Comparing the environmental credentials of surface coatings
18 May 2021For fast growing supply chains, such as those serving the aerospace, energy, defence and automotive markets, there is an increasing requirement for manufacturing components which are lightweight and durable.
When it comes to lightweighting in components and sub-assemblies, light metals and their alloys, such as magnesium, aluminium and titanium, are ideal material choices for many applications.
The downside to these light metals is their low wear resistance and susceptibility to corrosion, particularly in performance-focused applications. The answer to this challenge is anti-corrosion and wear resistant coatings such as:
- Hard anodizing
- Chrome plating techniques
- Plasma spray techniques
- Plasma electrolytic oxidation (PEO) A.K.A micro-arc oxidation
These coatings and surface treatments have been scrutinised for their use of toxic and harmful chemicals. Recent legislation, such as RoHS, REACH and their international equivalents, are encouraging manufacturers to boost their green credentials. This includes the use and disposal of waste and end of life products, moving the use of pollutants in anti-corrosion treatments higher up the specification agenda.
The use of toxic chemicals in creation of anti-corrosion coatings and surface treatments
There are a number of important considerations when selecting an anti-corrosion coating or surface treatment, including performance, cost and final application. However, the environmental impact has been slowly rising up the agenda for materials engineers.
In recent years, the green credentials of anti-corrosion coatings have been highlighted in a range of research studies designed to educate engineers on the high-hazard chemicals used in these processes. These studies have sought to find at-least equivalent performing coatings that have a limited impact on the environment.
Commercial sectors such as aerospace and automotive are now taking responsibility for the reuse, recycling and end of life disposal of their products and components. Choosing light metals that have been coated or treated using solutions with the lowest environmental impact, makes total cost of ownership and end of life material management easier and more cost effective. It also provides a unique source of added value as the industries seek to become more environmentally conscious.
Out of the four anti-corrosion coatings listed below, some use strong acids and others use heavy metals such as cobalt, nickel and chromium, which can all involve high-hazard chemicals. There are stringent regulations to control the use, transportation and disposal of these chemicals. Health and safety risks are also an important concern.
Hard anodising
Hard anodising (HA) is an electrochemical process that converts a metal surface into a corrosion-resistant anodic oxide finish. It is achieved by immersing the metal into an acid electrolyte bath and passing an electric current through the medium.
There are two by-products of anodising with a sulfuric acid bath: degraded sulfuric acid and aluminium hydroxide. The latter is classified by regulatory bodies such as the United States Environmental Protection Agency (EPA) as a hazardous wastewater and cannot be rejected into a municipal wastewater system.
The EPA also has strict standards for by-product disposal. This includes a maximum allowable aluminium concentration level and guidance on neutralising sulfuric acid to a pH of between six and eight before disposal can take place.
Disposal aside, there are further pollutants to consider during the anodising process. Pollutants in the form of sulfuric acid fumes are released from the bath that pollute the air and with extended exposure are harmful to employees working in the plant.
Chrome plating
Chrome plating techniques involve the application of a thin layer of chromium to a metal or metal alloy substrate, using electroplating.
Electroplating is the process of passing an electric current between two electrodes immersed in a chromic acid electrolytic bath, with one of the electrodes being the substrate to be plated. While the electricity is flowing, chromium atoms are deposited in a layer across the surface of the metal, to be plated in the next step of the process.
Traditional chrome plating processes rely on the use of chemicals which are designated as carcinogenic. The use and disposal of these chemicals are therefore highly regulated by regulatory authorities, such as the UK’s Health and Safety Executive (HSE).
According to the Surface Engineering Association, there are two common types of plating process for chrome. Hexavalent chromium is the most toxic and is a known human carcinogen. The plating bath used in this process will produce toxic waste as a by-product of the hexavalent chromium and must be treated before disposal.
Trivalent chromium offers a less toxic alternative, but its use and the disposal of its waste materials are still strictly controlled.
Plasma spray
Considered a mature and widely used technology, plasma spray applies a thick coating (up to a few millimetres in thickness) onto a substrate by injecting a powder into a high temperature plasma jet, formed by electrical to thermal energy released in a plasma torch.
Whether conducted manually or automatically, spray technologies expose workers to several potential and real risks, primarily respiratory issues as a result of breathing in harmful feedstock chemicals.
In one study, workplace exposure and release of ultrafine particles during atmospheric plasma spraying in the ceramic industry, it was identified that both ultrafine and nano airborne particles travelled from the emission source inside the spray chamber, out into the worker breathing zone. Further investigation also detected environmental release of ultrafine particles outside the exhaust tube and the release of engineered nanoparticles (ENP) into workplace air.
Plasma Electrolytic Oxidation
Plasma Electrolytic Oxidation (PEO), or micro-arc oxidation (MAO) as it is also known, produces multiple ceramic-like layers on the surface of light metals, valve metals and their alloys. The duplex coating formed by this unique technology has a porous outer layer. This allows materials scientists and engineers to impregnate different reagents to customise the performance characteristics of the coating.
PEO uses an electrolyte bath of proprietary dilute aqueous solution and a high voltage current of 200v or higher. When the current is passed through the electrolyte, the high potentials generate plasma discharges onto the substrate’s surface.
In turn, the plasma provides the ideal pressure and high temperature conditions to form a mainly crystalline oxide from the light metal substrate. The electrolytic bath is typically a low concentration, chemically benign, aqueous solution, meaning process waste streams can be discharged directly to municipal drains after a slight pH adjustment.
More industries are becoming accountable for the disposal of their by-products, and the increasing need for lighter engineering materials shows no sign of slowing. More sustainable and lower impact anti-corrosion surface coatings and treatments will play a major role in meeting these needs.
To learn more about PEO, download the What is PEO whitepaper or get in touch with our team of material scientists to learn more about the environmental and performance credentials of PEO today.
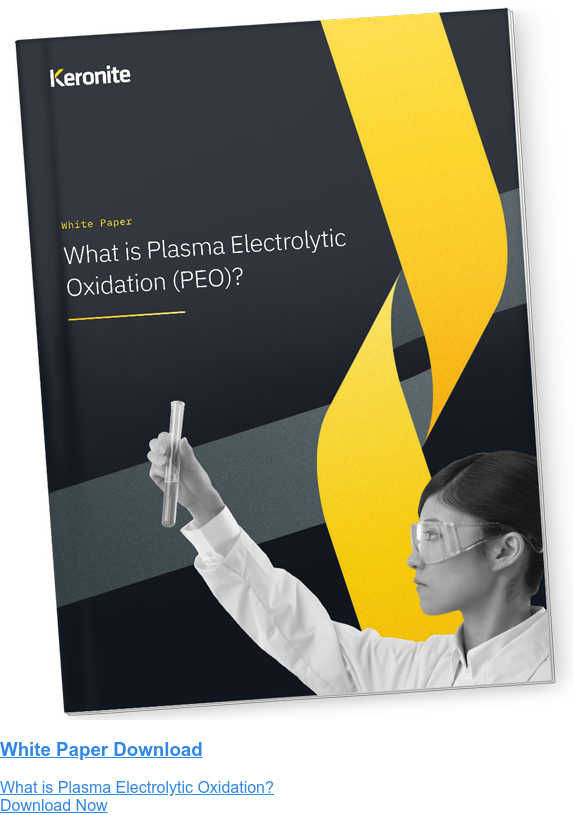
