Alternatives to white chromate conversion coatings
15 August 2023Chromate conversion coatings have been used in aerospace and other industries throughout the 20th century. They offer impressive corrosive protection, and provide enhanced surface adhesion for paint coats to reliably be applied.
In the 21st century, however, the challenges of utilising chromate conversion coatings has become increasingly prominent. The process involves harmful chemicals that are difficult to dispose of correctly, and the coating lacks additional vital surface features such as thermal insulation.
At Keronite, our scientists have developed advanced surface coating solutions that can substitute chromate conversion coatings without the use of harmful chemicals, whilst also providing additional surface features. As a result, engineers can utilise lighter metals to optimise designs in a greener and safer coating process.
What are chromate conversion coatings?
Chromate conversion coatings (CCC) are a protective surface solution used for their highly corrosive resistant and adhesive properties. The process involves submerging metal components in chromate acid where its surface oxidises, reducing hexavalent chromium (Cr6+) to the trivalent state (Cr3+). This creates a protective film on the metal’s substrate that varies in thickness according to how long the metal is submerged in the chromate acid solution.
CCC provides considerable protection from galvanic corrosion and minimises surface oxidation, which creates an adhesive primer to effectively apply paint coatings. These features led to its use in the aerospace industry during the 20th century to enable engineers to utilise aluminium components and reduce the weight of designs. Aluminium has an impressive strength-to-weight ratio, but is susceptible to galvanic corrosion; aircraft components also need to be painted white to reflect sunlight and reduce thermal absorption. CCC provided engineers with solutions to both these challenges, effectively improving the fuel efficiency via lightweight aluminium components.
What are the challenges of chromate conversion coatings?
One of the key challenges of using CCCs is the toxicity of the chromate acid solution. Hexavalent chromium compounds are highly carcinogenic, leading to irreversible adverse health effects to people that are exposed to the solution, as well as significant potential environmental damage. Because of this, hexavalent chromium compounds are highly regulated, and CCCs require a specialised disposal process of their waste products.
CCCs also lack additional insulating and protective properties past their impressive corrosive protection. In the modern engineering landscape for industries like aerospace, designers need a range of surface features to effectively integrate light metal components. One key example of this is structural aircraft components that need protection from thermal shock. These components face extreme levels of thermal stress in an extremely short amount of time, leading to cracks and irreversible damage to fatigue strength.
Plasma Electrolytic Oxidation - an effective chromate conversion coating alternative
Plasma Electrolytic Oxidation (PEO) is an advanced metal surface coating solution that provides a range of bespoke surface features for light metal components like aluminium. It utilises an electrolyte bath similar to hard anodising, but uses greater and controlled voltages to produce plasma discharges on the metal’s substrate. This creates a ceramic outer layer that is not only extremely resistant to corrosion, heat and wear, but produces an environmentally safe byproduct that can be easily disposed of.
A key feature of PEO is the porosity of the outer ceramic layer. These pores allow for the absorption of various reagents that are introduced in the electrolyte solution, enhancing surface characteristics that suit specific applications. For aerospace applications, Keronite has developed a CCC alternative that has innate reflectivity, corrosive protection and insulative properties that keeps critical systems cool; Introducing Keronite YF-2.
Keronite YF-2: bright white aluminium coating for aerospace
Scientists at Keronite have been working closely with aerospace industry partners to develop a new YF-2 bright-white coating. The brilliant finish provides protection against thermal shocks, sunlight exposure, and is also suited for satellites that are exposed to high levels of UV radiation. The high thermal shock resistance (MET 918) was tested by dipping components in liquid nitrogen (-198 C) and then immediately dipping them in boiling hot deionised water (100 C). The components showcased good coating-substrate adhesion (MET 918), and peel test showed no coating detachment.
The bright white coating of YF-2 exhibits excellent adhesion, good wear resistance, high hardness and good corrosion resistance. This was tested by placing components in a corrosive salt fog environment for 168 hours. These features combined make YF-2 a great candidate for aluminium alloys in a number of aerospace applications, and position it as an effective substitute to CCCs.
Utilise bespoke PEO solutions to optimise aerospace designs
Keronite’s YF-2 white aluminium coating expertly balances form and function in a single electrolyte formulation. It offers excellent corrosion resistance, hardness, and thermal insulation properties, making it a versatile option for various aerospace applications. Outside of aerospace, YF-2 is particularly suited for applications that necessitate both visual impact and high-performance, such as consumer electronics, architectural elements, and transportation systems.
