) technology.
Keronite is already working in partnership with leading defence manufacturers to find superior solutions for their materials. Our in-house scientists are examining methods to boost the corrosion resistance of magnesium alloys, as well as closely examining other areas of tribological concern.
To learn more about the work Keronite does, or to get in touch with our scientists to discuss the most appropriate coating for your project, then get in touch.
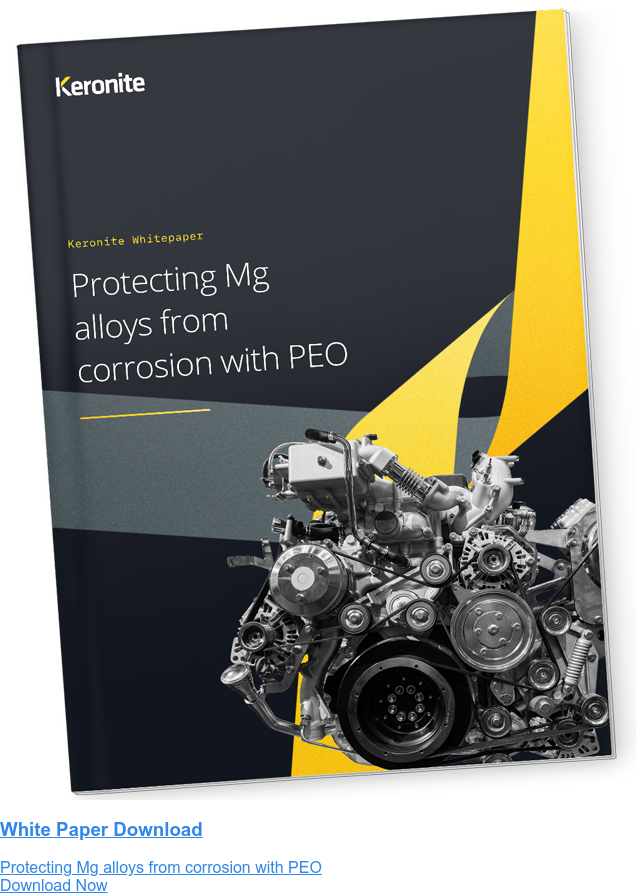
