Could surface technologies offer relief to the semiconductor manufacturing industry?
16 August 2021The electronics industry is failing to cope with a global shortage of semiconductors. Due to the COVID-19 pandemic, subsequent regional lockdowns and other restrictions, global distribution networks have experienced significant disruption. At the height of the crisis, chip delivery times extended beyond 20 weeks. This, combined with the ever-growing demand for smaller, faster chips, has left the industry looking to ensure a more robust supply chain and more reliable manufacturing processes.
Semiconductors are required for almost every electronic device manufactured today. As electronics and ‘smart’ capabilities are added to more everyday items, the overall demand for semiconductors has drastically grown. This demand has shown few signs of slowing, in fact, devices now require even more computing power and capacity, pushing demand up further. But as the last 12 months have demonstrated, all and any efforts to improve the reliability of supply can be a major competitive advantage for manufacturers.
Semiconductor fabrication is a niche market, dominated by a few key players thanks to high costs associated with the production process and research and development (R&D) expenses. Leading manufacturers such as Intel, Samsung and TSMC have publicly stated their intention to resolve supply chain issues by improving manufacturing process efficiency and overall product quality. The current supply chain issues are expected to have significant effects on the industry for a number of years.
High-precision semiconductor processing
The semiconductor manufacturing process is extremely complex and precise. It involves a large number of steps that must be carried out with a high degree of accuracy. The process is so precise that it requires the majority of steps to be carried out in cleanrooms to avoid contamination and defects. Equipment used to manufacture these devices must be maintained to the highest standards to ensure the quality and yield of the end products. This equipment must also be able to withstand the highly gaseous, corrosive environments in which semiconductors are manufactured.
Semiconductors are typically made from crystalline solids such as silicone. Their pure crystalline structure must be completely free of imperfections for the tiny device to function correctly. Pure silicon crystals are sliced into wafers, which are oxidised to create patterns on the surface. The semiconductor is then etched using Freon plasma. Finally, the silicon wafer is heated to over 1000 °C and “doped” with impure atoms. Once cooled, the semiconductor is ready to be integrated into a circuit. It will go on to form the microprocessors used in a wide range of electronics, from laptops to remote controls.
The semiconductor manufacturing process involves extremes of temperature and pressure. It must also be carried out at speed to produce the number of semiconductors required from a commercial perspective. For manufacturing equipment, this presents a number of potential issues that could radically reduce the longevity of the equipment, i.e. its useful life.
Protecting semiconductor manufacturing equipment investment
Machinery and tools used in the semiconductor industry are typically made from aluminium and stainless steel, as they’re strong and malleable. These metals must be coated to protect the processing equipment from the harsh environments required to produce semiconductors. The number of steps required for semiconductor manufacturing, and the complexity of the equipment, means that maintaining machinery to maximise equipment lifespan is key to success. Maintenance and repairs mean costly downtime and expensive replacements. Therefore, coating properties must be tailored to achieve excellent thermal, chemical (such as plasma gases) and abrasion resistance, as well as corrosion protection.
In addition to this, the internal surfaces of manufacturing equipment must be as clean and smooth as possible. Porous surfaces will hold contaminants that could be transferred to the semiconductor, causing disruption to the crystalline structure and its finely tuned electrical properties. Using surface coatings that have an extremely low friction coefficient and low surface roughness will minimise the risk of contamination and reduce the need for downtime and cleaning. This has huge commercial implications, as a high-performing surface coating will improve yield and reduce downtime costs.
Coatings for semiconductor manufacturing equipment can be traditional powder coatings, thermal spray coatings or even organic fluoropolymers. Ceramic coatings are also suitable for high heat, chemical, and abrasion resistance. Using ceramic plasma electrolytic oxide (PEO) coatings to protect manufacturing equipment can provide an effective solution to abrasive wear, corrosion, and contamination issues.
Plasma electrolytic oxidation for semiconductor manufacturing equipment
PEO coatings can be applied to intricate components by immersing them in an electrolyte bath and passing a voltage through the metal. The composition of the electrolyte bath will influence the properties of the resulting coating. Using different additives and voltage sequences, the film thickness and surface properties can be adapted to suit a wide range of applications.
For more information about how PEO can be used to coat aluminium or light metal machinery components, get in touch with Keronite’s expert team of materials scientists. They can discuss your project requirements and tailor a coating solution that can meet the demands of operating machinery under harsh conditions.
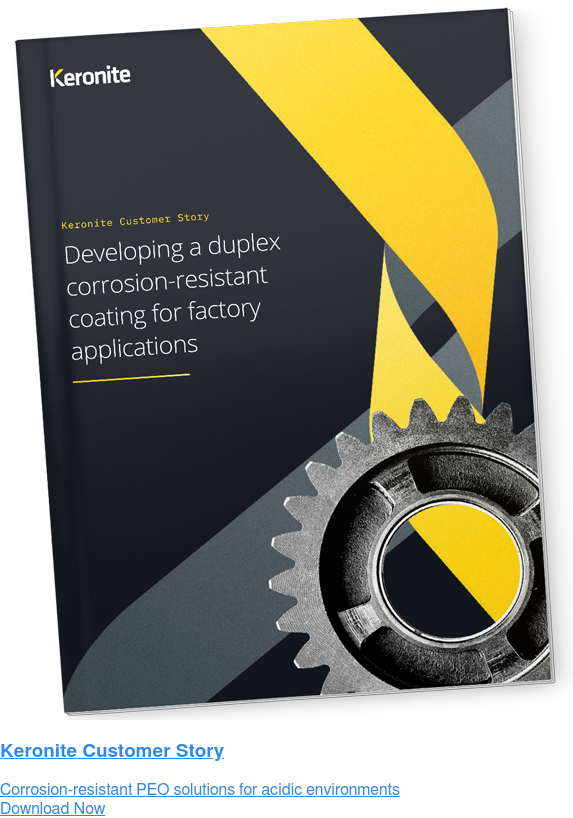