Our team of advanced engineers develop a range of electrolyte solutions to suit the specific surface characteristics of different applications. The result is the extended lifespan of lightweight components that would otherwise need to be heavier metals to survive harsh environments.
To find out more about the details surrounding YF-2 white aluminium coating and our other electrolyte solutions, download our datasheet. Or, to find out more about how PEO can provide the surface characteristics you need for your application, contact us today.
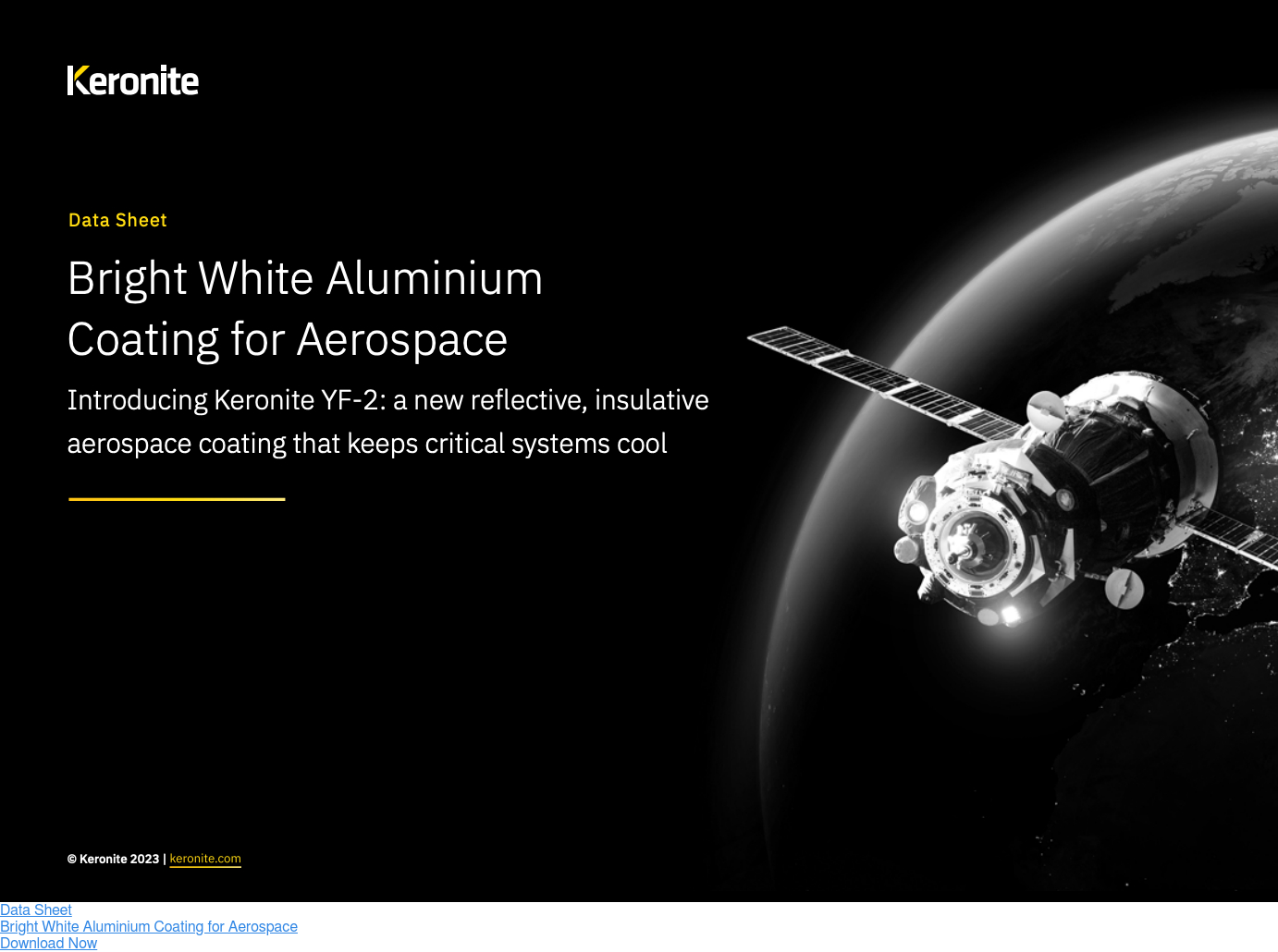
