3 high-performing alternatives to DOW17 coatings
23 May 2022As protective surface coatings for magnesium go, the most favoured solution until recently has been DOW-17. As a type of anodizing treatment popularised in the 1940s, the coating uses chromate and/or fluoride-containing electrolytes. In recent years, these have been outlawed, as chromate is toxic and fluorides are also harmful. Now outdated, advances in alternative surface technologies may offer a superior solution.
What is a DOW-17 coating?
The DOW17 metal coating treatment was invented by the Dow Chemical Company in the 1940s, creating the world’s first anodised magnesium coating. The anodic process renders treated magnesium components with a green surface finish, and this coating gives enhanced protection against corrosion and abrasion. Whilst the process does provide good paint adhesion, it has largely been replaced by more advanced metal surface treatments that give better performance against the three key disadvantages of the DOW17 process:
- Poor resistance to salt spray, thus giving minimal protection from corrosion in marine environments
- High porosity gives low protection against corrosion
- It uses chromium (VI), a known carcinogen and banned from use in the EU after September 2024
Thanks to modern material science, engineers looking for high-performing materials that are both lightweight and long-lived have a number of alternate options for improving metal alloys, and we consider the benefits of three such processes here:
What suitable alternatives are there to DOW-17 coatings?
Tagnite
Tagnite was developed by Technology Applications Group (TAG) in order to improve the corrosion resistance of magnesium alloys and remove the environmental and health concerns surrounding DOW17 coatings. Today the process is predominantly used in the defence and aerospace industries.
Tagnite’s anodising coating process causes magnesium alloys to develop a hard, smooth oxide layer with pores up to 10x smaller than those found in DOW17 coatings. Treated surfaces have high levels of abrasion resistance and offer good adhesion for paint.
A major disadvantage of the technology however, is that it is only used on magnesium, severely limiting its use.
Anodising
Whilst more resistant to corrosion than magnesium, aluminium is still susceptible to environmental deterioration. Through the process of anodising, aluminium components undergo a chemical reaction that forms a smooth and hard wearing anodic surface layer. The longer the metal is in the bath, with an electrical current passing through it, the thicker the protective layer is formed by oxides developing on the surface.
Anodised aluminium remains pure and fully recyclable, and components can be coloured with the addition of dye into the electrolytic bath. Because the colour is integrated into the metal substrate, anodised aluminium will not fade, chip or peel over time and the finish is UV-stable. The anodising process improves both durability and wear resistance of aluminium parts, ensuring long-lasting performance and thus delivering maintenance cost savings and reduced equipment downtime for component replacement.
Disadvantages of the conventional anodizing process include:
- Unsuitable for all grades of aluminium
- Colour inconsistency between batches
- Relatively expensive for small-scale production
Plasma Electrolytic Oxidation (PEO)
Developed by Keronite, Plasma Electrolytic Oxidation is a bath-based method of producing ceramic layers on the surface of light alloys. PEO’s two-stage method strengthens and seals the surface of metal alloys through:
- Oxidation of the substrate in a bath of proprietary dilute aqueous solution
- Plasma modification, altering the microstructure to improve corrosion resistance and fatigue strength
Unlike Tagnite (suitable only for magnesium) and anodising (treating aluminium), PEO can be applied to a number of light metals - the process is suitable for alloys of high aluminium, magnesium and titanium composition, along with zirconium, tantalum, niobium, hafnium and cobalt. PEO is therefore a highly adaptable and versatile solution for engineering projects.
PEO surface coatings bring a wide range of practical advantages when applied to light metal alloys, retaining full recyclability whilst also improving the performance of the materials:
- Wear resistance
- Corrosion protection
- Thermal management
- Hardness
- Fatigue performance
- Adhesion
Advanced surface technologies for replacing DOW-17 coatings
There are a number of potential substitutes for DOW-17 coatings. Materials scientists are continually improving the performance and processing efficiency of alternatives, as well as adding new characteristics to materials.
Keronite is the world’s leader in plasma electrolytic oxidation (PEO), an advanced surface technology used by many as a high-performance alternative to DOW-17. The process provides:
- Crack-free surfaces. Traditional anodising can result in cracks forming in the anodic oxide layer, making materials susceptible to wear in extreme temperature conditions. Through the use of plasma, the microstructure oxidised coatings take on an irregular form that protects them from cracking and improves performance in harsh temperatures. PEO’s inert ceramic structure provides excellent natural chemical stability and corrosion protection that outperforms traditional anodising in salt spray testing.
- Inert waste products. Aluminium hydroxide and degraded sulphuric acid are created during anodising, causing fumes that are harmful to workers and the environment and are difficult to process safely. With PEO, no organic compounds, VOCs, strong acids or heavy metals are used during the process. PEO uses 99% distilled water and the leftover liquids are no more hazardous than run-off water from a domestic washing machine.
- Bespoke finish. Keronite’s material scientists can adjust PEO processing parameters to produce tailored solutions that meet the brief of almost any engineering project.
In recent years, materials scientists have found novel techniques to uniquely manipulate the processing parameters to enhance coatings across a number of characteristics. This means PEO coatings can be created bespokely to an application – providing an all-encompassing solution against the specific challenges.
You can learn more about the many benefits of plasma electrolytic oxidation for magnesium alloys in the technical data sheet.
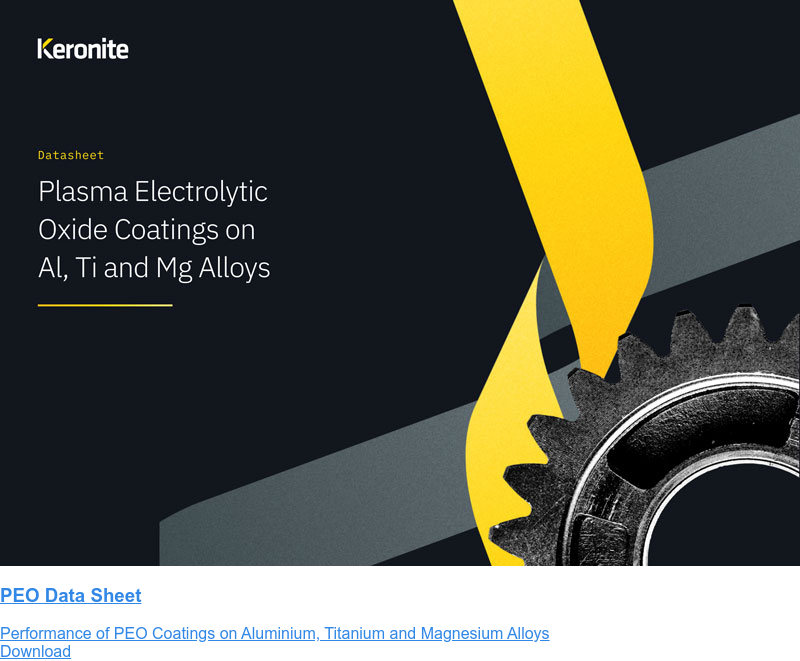
