Breaking barriers with dielectric breakdown strength coatings
9 October 2023Society has an insatiable demand for power and it keeps on growing. Across the world, electrical power consumption continues to increase, with more electrical devices being manufactured, sold and used. Demands for power hit record levels in 2019 and, although the speed of growth has slowed, demand is still growing.
The energy industry is constantly looking for new innovations to help increase the capacity of their infrastructure. One change these companies are making is to look at higher electrical fields, however, this requires reinventing a lot of equipment.
Consumer electronic trends are also raising the bar with the dielectric strength of materials. Engineers are seeking to design miniaturised, yet efficient equipment and devices. From a purely functional perspective, materials need to boost their dielectric strength to cope with this trend. But there is a third trend making dielectric characteristics all the more vital.
Electrification, the global movement to move from fossil fuel power to pure electric, is forcing engineers to consider the dielectric strength of their materials. Electric vehicles are the most well-known example of this, but every industry and even households are replacing their equipment in an effort to clean up and electrify.
Materials, especially aluminium, are being examined by materials scientists. In an effort to boost their performance in these applications, advanced surface technologies (like plasma electrolytic oxidation) are offering novel solutions.
Dielectric characteristics and dielectric breakdown strength
From a materials perspective, there are fundamental changes necessary for a future of highly efficient components. That’s not just from a lightweighting perspective; enabling products to operate with much less mass (and use less gas), but from a performance and functional perspective.
Dielectric characteristics within many applications offer opportunities to improve performance, enabling efficient energy capture and storage – meaning we’re able to generate more power from renewable energy sources. All the while, dielectric materials in semiconductors enable devices to continue miniaturising without inhibiting performance.
Dielectric characteristics describe a material in which electrons are tightly bound to the nucleus. They are without free electrons to carry current, which means they aren’t free to move under the influence of a foreign field. As a result, they are electrical insulators. This phenomenon can be used in various applications, which are becoming increasingly important as global trends accelerate.
Coating techniques that can finely control the dielectric performance of materials are of increasing interest across a variety of sectors. Charges within dielectric materials can be tightly controlled with advanced surface coatings, which can modify how materials respond to charges and how electrons relax following a charge. Through materials science, we can therefore tailor the capacitance and conductance as predefined electrical fields.
Dielectric materials: an increasingly important trait of light alloys
Dielectric materials are electrical insulators that may be polarized by an electrical field. Dielectric strength measures the effectiveness of this insulation: with stronger materials able to resist dielectric breakdown at higher voltages.
There are dozens of applications for materials possessing dielectric qualities. These include semiconductors, compact circuit board components, scientific and optical instruments (as neutral density filters, for example). Electronic components that possess higher dielectric strengths may be placed more closely to one another without the risk of electromagnetic interference issues. Other applications include capacitors and displays.
Plasma electrolytic oxidation for high dielectric strength
Ceramic materials are often used in high dielectric strength applications, as are many polymers. Ceramic naturally offers superior dielectric performance to many metals and plastics, offering up to 1015 Ω.m of resistivity and 17 to 40 kV/mm of dielectric strength.
The oxide layer formed on aluminium coatings has a slightly lower dielectric strength than alumina ceramics – around 15 kV/mm. However, for the majority of applications this is not sufficient. However, with the addition of an advanced surface coating, the dielectric strength of an aluminium alloy can be increased to as much as 59-79 kV/mm.
Coatings created by plasma electrolytic oxidation (PEO) excel in high dielectric strength applications. The process involves stimulating plasma discharges at the surface, which instigates the growth of a ceramic oxide layer. The thicker the oxide layer, the greater the dielectric strength of the surface.
Another benefit of the technique for dielectric performance is the process involves conversion of the substrate. This means that the protective dielectric coating adheres strongly, whereas alternative techniques deposit an additional layer on top: which can be prone to cracking and wear over time, decreasing the life of the dielectric strengthening coating.
And, finally, the PEO layer can be created and tailored for a range of requirements, which could include thermal and optical properties in combination with dielectric strength.
Summary
- Increasing electrification and growing demand in electricity consumption has created a quandary for engineers.
- Coatings with high dielectric strength enable engineers to create miniaturised electronics, while improving the performance of components prone to dielectric breakdown.
- Plasma electrolytic oxidation (PEO) is an advanced surface technique that uniquely increases the dielectric breakdown strength of aluminium (and other light alloys), while delivering superior wear, corrosion and thermal performance.
For more information about Keronite’s research and recent findings in high dielectric breakdown strength coatings for aluminium, get in touch with Keronite’s technical experts here.
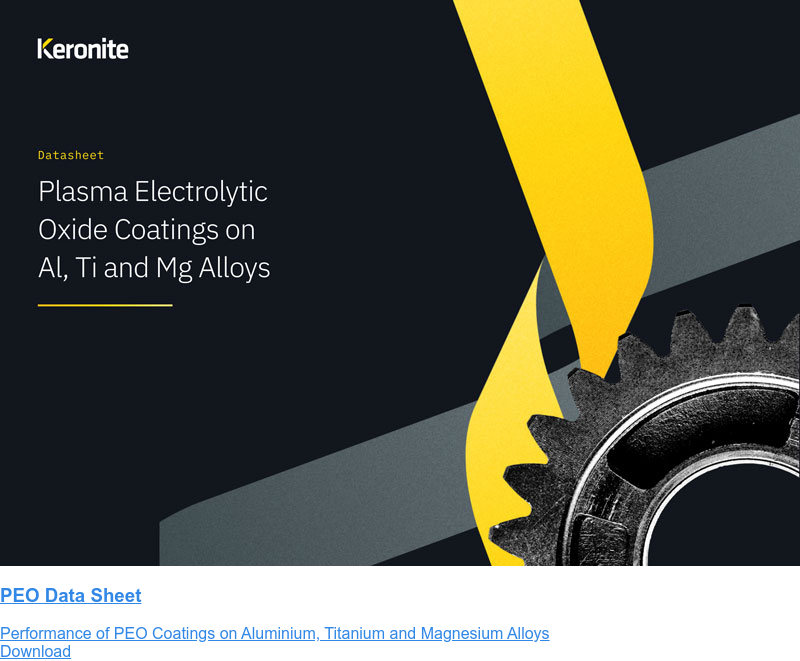
