5 trends that will define surface coating technology in 2021
24 February 2021Advances in science and engineering both solve problems and generate fresh challenges – for every tech breakthrough there is an emerging supply chain of materials, processes and technology needed to exploit it.
Materials science and engineering generally, and surface coatings specifically, play a key role in commercialising laboratory breakthroughs. They enable what was previously impossible or impractical, for example by using surface coating to make light metals withstand highly corrosive and high temperature environments. Coatings also accelerate the development and adoption of new technologies.
Here are five trends that will come to dominate 2021 and in turn, drive the direction of materials and surface coatings development:
1. Pandemic response and preparedness
The coronavirus crisis of 2020 showed how poorly prepared much of the world was in its capacity to respond to a global pandemic, despite the early warnings from previous regional pandemics such as SARS, Ebola and MERS. However, it also showed what a truly creative, collaborative, unrelenting and resourceful species humankind can be when faced with threats on a global scale.
Pandemic-driven innovation spanned examples such as pivoting existing supply chains and infrastructure from making diggers into making ventilators, to a dozen world-class vaccines created in a tenth of the time it typically takes. The Manufacturer has published a database of a huge range of companies that pivoted their core activities into production that directly supported the pandemic response. The challenge is now to prepare for the next pandemic that is undoubtedly ahead.
The range of solutions being developed to help combat pandemics is huge. The European Commission alone is funding over a dozen digital health programmes addressing pandemics that include novel air decontamination systems, diagnostic tests and telemedicine platforms. During 2020, Keronite received an InnovateUK grant to expand its development of antiviral coatings for light alloys that could reduce disease transmission via metal surfaces.
2. Nanostructures and nanomaterials
Underpinning the opportunities offered by nanotechnologies is how materials behave like both waves and particles at nanoscales, 1-100 nanometres (there are 1 million nanometres in a millimetre). In materials sciences terms, nanomaterials have a large surface area compared to volume. That means more of a nanomaterial is in contact with the matter around it, with resulting greater reactivity.
There are nanomaterials applications under development and/or due for release in 2021 that would sound like science fiction if they were not so close to commercialisation. They include using nanomaterials as carriers of dental repair products, enabling teeth to repair themselves. The same approach could be used to support osseointegration of medical implants.
A team of US and Israeli researchers have found a way of using DNA alongside superconducting niobium and silicon to create 3D superconducting nanostructures. The technique, called DNA origami, has applications in medical and geophysical sensors and quantum computing.
And introducing titanium dioxide nanoparticles, tiny super-catalysts, into plasma electrolytic oxidation (PEO) surface coatings can introduce photocatalytic characteristics that in turn provide antimicrobial properties on the surfaces of light metals.
3. The rise of the smart factory to accelerate manufacturing speeds
By 2025, the main manufacturing competitive driver will be smart factories. That is according to research by Deloitte, which shows that 86% of US manufacturers believe smart factories “will be the main driver of competition”, and 83% “believe that smart factories will transform the way products are made”.
The smart factory is the product of genuine digital transformation and will include elements of the internet of things (IoT), Industry 4.0, artificial intelligence and machine learning, big data, analytics and the cloud, supply chain ecosystems sharing common platforms and additive manufacturing.
At the process engineering level, manufacturing speeds have three bottlenecks: process limits, system limits and coordination limits. Alongside the IT tech solutions above, manufacturers are introducing cobots to support and speed up the human, or system, part of the manufacturing process.
And additive manufacturing is finally coming of age. For example, surface coatings enable a much broader range of additively manufactured light metal components, enabling the approach to accelerate the production of complex parts for applications in industries such as medical, dental and aerospace.
4. Space communication systems
Much of the tech we take for granted today was originally created to meet a space-related challenge. Consumer products from running shoes to camera phones have a root in space travel. And driven by the huge growth in commercial space activity, such as satellite launches and space tourism, this trend is accelerating.
An exciting new engineering hub for the development of 5G and satellite technology will be completed in 2021. According to the UK Space Agency, the hub will: “provide a testing facility that can show the benefits of hybrid 5G and satellite communications networks.”
To survive the extreme temperature contrasts in space, from -170 to 500 degrees centigrade, the external surfaces of spacecraft, satellites and probes require thermal and cryo barriers. Keronite has worked with the European Space Agency (ESA) and the Japanese Aerospace Exploration Agency (JAXA) to create the thermal control surface coatings for the light metal components of the Bepi Colombo mission to Mercury.
5. Increasing collaboration/partnership in the UK space industry
According to the UK Space Agency’s International Director Alice Bunn: “There are over 100 space faring nations across the world now, many of which are looking to collaborate with the UK.” Commercial activity in the space sector is exploding – in 2019 alone, space companies benefitted from $5.8bn of private investment.
Whilst most of this was soaked up by the big players such as Virgin Galactic, SpaceX, Blue Origin and OneWeb, initiatives such as the UK Government’s international space collaborations are designed to fund the smaller scale projects. This is coupled with organisations such as the Satellite Applications Catapult, a UK-based business dedicated to linking academic and industry research with organisations that have an application needing a solution.
A great example of the potential public-private partnerships that can be delivered is Keronite’s contribution to the BepiColombo project, shown above. Other partnerships with Airbus and ONERA are underway.
Collaboration and partnership in the UK space industry received a further boost in the final months of 2020, with the announcement that new space hubs will be created in 2021, following the successful model of the Harwell Hub in Oxfordshire, which is the home of the 5G project highlighted above. The UK Space Agency is expected to unveil a new programme of activity for 2021 that will include partnerships between government and local enterprise agencies, academic research and businesses.
The combination of the pandemic and resulting global economic downturn has meant 2020 was a tough year for many organisations. However, every challenge becomes an opportunity when viewed through a different lens. Combating coronavirus, the drive for ever more efficient and responsive manufacturing, space sector growth and the health benefits of nanotechnology look set to make 2021 an exciting year.
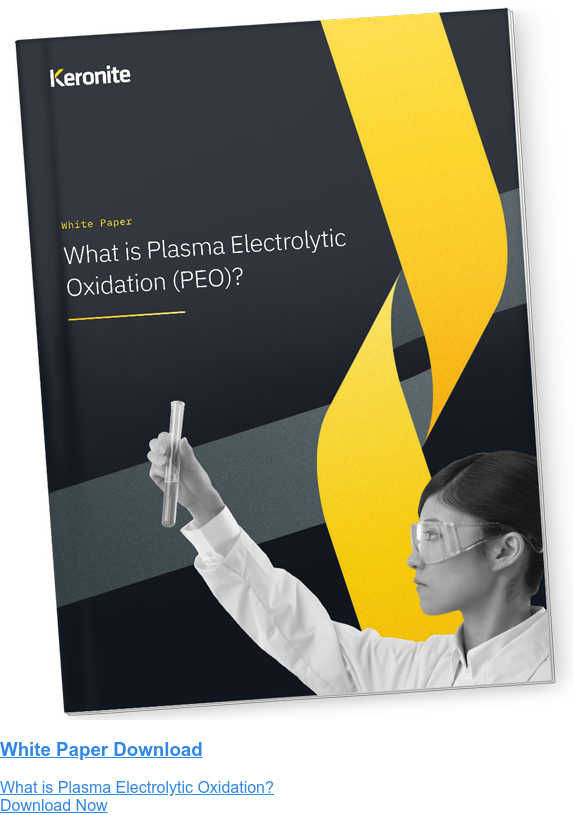
