AI brings new material challenges to unmanned aircraft & drones
20 September 2022Unmanned flight is a relatively new phenomenon. So materials scientists are investigating techniques to improve the performance of these autonomous planes and drones in unique ways.
In 1998, the world’s first unmanned transatlantic flight was made. Since, military and civilian applications for drones have become ubiquitous. From sophisticated military intelligence missions to precision agriculture, the use of drones has become more vital to the economy and society. But the applications do not end there. As technology advances, the mechanical limitations of drones are becoming well known. Scientists at Keronite are working in partnership with leading aerospace manufacturers to solve each of these issues.
New applications for unmanned aircraft and drones
Defence | Civilian | Dual |
Reconnaissance | Precision agriculture | Land and maritime surveillance |
Combat and defense | Cinematography | Delivery and transportation |
Communications relay | Manufacturing and construction | Entertainment |
Cargo transport | Public health monitoring | Earth imagery and mapping |
Precision strikes | Environmental monitoring | Search and rescue |
Drones: the new mechanical requirements
Artificial intelligence is advancing every year. Machines are now capable of completing far more tasks without human intervention. The most prescient demonstration of this is in industrial settings – where robotics actively automate tasks previously only a human could do.
With sophisticated algorithms, more drones are shifting from being remote controlled to being completely autonomous. Sophisticated sensor technologies are enabling drones to complete tasks with minimal instruction.
But as technology advances, unmanned drone technology is beginning to look restricted in another way: materials and hardware.
Great expectations
The defense sector is investing heavily in materials technologies that extend the amount of time a drone can spend in the air. Also, as investments increase, the expectation is that maintenance costs will also fall.
Composite materials – carbon fibre and carbon-reinforced plastics, for example – are used widely in drone technologies. And for good reason – they are lightweight, offer high strength to weight ratios and are relatively inexpensive. Composites are excellent choices for many parts of drones. But where even greater strength is required, light alloys are still the go-to materials.
New objectives
Now drones are equipped with numerous advanced sensors and cameras, the attention has turned to what value they can add within their existing applications:- Maximising efficiency, so drones can spend more time unmanned in the air.
- Increasing autonomy. Introducing new features that enable drones to add more value to their applications.
- Speed. In defense applications, timing is everything. Enabling drones to be faster and more responsive can add unprecedented value within their applications.
- In defense applications, radio reflectivity and specific aesthetics are crucial to performance.
- Reducing maintenance and running costs. Where budgets are tight, minimising the maintenance requirements and improving fuel efficiency is imperative.
Each of these requirements puts new pressures on the materials that makeup a drone.
The scale of the materials challenge
As the benefits of drones become clearer to a vast array of industries, there is significant interest in boosting the performance of drones.
Aluminium, magnesium and titanium are used throughout the military sector. Light alloys are used primarily for their high strength and low weight, which makes them primary candidates for drone applications. But as the possibilities introduced by artificial intelligence grows, the expectations upon materials does, too:
More time in air
For the most part, drones spend much of their time on the ground. This isn’t because they are wanted in the air – it’s simply because of the energy and costs associated with keeping them in the air. But in order to detract more value from drones, the more time they can spend in the air, the better.
To improve the time spent in the air, the total energy consumption must be reduced. Else, drones will be carrying excess fuel – often in the form of heavy battery packs – which creates a paradoxical design decision. At what point does the extra weight of fuel/power detract from flight time?
Lighter materials are able to help with this. By reducing the weight of the drones structure, the drone will be more efficient and able to carry a greater payload. This is where light alloys become invaluable. Swapping out heavier metals like steel for lightweight alternatives makes a great deal of sense.
More unmanned capabilities
As software and artificial intelligence capabilities continue to improve, the scope for what drones can do is growing. Not only can they help capture data, but they can make decisions and operate with minimal human intervention. But to enable this, we’re likely to see drones equipped with more sophisticated equipment – all contributing towards a much more complex design.
This added complexity brings new materials challenges. For one, there are more components that need to perform well. This makes the materials and surface coating selection process much more involved. Large-sized drones come with significant design costs, thus making it all the more important to protect intricately designed components.
To enhance the performance of materials, advanced surface coating options like plasma electrolytic oxidation (PEO) are able to offer unique protection from an array of mechanical challenges.
Speed. In design and in performance
The speed of human progress is speeding up. Unmanned drones need to be just as well suited to tomorrow’s challenges as todays. To enable this, the design process needs to take into account the scope of change in the future.
To make this the case, structural materials need to be built with advanced technology – meaning they won’t become outdated quickly. Materials should also be bespokely coated, enabling their best performance possible with today’s technology.
Materials science partnerships are perhaps the best way forward. Working closely with a team that will enhance your materials will ensure that every component is able to perform to its maximum; enabling new opportunities to improve the design.
Droning on up?
Keronite’s materials scientists create the world’s most advanced surface coatings for light alloys. Naturally, the bespoke coatings made at Keronite’s Cambridge-based technology centre have become central to the performance of unmanned drones and planes. As world leaders in plasma electrolytic oxidation technology, Keronite’s coatings are able to offer unique performance improvements over other comparable coatings.
To learn more about plasma electrolytic oxidation (PEO) technology, download the What is Plasma Electrolytic Oxidation? White paper. Or, to get in touch with Keronite’s technical team, reach out to us on our contact page.
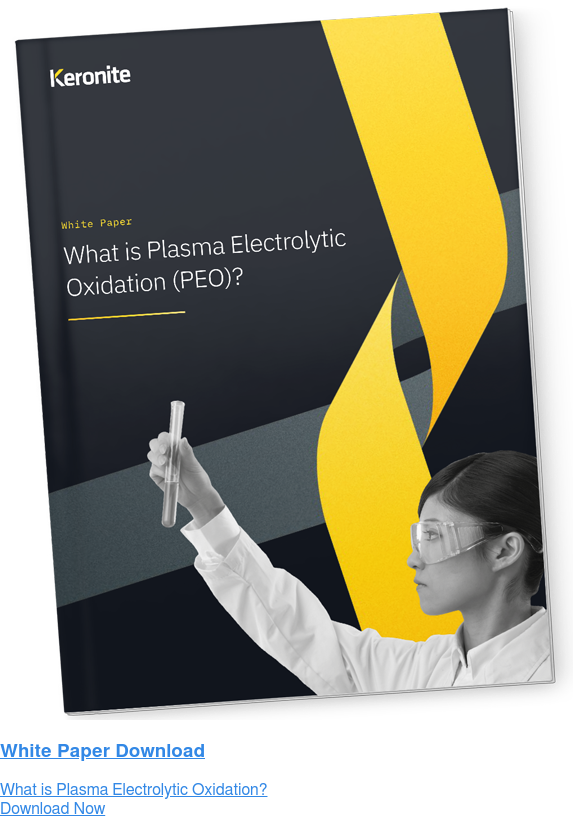
